EPDM Granules Wearing Course for Playground Surfaces
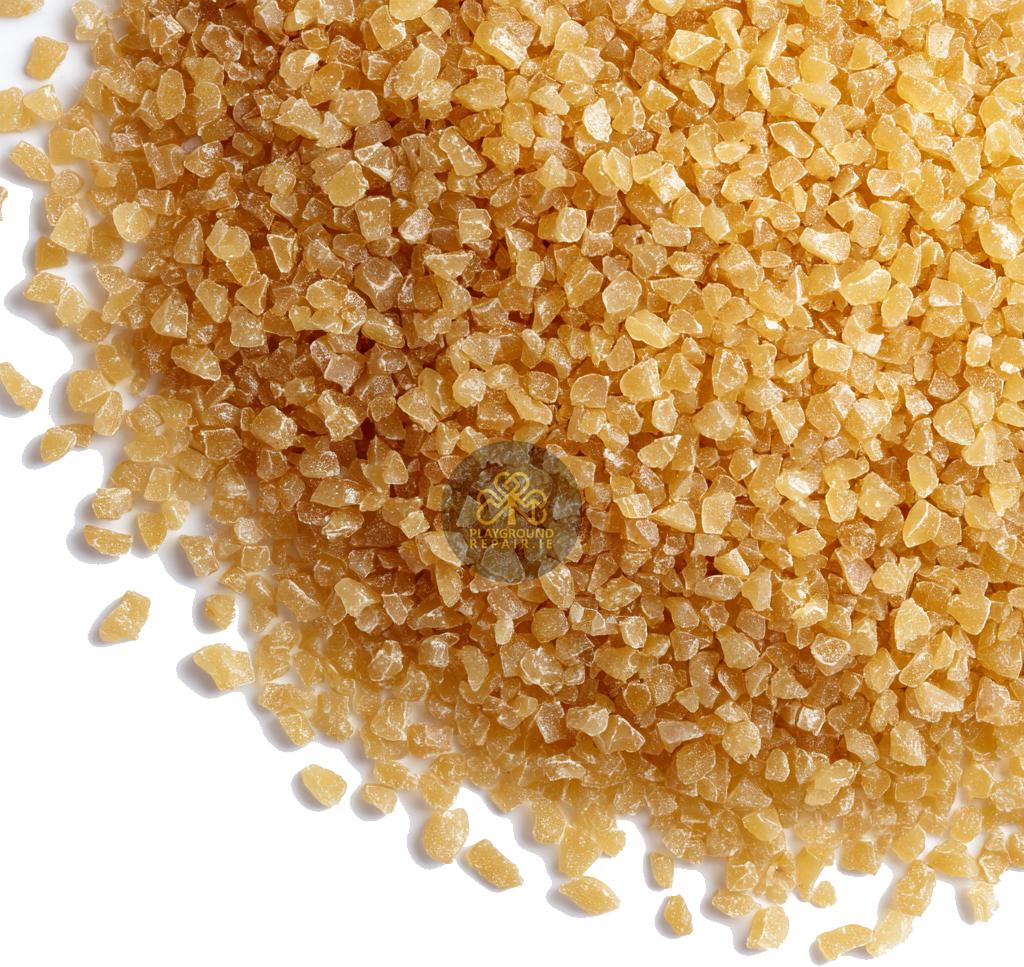
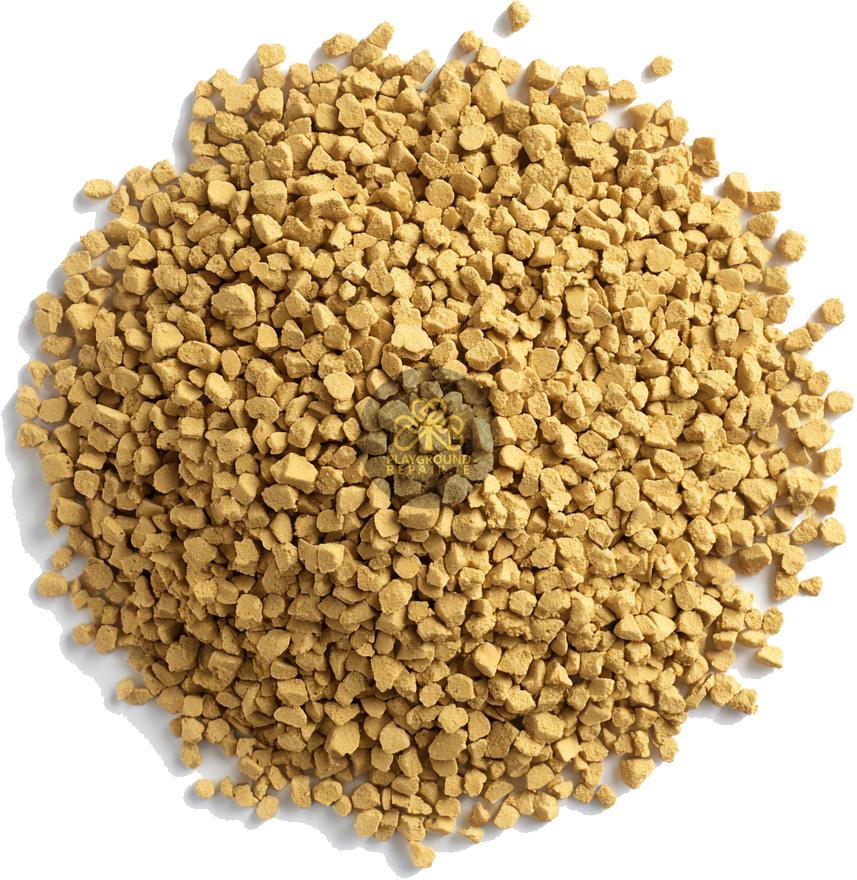
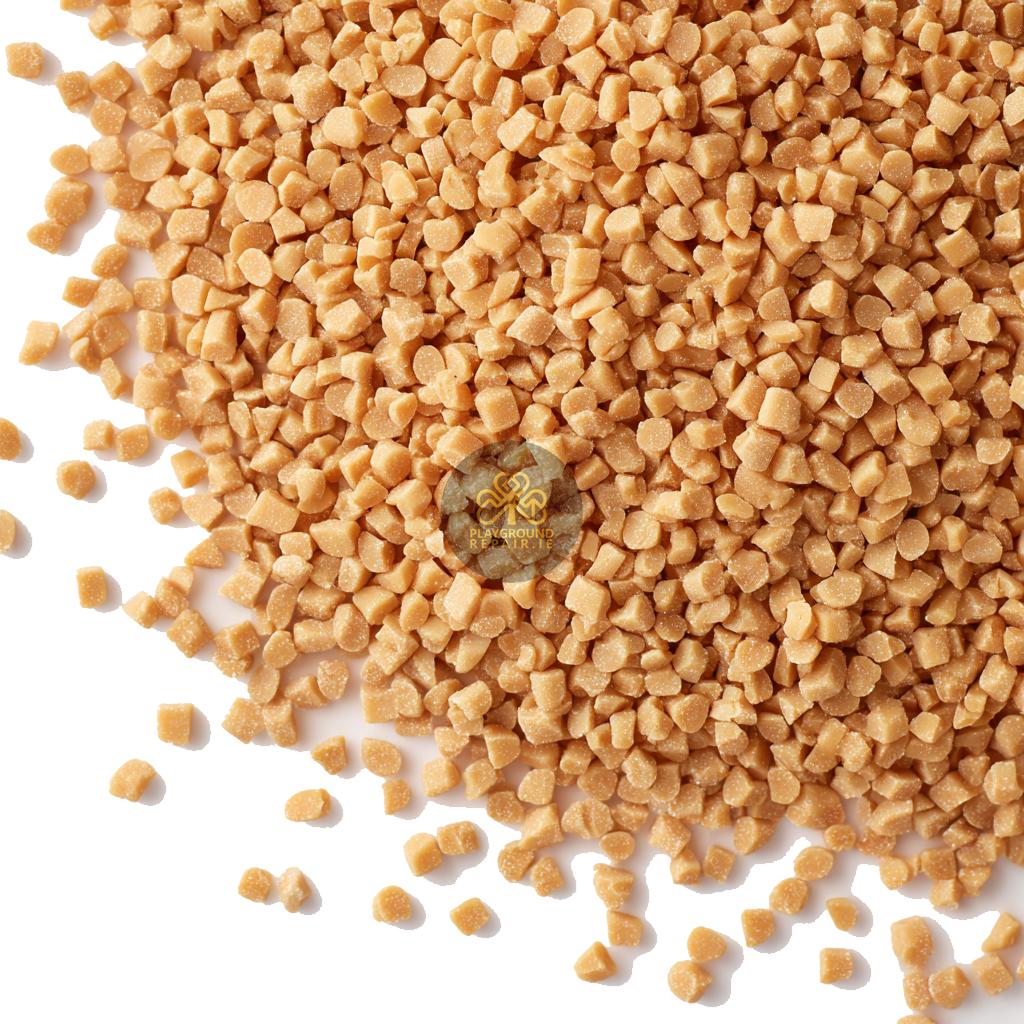
