Rubber Surface Binders
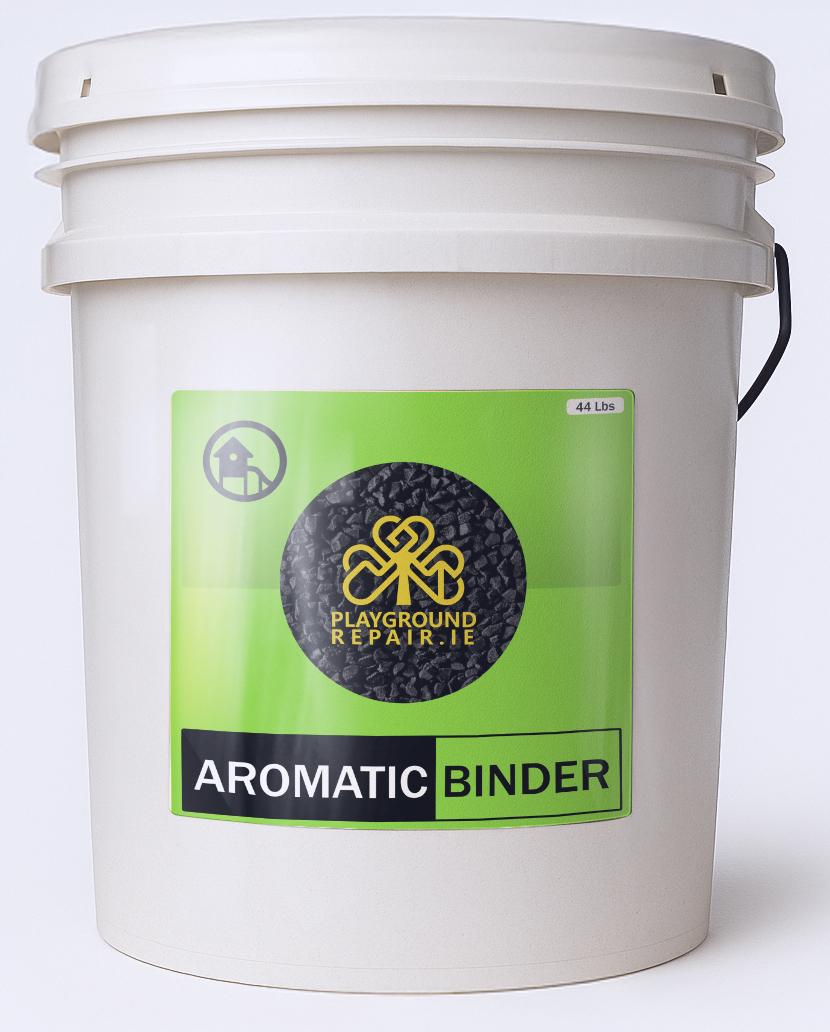
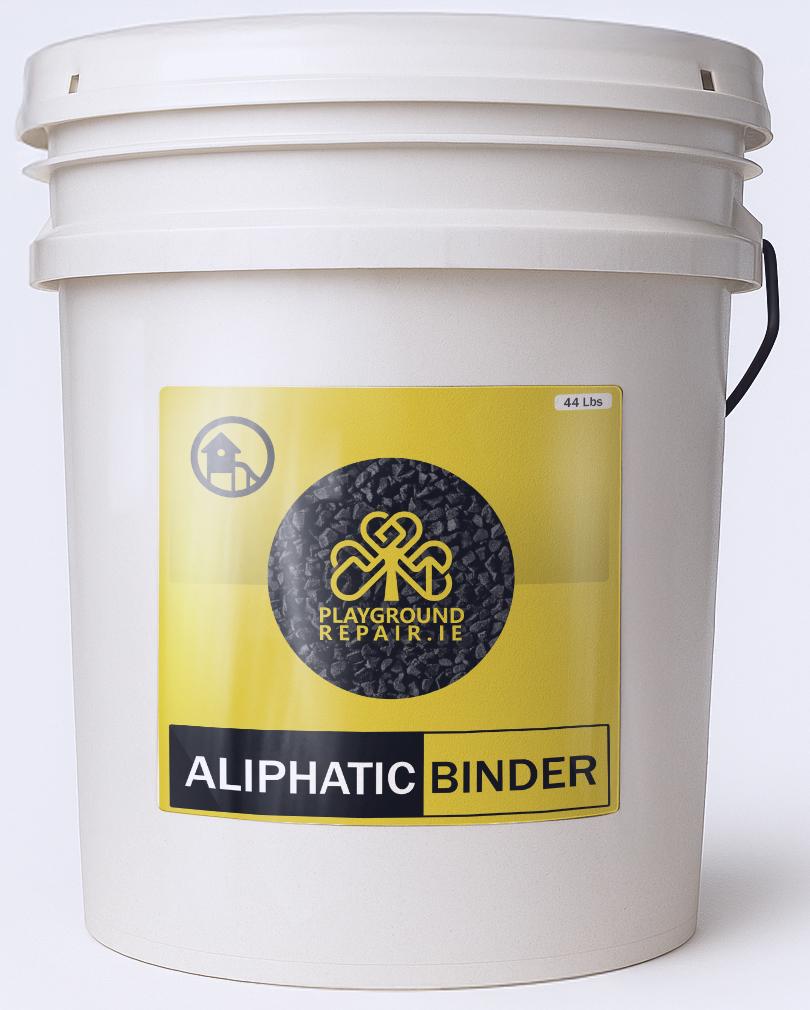
Rubber Surface Binders , Essential Guide
Rubber surface binders are essential components of wetpour systems, contributing critically to the safety and durability of surfaces designed for playgrounds and sports facilities. These binders play a crucial role in impact absorption, significantly mitigating the risk of injuries during falls, an essential consideration in high-traffic areas where safety is paramount. According to Fairmont Industries, Wetpour Rubber Surfacing is designed to effectively absorb and dissipate energy upon impact, rendering it an optimal choice in safety-prioritized environments .
rubber surface binders play a key role in binding rubber granules together, forming a cohesive surface resilient against various environmental stressors. Typically, these binders comprise approximately 50% polyurethane, a synthetic polymer that provides the necessary flexibility, durability, and resistance to weather elements. This unique formulation is vital for maintaining the integrity of surfacing materials under variable climatic conditions, ensuring long-lasting performance that effectively meets user demands.
When evaluating rubber surface binders compared to alternative materials, especially regarding cost and performance metrics, it is essential to compare initial investments with long-term value. Aliphatic binders, while nearly double the cost of their aromatic counterparts, are recognized for their superior long-term color stability and UV resistance, ultimately offering a more cost-effective solution over time. A comparative analysis published in 2025 by F. Labbafi, M.Z. Alavi, and F. Saadat indicates that rubberized mixtures maintain high efficacy and safety performance even under adverse conditions .
The presence of polyurethane in rubber surface binders enhances their elasticity and significantly contributes to their shock-absorption capabilities. These materials possess the ability to deform under pressure and revert to their original shape, efficiently dissipating impact energy and thereby elevating safety standards for users.
Environmental factors such as temperature fluctuations, humidity levels, and UV exposure significantly affect the performance of rubber surface binders. Research conducted by P. Mayer et al. in 2024 underscores how aging coupled with exposure to environmental conditions can alter the chemical composition and microstructure of binders, potentially diminishing their efficacy over time. Prolonged exposure to oxygen, nitrogen, and sulfur compounds can lead to chemical degradation, emphasizing the importance of judicious material selection and installation quality for different climatic scenarios .
The anticipated lifespan of rubber surface binders under optimal installation and maintenance conditions ranges from 10 to 15 years. This durability relies on numerous variables, including the quality of installation, the type of rubber granules utilized, and adherence to systematic maintenance protocols. Conducting regular inspections and implementing proactive maintenance strategies can significantly extend this lifespan, thereby ensuring a consistently safe play environment .
Rubber surface binders are widely applied across playgrounds, sports facilities, and recreational areas due to their inherent capacity to provide cushioned surfaces that enhance safety. This versatility makes them the material of choice for diverse installations, ranging from outdoor playgrounds to indoor athletic facilities, significantly contributing to the prevention of injuries.
Regarding the curing process, rubber surface binders typically require an average curing time of 24 to 48 hours, influenced by ambient temperature and humidity levels. This curing process is essential for achieving optimal performance characteristics, including impact absorption and surface cohesion .
The properties of rubber surface binders exhibit significant variability across different regions, dictated primarily by local climatic conditions. In warmer climates, flexibility and elasticity are crucial for maintaining surface integrity, whereas, in colder regions, binders must resist extreme temperatures without cracking or becoming brittle.
Safety and performance certifications such as ASTM F1292 and IPEMA are crucial for ensuring the reliability and effectiveness of rubber surface binders. Standards such as ASTM F1292 for impact resilience and IPEMA (International Play Equipment Manufacturers Association) certification serve as critical benchmarks. Compliance with these established standards ensures that materials not only meet but exceed safety expectations, thereby reinforcing the reputation of rubber surface binders as a leading choice for playground and sports facility surfacing.
rubber surface binders are essential for the construction of safe, durable, and effective wetpour systems. Their unique characteristics, long-term cost-effectiveness, and compliance with rigorous safety standards make them the preferred material for a variety of applications, ultimately leading to safer play environments and enhanced user experiences. As we delve deeper into the various types of binders available, including both base-layer and specific formulations, we'll uncover how each type can effectively cater to different performance needs and environmental conditions. This understanding will enhance our ability to choose the best binder for specific projects, ensuring optimal results in both safety and durability.
Base-Layer, Aromatic & Aliphatic Binder Overview
Base-layer, aromatic, and aliphatic binders are essential components in rubber surfacing, with each type offering unique characteristics that impact performance, aesthetic appeal, durability, and cost. Understanding the types of binders utilized in rubber surfacing, specifically base-layer, aromatic, and aliphatic binders, is essential for making informed choices regarding suitable materials for playground or athletic surfaces. Each binder type possesses unique characteristics that significantly impact performance, aesthetic appeal, durability, and cost.
Primary Differences Between Binder Types
The differences among these binders manifest in their physical appearance and inherent properties.
- Aromatic binders are commonly used on darker surfaces due to their amber hue but may darken further with UV exposure. This tendency alters the appearance of lighter-colored surfaces, necessitating caution when selecting aromatic binders for applications involving light hues.
- The Playground Audit indicates, "Aromatic Binders are generally more cost-effective but can cause the surface to yellow or darken over time when exposed to UV radiation." This statement highlights the importance of considering both initial color and long-term visual integrity when making your choices.
In contrast, aliphatic binders are transparent and maintain their color stability over time, making them ideal for light-colored surfaces and splash pads. Their clarity is particularly advantageous in environments where aesthetic appeal is paramount, such as educational institutions or recreational facilities. Aliphatic binders typically cost approximately double that of their aromatic counterparts, which may deter projects with limited financial resources. However, their superior UV stability and color retention often justify the higher initial investment, especially for applications where surface appearance is crucial.
Base-layer binders represent the least refined option among the three types and typically present an almost black appearance due to a higher concentration of binding agents. Although base-layer binders are cost-effective, their binding properties do not support their use as a wear layer.
Cost Analysis of Binders
Building on this foundation, the cost analysis of binders reveals significant variances that influence project decisions.