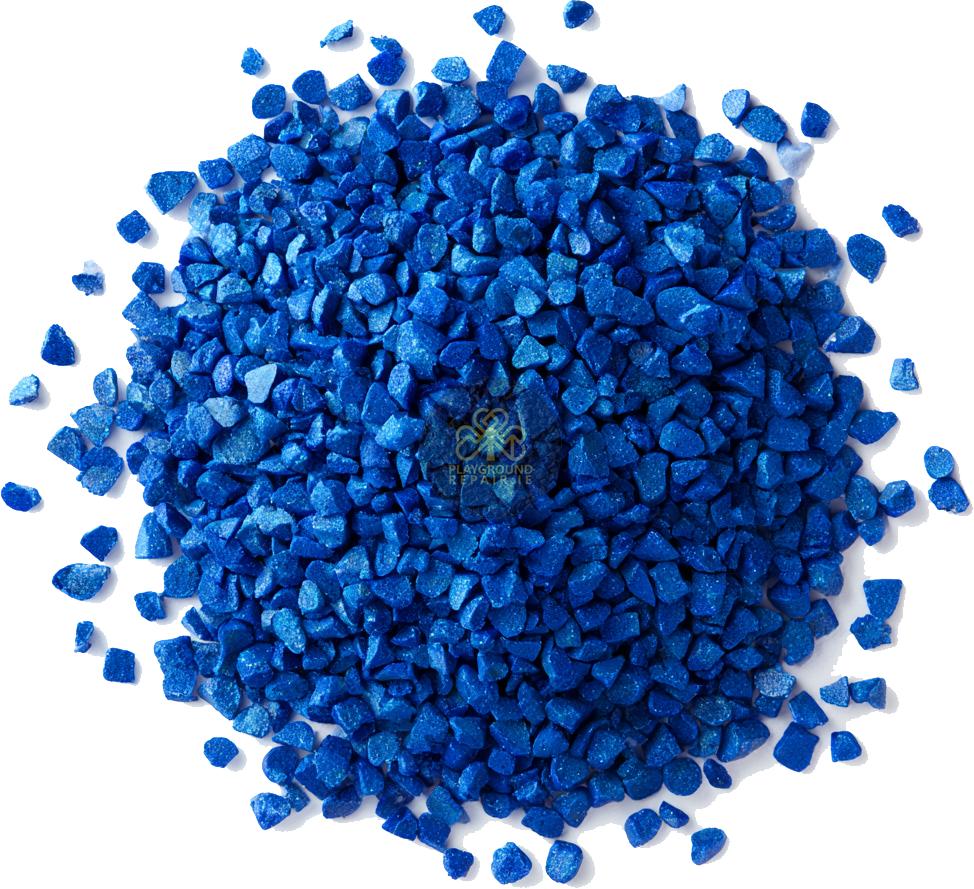
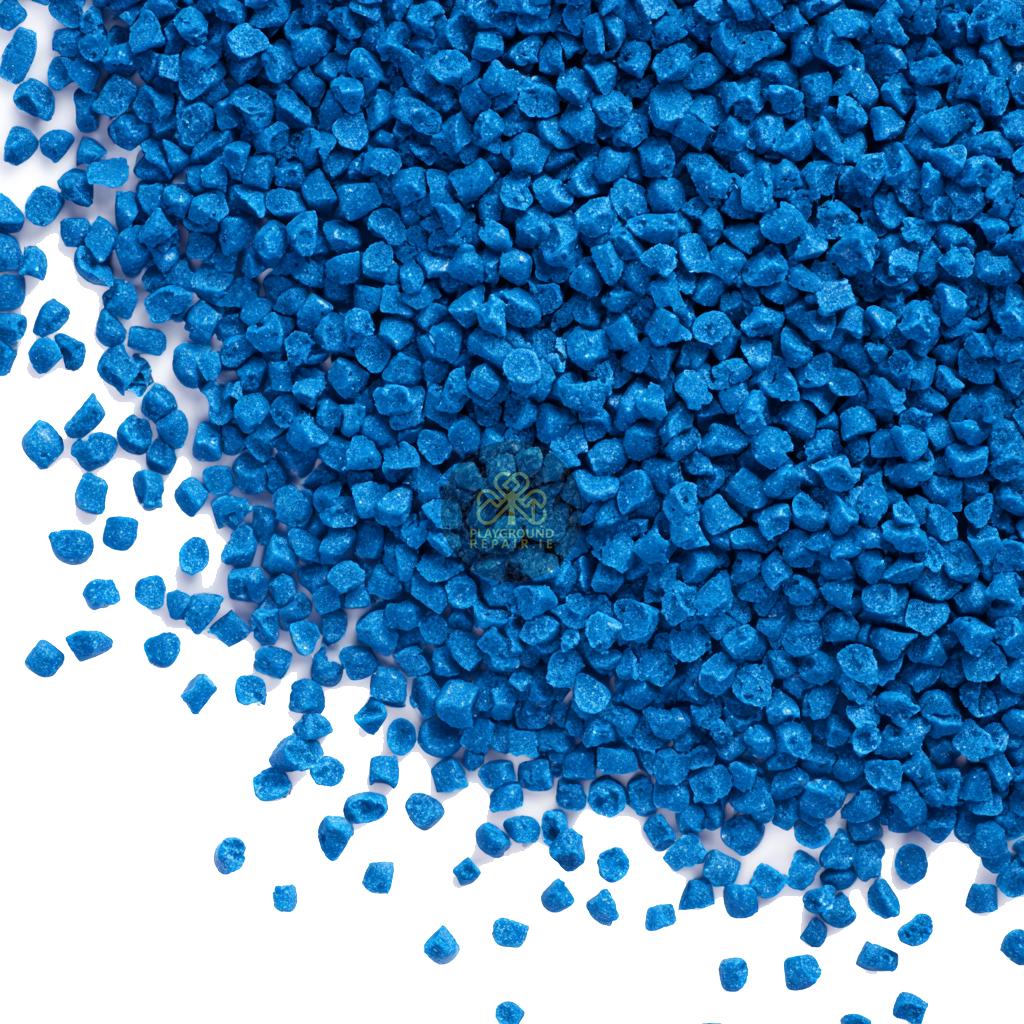
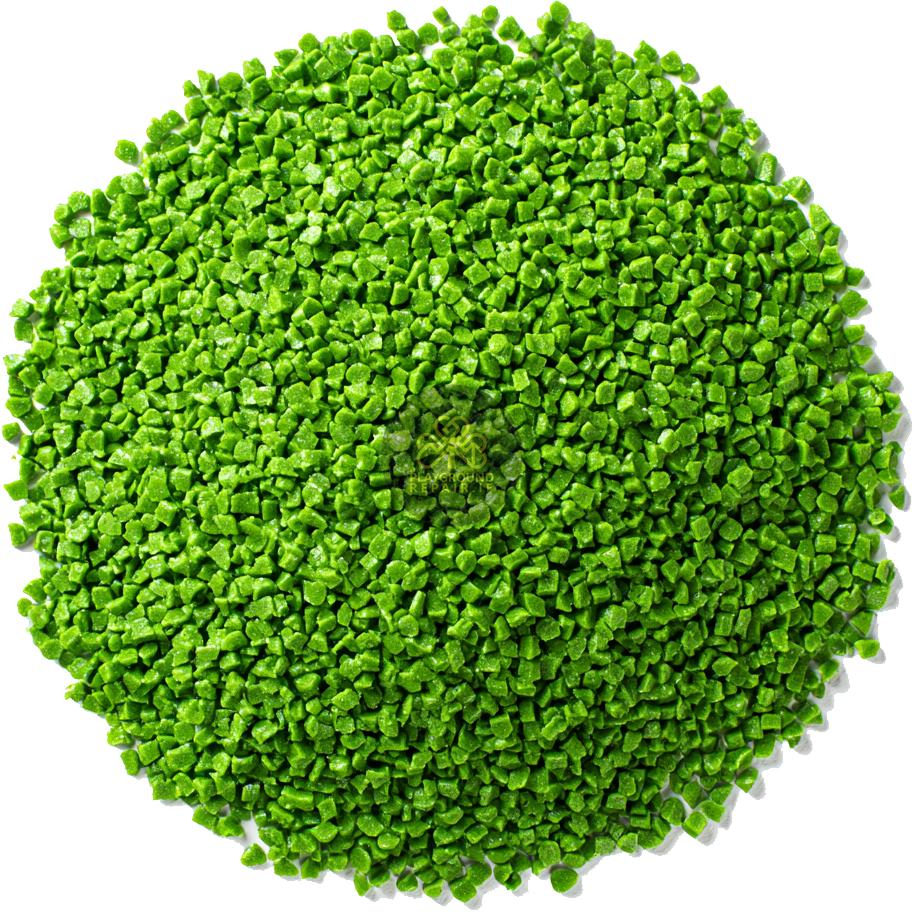
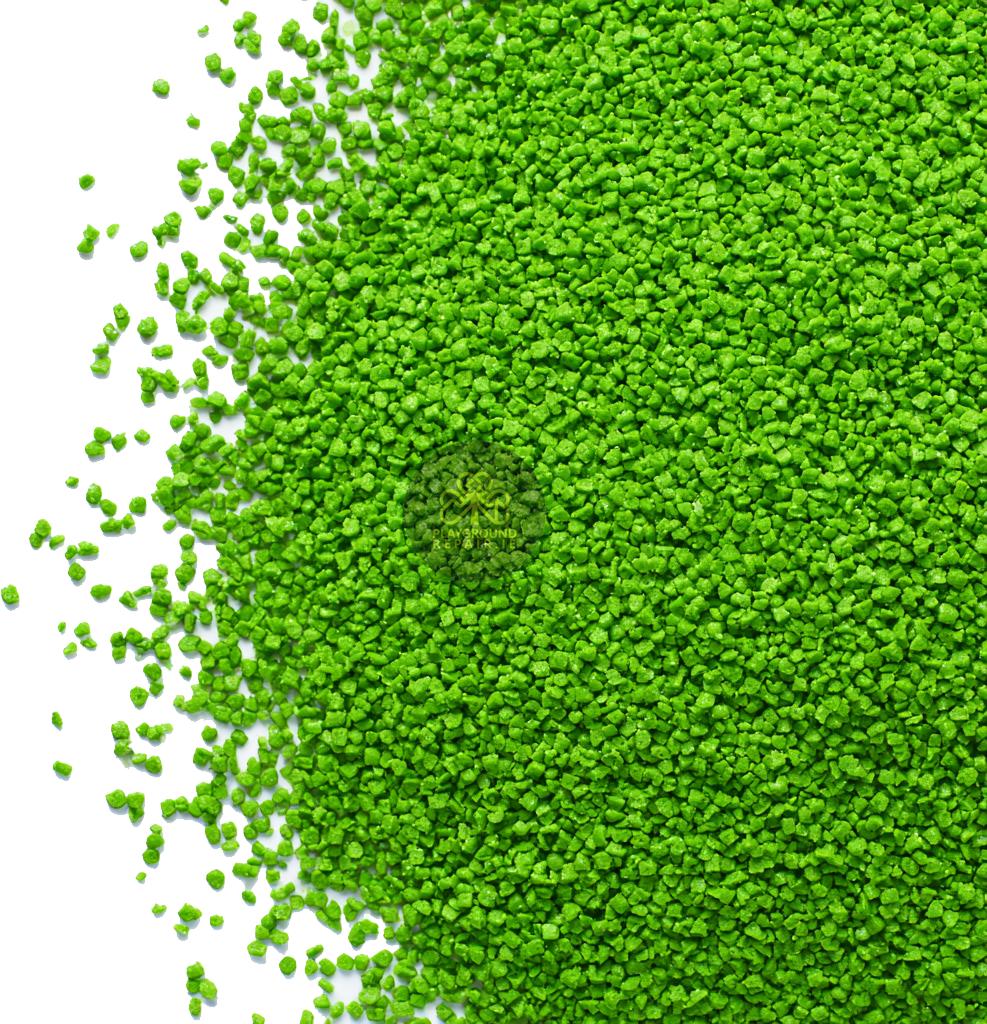