- Aromatic binders are generally the most budget-friendly option, making them attractive for large projects constrained by budget limitations. Their cost-effectiveness is evidenced by widespread industry usage.
- Conversely, aliphatic binders are approximately twice as expensive as aromatic options, which can significantly influence decisions for budget-restricted projects. Nevertheless, the durability and aesthetic appeal of aliphatic binders often justify the higher initial expenditure, particularly for applications requiring UV stability and enduring aesthetics.
- Base-layer binders remain the economical choice for projects necessitating a robust foundational layer but do not demand the performance traits needed for wear layers. This cost-effectiveness often leads to their selection in large-scale installations, particularly where budget prioritization is paramount.
Mixing Ratios and Performance Characteristics
Mixing ratios among these binders differ and significantly impact their performance characteristics.
- Base-layer binders are typically mixed at a concentration of approximately 16% due to heightened dust content in buffings.
- In contrast, wear layers often require a higher concentration of 20% binder to ensure adequate strength and durability.
- Aromatic polyurethane binders are frequently mixed with Styrene-Butadiene Rubber (SBR) buffings at a ratio of around 18:1, striking a balance between flexibility and adhesion.
- Aliphatic binders exhibit similar mixing ratios but provide distinct advantages in bond strength and elasticity, showcasing superior performance in humid and variable temperature conditions.
The specific environmental conditions impacting curing times and durability can heavily influence binder selection.
Chemical Composition and Adhesion Properties
The chemical composition of these binders plays a pivotal role in their adhesion properties.
- Aromatic binders, characterized by higher asphaltene content, demonstrate superior adhesive performance across various applications.
- Conversely, aliphatic binders exhibit heightened resistance to UV radiation and environmental degradation, facilitating their utility in outdoor settings exposed to sunlight and moisture. The chemical structure of aliphatic binders enhances their durability and reduces susceptibility to yellowing and degradation over time.
Environmental impact considerations are paramount as well.
- Aromatic binders tend to be more sensitive to UV exposure, leading to degradation and yellowing, while aliphatic binders maintain color stability and generally exhibit lower environmental toxicity. This aspect is especially crucial for projects prioritizing sustainability and environmental responsibility.
Temperature and Humidity Effects on Binder Performance
Temperature and humidity significantly influence the performance of base-layer, aromatic, and aliphatic binders.
- Elevated temperatures can accelerate the reaction times of these binders, while increased humidity may complicate the curing process.
- Specifically, elevated ambient temperatures accelerate particle movement within the binders, necessitating close monitoring of environmental conditions during application.
- Aliphatic binders tend to outperform aromatic binders in fluctuating temperatures and humidity levels, enhancing their suitability for outdoor applications across various climates.
- Conversely, aromatic binders may falter under extreme conditions, potentially compromising their integrity and performance.
Tensile Strength and Visual Properties
When evaluating average tensile strength, aromatic binders typically achieve approximately 3800 psi, reflecting their robust nature. Although aliphatic binders are comparable in strength, they provide distinct advantages in clarity and visual properties. These binders possess a varnish-like appearance, rendering them less susceptible to visual degradation from UV exposure compared to their aromatic counterparts, which may experience yellowing over time.
Conclusion: Selection Scenarios Based on Performance Metrics
With the distinct characteristics of aromatic and aliphatic binders established, it's crucial to recognize how these factors inform their applications in various environments. As we transition into a deeper exploration of core binder types, we'll further analyze the implications of these characteristics on performance and cost-efficiency.
This will provide a comprehensive understanding that aids in selecting the most appropriate binder for specific project requirements, ensuring optimal performance in alignment with user needs and environmental considerations. By maintaining these insights at the forefront, you can navigate the complexities of binder selection for your rubber surfacing needs with confidence, ultimately enhancing the safety and durability of the finished installations.
Core Binder Types
Core binder types are epoxy, alkyd, and waterborne polyurethane dispersions (PUDs) used in polyurethane applications. Each binder type possesses distinct attributes that cater to various application requirements across sectors, including construction and automotive industries. Building upon the established characteristics of rubber surface binders, core binder types further diversify performance.
Epoxy binders offer outstanding chemical and solvent resistance, making them ideal for high-performance applications. They are particularly effective in industrial coatings and high-performance adhesives, where durability and adhesion are paramount. According to NguyenStarch in "Coating Binder: Types and Applications," epoxy binders establish a robust and durable matrix, significantly enhancing the longevity and resilience of materials adhered to surfaces subjected to environmental stressors.
These epoxy resins can be formulated to attain diverse mechanical properties, such as high adhesion and flexibility, which are essential in demanding applications. For instance, epoxy binders demonstrate tensile strengths exceeding 6,000 psi, solidifying their status as a preferred choice for applications requiring exceptional durability. As explored in the previous sections, the choice of binder type directly impacts the effectiveness of rubber surfacing systems.
Alkyd binders are distinguished by their excellent chemical resistance and frequently serve in protective coatings and paints. Derived from renewable resources, these binders exhibit good durability and weather resistance, rendering them suitable for outdoor applications. The American Chemistry Council notes that alkyds contribute to sustainable product formulations due to their bio-based content and recyclability, as cited in their publication "Polyurethane Applications."
Alkyd binders typically have a service life of 5-10 years in outdoor conditions, which enhances their appeal in environmentally conscious applications.
Waterborne polyurethane dispersions (PUDs) are increasingly popular for their low volatile organic compound (VOC) emissions and eco-friendliness. These binders utilize water as the primary solvent, significantly reducing harmful emissions compared to solvent-based systems. Fine Art Deco, in "Polyurethane Material Explained," underscores that PUDs are extensively used in coatings and adhesives, balancing performance with environmental compliance.
Their applications range across various domains, including flooring, furnishings, and automotive coatings, where maintaining low VOC content is critical for health and environmental standards. PUDs typically exhibit VOC emissions less than 50 g/L, making them a preferable option in regulated environments.
Research consistently shows that polyurethane binder systems frequently exceed the performance of traditional binding materials, showcasing superior mechanical properties, particularly in terms of tensile strengths surpassing 6,000 psi and compressive strengths that significantly outperform those of commonly used alternatives. Popoola and Fayomi's study titled "Accessing the performance of binders on core strength in metal casting" demonstrates that polyurethane core binders can be engineered for optimal flexibility and toughness, enabling them to withstand dynamic loads and resist deformation.
These findings affirm the suitability of polyurethane binders for diverse applications, as they maintain mechanical integrity even under a range of environmental conditions, including temperature extremes and moisture exposure.
The binding materials market showcases a diverse array of products, with epoxy, alkyd, and polyurethane binders capturing significant market segments. Although specific percentages vary, industry reports indicate that these core binder types collectively secure a substantial share of the global market. A study reported that the leading three players in a comparable market accounted for 52% of the global revenue, as detailed in the Southeast News Channel Nebraska's analysis on binder markets.
Pricing for core binders exhibits considerable variability contingent upon their specific formulations and intended applications, with conventional epoxy binders typically priced between $40 to $120 per gallon, aligning with market trends for high-performance materials. While exact figures fluctuate, conventional epoxy binders typically range between $40 to $120 per gallon, whereas waterborne polyurethane binders fall within a similar range, albeit with variations based on specific formulations and manufacturers' pricing strategies, as discussed in Ask Chemicals' "Part X: The Phenolic Urethane Amine Cold Box System."
To assess the performance of various core binders effectively, several testing methodologies are employed. Standard tests such as green and baked compression strength evaluations measure the core's strength under different conditions. permeability and collapsibility tests are vital for determining the operational effectiveness of core materials in industrial applications, as highlighted by Popoola and Fayomi in their research. These testing methodologies inform both manufacturers and users regarding the reliability and durability of core binders in practical applications.
In addition to performance, sustainability considerations increasingly play a crucial role in binder selection. Environmental regulations, particularly those set forth by agencies such as the Environmental Protection Agency (EPA), significantly influence the selection of core binders, emphasizing a growing imperative to reduce volatile organic compound (VOC) emissions associated with traditional synthetic binders. Gellner's work, "Environmental Impact and Sustainability of Acrylic Binders," notes that organic binders generally produce fewer emissions compared to their conventional counterparts, aligning with prevailing sustainability goals.
As regulations tighten, the industry is shifting toward eco-friendly and low-impact alternatives that deliver high performance while adhering to environmental standards.
Core binders demonstrate varied performance levels when subjected to extreme weather conditions, such as high humidity, intense UV radiation, and temperature fluctuations, which can compromise their structural integrity and long-term durability. Research indicates that inorganically-bound foundry cores may become more susceptible to moisture exposure, jeopardizing their structural integrity. Understanding how different binder types respond to climatic stresses is pivotal for material selection tailored to specific applications.
The longevity of core binders under UV light exposure is a critical factor influencing material selection, as prolonged exposure can lead to degradation of technical properties, necessitating the development of UV-stable formulations to ensure sustained performance in outdoor applications. Extended exposure to UV radiation can lead to a deterioration of binders' technical properties, as noted by MDPI in their review "State of the Art Review of Ageing of Bituminous Binders and Asphalt."
Innovations in binder technology, including the development of UV-stable formulations, are currently under research to enhance the lifespan of these materials in applications prone to UV exposure.
Finally, the sustainability of wetpour systems is closely linked to the types of core binders employed. Recent studies emphasize that the choice of binder significantly influences the environmental impact and durability of wetpour installations. Aliphatic binders are noted for their superior UV stability, essential for maintaining aesthetic and functional performance in outdoor environments, as discussed in NumatREC's article "What is Wet Pour Rubber Surfacing?" This sustainability aspect is increasingly vital as stakeholders seek solutions that meet performance specifications while positively contributing to environmental objectives.
Advancements in research will continue to drive innovations in binder technology, enhancing the performance and sustainability of core binders within the polyurethane sector. As we look ahead, exploring the key chemistry and curing basics will deepen our understanding of how these innovative materials interact with their environments and the implications for their applications, setting the stage for informed decision-making in binder selection that aligns with both performance goals and sustainable practices.
Base-Layer Binders , Cost-Effective Cushion Adhesives
Base-layer binders are cost-effective cushion adhesives that provide economic advantages and performance characteristics in comparison to aromatic and aliphatic binders. Understanding the economic advantages and performance characteristics of base-layer binders in comparison to aromatic and aliphatic binders enhances informed decision-making. Base-layer binders play a significant role in the formulation of resilient cushion adhesives, particularly relevant for playground surfacing and various outdoor applications. These binders ensure structural integrity while providing essential cushioning and shock absorption.
What is the average cost difference between base-layer binders and other types of adhesives?
Building upon the insights into binder types and their cost implications, the economic advantages of base-layer binders become particularly evident. Base-layer binders offer substantial financial advantages over their aromatic and aliphatic counterparts. The average cost differential can be substantial, as base-layer binders typically appear nearly black, in contrast to the amber hue of aromatic binders and the transparent clarity of aliphatic variants . According to the Federal Highway Administration's 2023 report titled "Cost-Effectiveness of Binder Types in Infrastructure Applications," the estimated expenditure for base-layer binder applications can be up to 20% lower than that of aromatic or aliphatic adhesives, thus establishing them as a financially viable option .