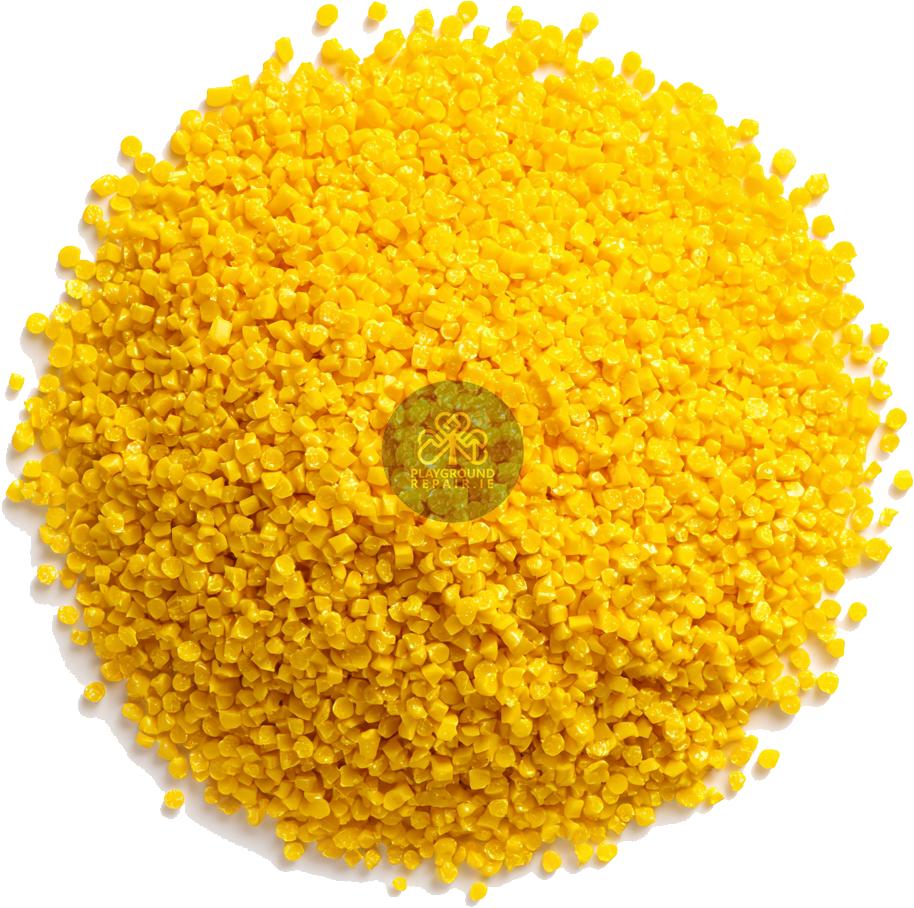
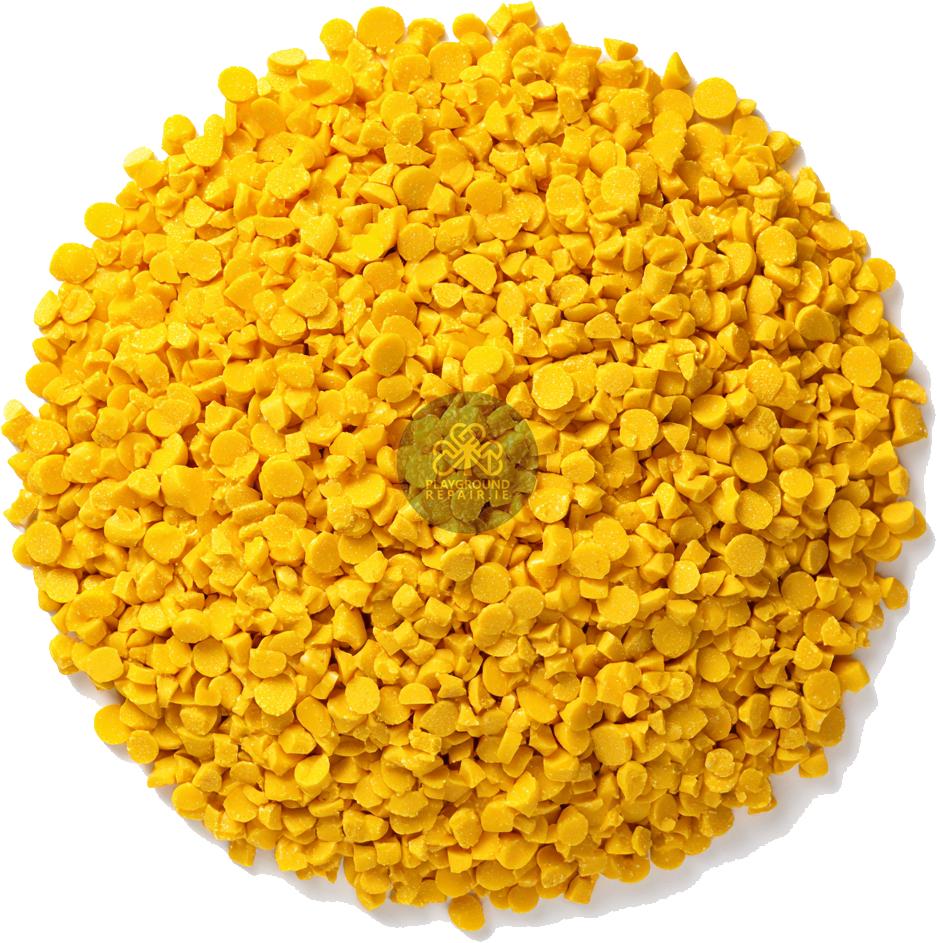
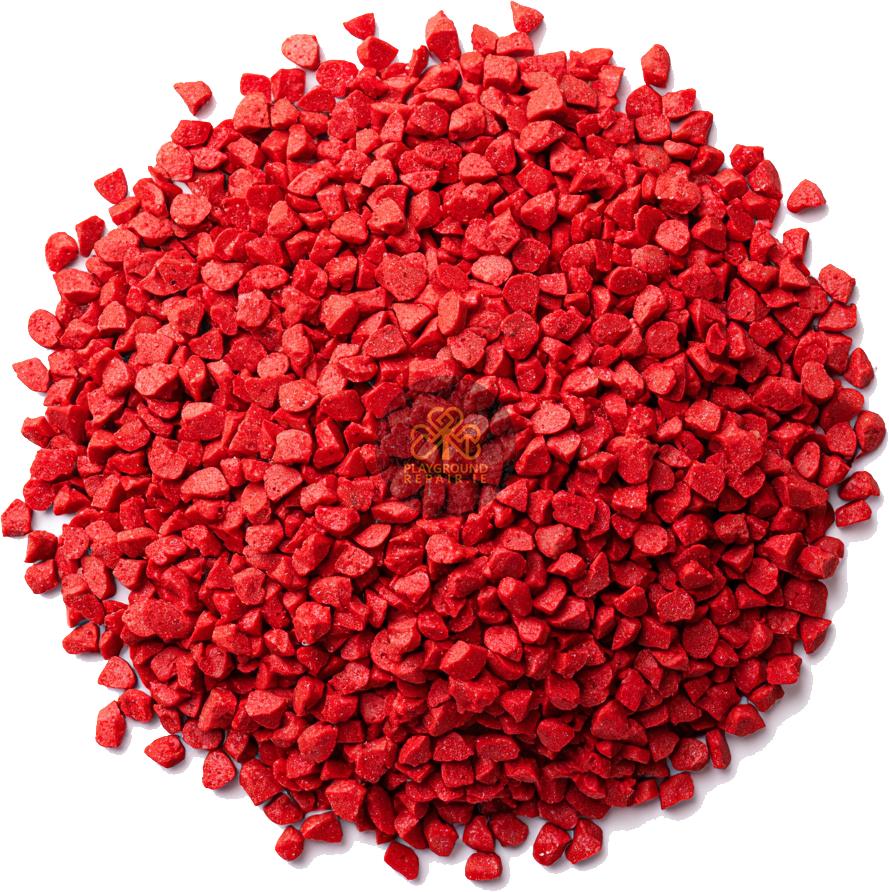
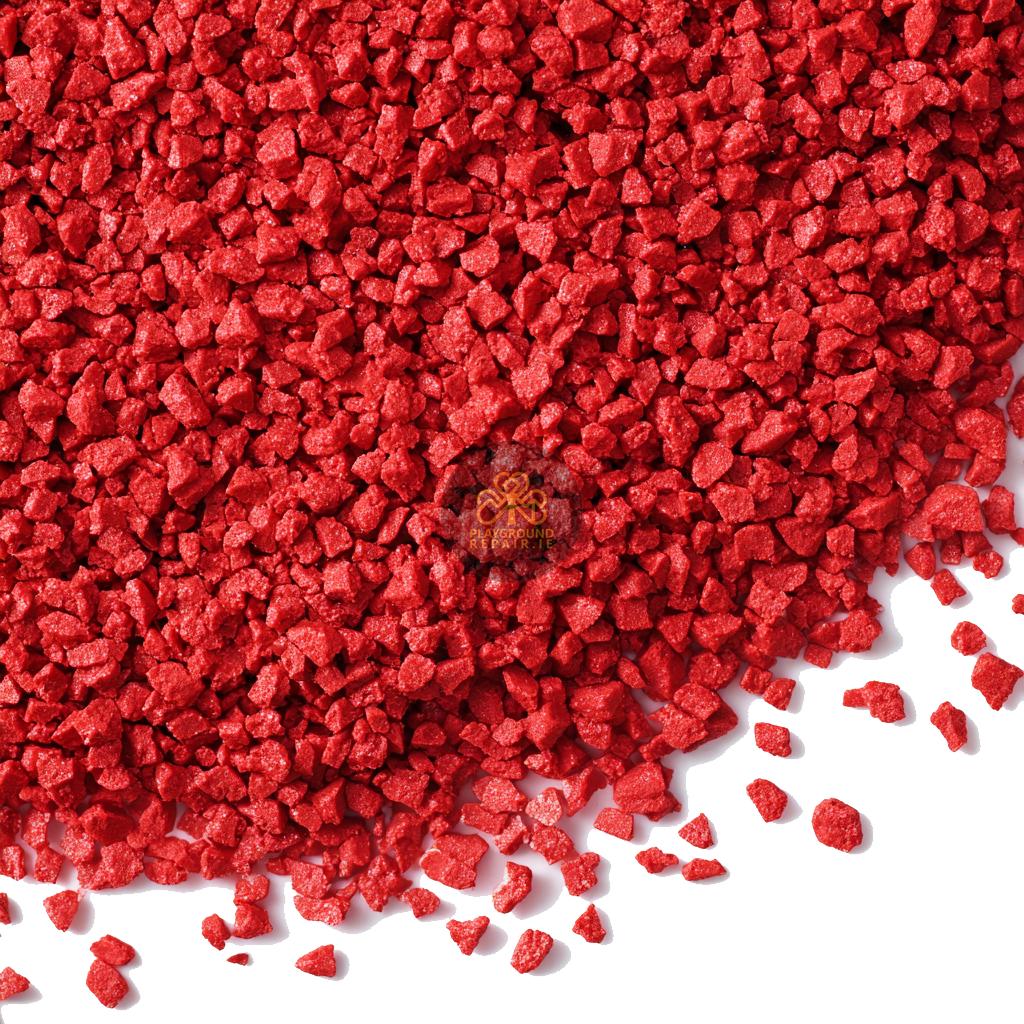
EPDM Granules
Key Benefits of EPDM Granules
- 🎨 Vibrant, Long-Lasting Colour
- ✨ Creative Design Flexibility
- 💪 Exceptional Durability
- 🤸 Superior Elasticity & Safety
- ♿ Seamless & Accessible
EPDM Granules Calculator
These granules form the top 'wearing course' of a traditional two-layer wetpour system, installed over a base layer of SBR rubber. When mixed with our premium Aliphatic Binder, they create a seamless, flexible, and porous surface that is perfect for incorporating intricate shapes and logos. Offering superior elasticity and a wider range of bright colours than any other material, EPDM is the professional's choice for a high-end, durable, and visually stunning safety surface.