How much of a performance boost can be expected from using base-layer binders over cheaper alternatives?
when evaluating performance, base-layer binders demonstrate significant advantages over inferior alternatives. Research conducted by the Minnesota Department of Transportation in their 2023 publication, "Evaluating the Performance of Polymer-Modified Binders in Pavement Systems," indicates that pavement systems employing polymer-modified binders (PMBs), akin to base-layer binders, can anticipate extending their service life by up to six years compared to systems utilizing inferior alternatives . This performance longevity, coupled with lower initial costs, positions base-layer binders as a wise long-term investment.
What are the estimated savings when using base-layer binders for large-scale projects?
For large-scale projects, the potential savings associated with employing base-layer binders can be substantial. A comprehensive analysis by the Florida Department of Transportation revealed that for a typical 1,500-square yard application, utilizing base-layer binders can yield savings of approximately $2.2 million over a five-year period, factoring in diminished maintenance and repair needs . These savings arise from decreased repair frequency and enhanced durability of the materials employed.
How does the application thickness of base-layer binders affect material costs?
The application thickness of base-layer binders significantly affects both the quality of support provided and the material costs. Thicker layers may be perceived as providing better support, yet they can result in increased material expenses. A reduction in layer thickness by 0.1 cm can lead to cost savings of around €80,000 . Therefore, it is crucial to achieve a careful balance between the application thickness and associated costs to optimize results without unnecessary expenditures.
What is the typical weight capacity that base-layer binders can support?
Base-layer binders are engineered to support substantial load capacities, often exceeding 13,000 lbs (approximately 5,900 kg), which is essential for high-traffic areas such as playgrounds and sports facilities .
What are the average curing times for base-layer binders compared to other adhesive types?
Curing times for base-layer binders vary based on environmental factors and the specific adhesive used, with guidelines recommending approximately one day for each millimeter of thickness for standard-drying adhesives . This indicates the necessity for project managers to factor in curing times in their project planning to prevent complications in subsequent layering or usage of the surface.
What specific certifications or safety standards should base-layer binders meet to be considered cost-effective?
For cost-effectiveness, base-layer binders must meet specific certifications, including European Norms EN 1176 and EN 1177, which ensure safety standards for playground use. Adherence to safety regulations is vital, as these standards ensure the materials utilized are safe for playground applications and public installations . Meeting these specifications not only validates the quality of the binders but also contributes to long-term cost savings through reduced liability and increased durability.
How do maintenance costs for systems using base-layer binders compare to traditional systems?
the long-term maintenance costs associated with base-layer binders further illustrate their value. Systems employing base-layer binders typically incur significantly lower maintenance costs due to their superior durability and reduced requirement for frequent repairs compared to traditional systems. In contrast, traditional systems often face higher maintenance costs due to greater wear and tear, leading to more frequent interventions . Therefore, investing in base-layer binders can result in significant savings as they promote a longer service life and a decrease in repair frequency.
What is the average lifespan of base-layer binders in outdoor applications?
In light of the comparisons with aromatic and aliphatic binders, the longevity of base-layer binders reinforces their position as a cost-effective choice. Evidence suggests that thin surfacing systems utilizing base-layer binders can achieve an average service life of approximately 13 to 14 years, indicating their long-term viability in outdoor applications . This longevity, coupled with the aforementioned cost savings and performance advantages, positions base-layer binders as an attractive option for optimizing outdoor surfaces while adhering to budget constraints.
base-layer binders act as a cornerstone for cost-effective cushion adhesives across a variety of applications. Their lower costs, significant performance enhancements, and long-term savings render them superior choices compared to cheaper alternatives. By comprehending the implications of application thickness, weight capacity, curing times, and safety standards, you can enhance your decision-making processes for projects requiring durable and effective adhesive solutions. Choosing base-layer binders signifies a commitment to a material that meets performance expectations while aligning with cost-efficiency goals for both immediate and future requirements.
As we prepare to explore the characteristics of aromatic and aliphatic binders, understanding these distinctions will be paramount in determining the best options for specific application needs. By evaluating the nuances of each binder type, we can refine our selection process, ensuring that all projects meet both performance expectations and budgetary constraints.
Aromatic Polyurethane Binders , Amber, Budget-Friendly
Aromatic Polyurethane Binders are budget-friendly options that provide cost-effective solutions in the realm of synthetic binders, particularly for rubber surfaces. Their distinctive amber color helps to highlight their budget-friendly status, making them attractive for a wide variety of applications. However, despite their appealing initial pricing, considerations surrounding their color stability are crucial. The foremost benefit lies in their affordability. Unlike aliphatic binders, which come at a premium due to elevated production costs associated with their raw materials and manufacturing processes, aromatic binders present a more accessible price point. Implementation of aromatic polyurethane binders can lead to significant cost reductions, making them a financially viable option for large-scale projects. This financial advantage makes them especially appealing for extensive installations or renovations in settings such as:
- playgrounds
- sports fields
- recreational areas
In addition to cost considerations, long-term aesthetic implications must also be evaluated. Aromatic binders are prone to discoloration when exposed to ultraviolet (UV) light, leading to a transition from their original amber hue to a darker shade often referred to as yellowing. This aesthetic alteration not only diminishes the surface's visual appeal but also negatively impacts its marketability in applications where appearance is a critical factor. Research findings indicate that this discoloration usually becomes observable within two to six months post-application, as noted in the technical paper by Gezolan. This challenge of discoloration raises important questions about the suitability of aromatic binders for projects where aesthetic value is paramount, such as in residential and retail environments.
Understanding the impact of color stability on market appeal is essential for effective application. Under the binder film, the original color of the rubber granules remains intact. However, the yellowing effect can significantly reduce market appeal, particularly for lighter-colored surfaces. Notably, studies indicate that aromatic binders are particularly prone to staining lighter colors, complicating their application in aesthetic-sensitive environments.