What is the difference between EPDM and SBR Granules?
This is the most common question in wetpour surfacing. Both are rubber granules, but they have very different roles and properties.- SBR Granules (Styrene Butadiene Rubber): This is the base layer or "shock pad" of a wetpour system.
- Origin: It is a lower-cost material, typically black, made from recycled vehicle tyres.
- Function: Its primary job is to provide the impact absorption and critical fall height protection. It is installed at a greater thickness (30mm - 150mm) directly onto the stone sub-base.
- Appearance: It is only available in black.
EPDM Granules (This Product): This is the top layer or "wearing course" of a wetpour system.
- Origin: It is a premium, virgin synthetic rubber, not recycled.
- Function: Its job is to provide durability, UV resistance, and vibrant colour. It is installed in a thin layer (typically 15mm) on top of the SBR base.
- Appearance: It is available in a huge range of bright, through-coloured options.
EPDM Granules Specifications
Property | Value |
---|---|
Material Type | Ethylene Propylene Diene Monomer (Virgin Rubber) |
Application | Wearing course (top layer) of wetpour safety surfacing |
Granule Size | Standard 1.0mm - 4.0mm |
Bulk Density | Approx. 1,100 kg/m³ |
Hardness | Approx. 60 Shore A |
Colouring | Through-Coloured (Pigment is integral to the granule) |
Purity | >99% EPDM Polymer |
Required Binder | Must be mixed with Aliphatic Binder for bright colours |
Packaging | Sold in 25kg weather-resistant bags |
Our EPDM Granules are a component part of a full wetpour installation. They must be mixed with a polyurethane binder to create the final surface. Here is a guide to their proper use.
Required System Components
Materials:
- EPDM Granules (This Product)
- Aliphatic Binder (for colour stability)
- A prepared SBR rubber base layer or suitable sub-base
Key Tools:
- Forced-Action Mixer
- Steel Float Trowel & Screed Bars
- Wheelbarrow & Buckets
Step 1: Prepare the Base
EPDM granules are installed as the top layer (typically 15mm thick) over a prepared base course of SBR rubber. Ensure the SBR base is clean, dry, and free of all loose material before beginning.
Step 2: Use the Correct Mixing Ratio
The strength and longevity of the surface depend on the correct mix. The standard ratio is 1 part binder to 4 parts EPDM granules by weight (a 20% binder ratio).
- For every 25kg bag of EPDM Granules, you will need 6.25kg of our Aliphatic Binder.
Step 3: The Mixing Process
A forced-action mixer is essential for ensuring every granule is evenly coated.
- Add the full 25kg bag of EPDM granules to the mixer.
- Start the mixer, and then immediately pour the 6.25kg of Aliphatic Binder over the tumbling granules.
- Mix for 2-4 minutes until every granule is coated in a uniform, glossy film. For multi-colour mixes, blend the dry granules first before adding the binder.
Step 4: Trowelling the Surface
Once mixed, the material must be applied immediately over the SBR base layer.
- Transport the mix to the installation area and pour it onto the base.
- Spread the material evenly using a rake or trowel to the desired thickness (typically 15mm), using screed bars to ensure a consistent depth.
- Using a steel float trowel, apply firm downward pressure to compact and smooth the surface. Regularly wipe the trowel with a release agent (white spirit) to achieve a seamless, flat finish.