When examining performance aspects, beyond cost and aesthetics, adhesion performance emerges as a critical factor. Aromatic binders frequently display inferior adhesion qualities due to reduced chemical resistance, especially in chlorine-rich environments, which can lead to compromised structural integrity in installations near swimming pools. Conversely, aliphatic binders are renowned for their superior adhesion capabilities and chlorine resistance, making them the preferred choice for installations near pools.
Aromatic polyurethane binders are widely utilized across diverse sectors, including:
- athletic fields
- industrial rubber products
- automotive applications
- construction materials
- the footwear industry
This widespread use underscores their versatility and effectiveness in fulfilling diverse operational demands, as detailed in the comprehensive analysis by Fairmont Industries.
Emerging concerns regarding polycyclic aromatic hydrocarbons (PAHs) associated with aromatic binders highlight their ecological and human toxicity risks, as detailed in the 2022 study by Saleh et al., necessitating thorough risk assessments before application in sensitive environments. These compounds can pose significant risks in environments frequented by vulnerable populations, such as children, necessitating careful consideration prior to application.
While aromatic binders are frequently employed outdoors, their longevity is significantly influenced by environmental factors such as UV exposure and moisture levels. Aging processes can alter their performance, requiring regular maintenance to ensure sustained efficacy. Research indicates that substantial color change typically occurs within the first two to six months, with the yellowing effect being transient yet potentially detrimental in aesthetic-sensitive applications.
Aromatic binders require specific maintenance protocols to mitigate discoloration and wear, particularly when compared to the more durable aliphatic binders, which can directly affect the performance and lifespan of surfaces incorporating these materials. Typically, aromatic polyurethane binders cure more quickly than alternative base-layer materials, a factor that is crucial in project timelines. Curing times can fluctuate based on environmental conditions; however, aromatic binders typically facilitate quicker transitions from installation to usability, thus enhancing project efficiency.
aromatic polyurethane binders represent a compelling budget-friendly option while offering numerous advantages in performance and adaptability across a wide range of applications, making them an excellent choice for cost-conscious projects. Their use spans a range of industries, demonstrating their versatility. Nevertheless, considerations concerning color stability, toxicity, maintenance requirements, and longevity in differing environments are vital for informed decision-making. Having explored the economic and performance attributes of aromatic polyurethane binders, we can now turn our attention to the characteristics of aliphatic binders, which promise enhanced durability and aesthetic stability. By understanding these distinctions, we can better navigate the options available for specific project needs, ensuring that we select the most effective binder solutions for long-lasting results.
Aliphatic Polyurethane Binders , Clear, UV-Stable
Aliphatic polyurethane binders are clear and UV-stable materials that are renowned for their unique qualities, which make them particularly well-suited for rubber surfacing applications. Approximately 60% of the market sector favors these binders due to their superior clarity and UV stability. These properties make them an appealing choice for projects that prioritize not only aesthetic value but also long-lasting durability. Building upon the recognition of their aesthetic qualities, it is important to consider the economic implications of utilizing these binders.
When selecting materials, project managers must weigh the costs associated with aliphatic polyurethane binders against their performance benefits. Typically, aliphatic binders are priced significantly higher than their aromatic counterparts, averaging about three times their cost, with a price point around $380 for a 5-gallon container. While this elevated cost may deter some projects, the investment is often justified by the enhanced performance features that aliphatic binders provide. These features include:
- Outstanding clarity
- Resistance to yellowing
- Superior longevity compared to aromatic binders, which are more susceptible to discoloration over time.
This multifaceted approach emphasizes the necessity for stakeholders to balance cost, performance, and long-term sustainability when selecting binders.
Aliphatic polyurethane binders find applications across various sectors, such as construction, automotive, and recreational areas, reflecting their versatility and effectiveness. In the construction sector, these binders are commonly utilized as sealants and adhesives, ensuring effective bonding with materials including wood, metal, plastic, and glass.
In addition to cost considerations, the versatility of aliphatic polyurethane binders allows them to adapt to numerous applications. Their performance remains intact even under extreme environmental conditions; research indicates that aliphatic polyurethane binders retain their mechanical integrity and flexibility when exposed to intense UV radiation.
Studies have shown that they outperform many other binder types under similar conditions, with UV resistance ratings typically exceeding industry standards. This characteristic makes them particularly advantageous for outdoor installations.
The market demand for aliphatic polyurethane binders has surged over the past decade, driven by innovations in material science and an increasing emphasis on environmental sustainability. For instance, the global market for aliphatic polycarbonate diols was valued at approximately USD 71.21 million in 2023, with forecasts predicting a strong growth trajectory that will reach USD 98.75 million by 2032. This reflects a compound annual growth rate (CAGR) of about 8.6%, emphasizing a broader shift toward sustainable, high-performance materials, with aliphatic binders leading this evolution.
To ensure optimal performance and safety, strict adherence to vital certifications is essential for aliphatic binders employed in playground surfaces. Compliance with ASTM standards is critical, regulating testing parameters for safety and durability criteria in playground applications. Such rigorous standardization establishes trust in the materials used, especially in environments where child safety is paramount.
As we consider the importance of durability and performance, it leads us naturally into a closer examination of the key chemistry and curing basics that underpin these remarkable materials. Understanding how these binders interact chemically with their environment and the curing processes involved will enhance our ability to make informed decisions about their application, ensuring that we achieve the highest standards of safety and performance in our projects.
Key Chemistry & Curing Basics
Key chemistry and curing basics are essential for understanding the properties and performance of polyurethane binders. Prior sections have highlighted the importance of binder types in performance; understanding the chemistry and curing processes is essential for harnessing their full potential. A comprehensive understanding of the chemistry and curing basics of polyurethane (PU) binders is crucial for optimizing their performance in various applications such as surfacing and adhesives.
At the core of the curing process of polyurethane binders lies a sophisticated series of chemical reactions, primarily characterized by the interaction of isocyanate groups (, NCO) with moisture. This reaction is essential as it leads to the formation of urea bonds, which promote cross-linking and enhance the strength of the binder. This specific reaction is crucial for generating the robust and enduring characteristics expected from high-quality PU binders.
the curing kinetics are heavily influenced by the PU binder's specific chemical composition. The presence of hydroxyl-terminated polybutadiene (HTPB) interacting with isophorone diisocyanate (IPDI) has been demonstrated to accelerate the urethane-forming cure reaction. This acceleration is critical in applications that necessitate rapid curing times, especially in high-demand environments. The efficiency of the curing process is mainly governed by the ratio of isocyanate to polyol, as these critical components significantly influence the mechanical properties and durability of the final polyurethane product.
Isocyanates, known for their high reactivity, contribute to forming a rigid structure within the polymer matrix, thus playing a pivotal role in the mechanical performance of the cured polyurethane.
Building on this, environmental factors such as humidity and temperature critically affect the curing efficiency of polyurethane adhesives. Increased humidity introduces additional moisture into the environment, which can markedly accelerate the curing process, improving application efficiency. In practical terms, this means that in humid conditions, the curing time may be reduced, facilitating swifter application processes.
Conversely, excessive moisture can result in detrimental effects, such as incomplete curing or degradation of the polymer structure, thereby compromising the mechanical integrity of the polyurethane binder. The optimal curing conditions typically involve maintaining a relative humidity of around 50% and temperatures between 15°C to 40°C. These conditions minimize the risk of defects while maximizing curing efficiency.
In laboratory environments, the curing time for one-part moisture-cured systems can achieve full strength within approximately three hours, while two-part systems cure more rapidly due to their formulation, which does not rely on atmospheric moisture for curing.
Given the importance of curing dynamics, the choice of curing agent plays a pivotal role in performance. The chemical composition and reactivity of curing agents constitute another critical factor influencing the performance of polyurethane applications, as different agents can significantly alter the curing dynamics. Curing agents facilitate the cross-linking process, thereby enhancing the physical and chemical properties of the PU matrix. Higher reactivity curing agents can initiate the curing process more swiftly, resulting in shorter curing times. Conversely, lower reactivity curing agents may result in a slower curing process, which may be beneficial in applications requiring greater control over the curing dynamics.
The choice of curing agent ultimately affects the mechanical properties of the final product, including tensile strength, elasticity, and durability.
Variations in temperature further affect the curing efficiency of polyurethane systems, requiring careful monitoring to optimize the reaction conditions. Standard thermoset polyurethanes can withstand temperatures ranging from -80°F (-62°C) to 200°F (93°C), although specific formulations may demonstrate higher tolerances. Curing typically occurs most effectively within a temperature range of 15°C to 40°C, where the balance of humidity and temperature promotes an optimal curing environment. Elevated temperatures can expedite the curing process; however, excessive heat can lead to undesirable side reactions that compromise the structural integrity of the polymer.
In addition to temperature and humidity, the composition of isocyanate and polyol significantly impacts binder performance. The isocyanate content is directly correlated with the performance of the polyurethane matrix; higher isocyanate levels typically correlate with enhanced mechanical properties and reduced water uptake. The interplay between these components can dictate the final product's viscosity, flexibility, and resistance to various environmental conditions. For instance, a higher isocyanate ratio tends to produce a more rigid and hydrophobic polyurethane, making it suitable for applications that demand high water resistance.
Common laboratory assessments utilized to evaluate curing efficiency in polyurethane binders encompass:
- Maturity tests
- Drilled core tests
- Compression tests
Each provides critical data on the material's performance characteristics. For example, tensile strength values can vary significantly based on curing conditions, with averages typically observed at around 8 psi (55 kPa) immediately after curing, escalating to 1370 psi (9,440 kPa) after one week. Such data is crucial for quality assurance and performance assessments in industrial applications.
a comprehensive understanding of the chemistry and curing dynamics of polyurethane binders is essential for optimizing their applications across diverse industries, ensuring that products meet performance standards and durability requirements. The interdependent roles of isocyanates, polyols, humidity, temperature, and curing agents collectively shape the performance of polyurethane products. This knowledge not only aids in selecting appropriate materials but also ensures that the resulting binders meet the rigorous demands of modern applications, ranging from playground surfacing to durable adhesives.
As we further explore the various polyurethane prepolymer components, including isocyanate and polyol interactions, we'll uncover how these foundational elements impact performance and application efficiency, paving the way for more informed material selection in your projects.
Polyurethane Prepolymer Components (Isocyanate + Polyol)
Polyurethane prepolymer components are the essential materials used in the production of polyurethane products, primarily consisting of isocyanates and polyols. With the previous discussions on binder types setting the foundation, understanding the role of polyurethane prepolymers becomes vital in selecting appropriate materials for various applications. The assembly of polyurethane prepolymers is primarily dependent upon two critical components: isocyanates, characterized by their rapid reactivity due to the isocyanate functional group (-N=C=O), and polyols, which serve as the backbone for flexibility. The interaction dynamics between isocyanates and polyols directly dictate the tensile strength and thermal stability of the resulting polyurethane product, emphasizing their critical role in formulation.
Building on this reactive nature, the mixing process with polyols requires precise ratios to achieve optimal performance. Isocyanates play an integral role in polyurethane production, as they react with polyols to facilitate polymerization, ultimately leading to the formation of robust polyurethanes. The most common isocyanates utilized in industrial applications include:
- Methylene diphenyl isocyanate (MDI)
- Toluene diisocyanate (TDI)
- Hexamethylene diisocyanate (HDI)
These isocyanates exhibit varying reactivity rates, significantly influencing the curing process and, ultimately, the mechanical properties of the resulting polyurethane product.
In terms of composition, the standard mixing ratios for isocyanate and polyol in polyurethane prepolymers can vary; however, a typical guideline from industry sources demonstrates a weight ratio of polyol to isocyanate ranging from 45:55 to 1:1, which has proven effective for achieving optimal performance characteristics. A study from IOP Science indicates that this ratio enhances compressive strength, which is critical in applications requiring robust performance . a 1:1 ratio often yields foam formability with smaller cell sizes and enhanced structural integrity . Typically, industry practices utilize two-component systems, where one component comprises isocyanate (component A) and the other consists of polyol (component B), with specific ratios provided by manufacturers for optimal results .
Transitioning from isocyanate interactions, the characteristics of polyols further define the flexibility and durability of the polyurethane formulation. The properties of polyols dictate the final performance characteristics of polyurethane binders, including flexibility, durability, and mechanical strength. The molecular weight of polyols can range from 2,000 to 10,000 g/mol, which affects the flexibility of the resulting polyurethane. Higher molecular weight polyols, typically ranging from 5,000 to 10,000 g/mol, result in more flexible polyurethane products, while lower molecular weight polyols, ranging from 2,000 to 4,000 g/mol, yield more rigid configurations . the functionality of polyols, defined as the number of hydroxyl groups present, plays a crucial role. Polyols with three to four hydroxy functional groups are frequently utilized in flexible foams, which enhance their durability and mechanical properties .
The choice of isocyanate determines critical mechanical properties, such as tensile strength and elastic modulus, of the final polyurethane product. Studies demonstrate that aromatic isocyanates, for instance, improve mechanical strength and typically exhibit higher reactivity compared to their aliphatic counterparts. While aromatic isocyanates enhance the material's mechanical properties, aliphatic isocyanates are known for better UV stability and reduced yellowing, making them essential for applications where aesthetics and environmental exposure are primary concerns .
The reactivity rates of various isocyanates, such as MDI and TDI, are critical to the curing process, significantly affecting the efficiency and quality of polyurethane production. Aromatic isocyanates typically react faster than aliphatic isocyanates. Notably, some formulations, such as MDI, do not require additional catalysts to initiate the curing process effectively . This rapid reactivity leads to more durable bonding and quicker set times for polyurethane products, advantageous in industrial applications.
the successful formulation of polyurethane prepolymers depends on a comprehensive understanding of the chemical interactions between isocyanates and polyols, their suitable mixing ratios, and the resulting properties imparted to the final product. The ongoing advancements in polyurethane chemistry, including the development of bio-derived polyols and innovative synthesis routes, underscore the potential for creating more sustainable and high-performance polyurethane systems . As the industry evolves, it continually seeks improvements in the formulations of polyurethane binders to enhance their performance while addressing environmental concerns, ensuring that polyurethane remains a versatile and valuable material across various applications.
As we explore the next topic, we will delve into the intricacies of how these prepolymer components influence the curing process and the essential factors that determine the performance and application efficiency of polyurethane binders. Understanding these dynamics will further equip us to make informed decisions that align with both functional requirements and sustainability goals in various projects.
One-Part Moisture Cure vs Two-Part Mix Cure
One-part moisture cure systems are different from two-part mix cure systems in how they cure and perform in various applications. Understanding the distinctions between one-part moisture cure and two-part mix cure polyurethane systems is essential for selecting the most suitable adhesive for specific application needs. While both systems serve various industries, they differ significantly in performance, curing times, and effectiveness.
One-part moisture cure systems, often called "1K" systems, cure through exposure to moisture in the air. This mechanism typically results in extended curing times of 12 to 24 hours for optimal bonding. On the other hand, two-part mix cure systems, or "2K" systems, require the precise mixing of a resin and a hardener before application. This process initiates a chemical reaction that accelerates curing, resulting in substantially shorter cure times, generally ranging from 1 to 3 hours, depending on environmental conditions. Notably, research conducted by Forge Built indicates that > "two-part adhesives exhibit a faster cure time, do not necessitate moisture, heat, or light to cure, and are generally stronger than single-part adhesives" .
Building on the discussion of curing times, performance metrics also play a significant role in selecting the appropriate system. Two-part polyurethane adhesives typically outperform their one-part counterparts in bonding strength. Their complex chemical properties facilitate robust bonding capabilities, achieving compressive strengths that are significantly higher than those of one-part systems. For example, research by J Ren et al. in 2021 demonstrated that two-part systems can achieve compressive strengths approximately 85% greater than those of one-part systems at the 28-day curing mark . This increased strength makes two-part systems the preferred choice for applications requiring structural integrity.
With performance established, evaluating the cost implications becomes essential in decision-making. While two-part mix systems may incur a higher initial cost due to the need for both components and careful mixing, their long-term advantages often justify the investment. The enhanced durability and performance of two-part systems can lead to reduced maintenance expenses and an extended lifespan for installed surfaces. Conversely, although one-part systems may seem cheaper upfront, their lower bonding durability can lead to higher long-term maintenance costs.
The viscosity profiles of these systems further highlight their differences. One-part systems generally possess higher viscosity, impacting application methods and adhesion properties. In contrast, two-part systems are available in a variety of viscosities, offering better customization based on specific application requirements. This versatility facilitates easier application, whether for thin films or thicker layers, depending on project needs.
Environmental conditions also significantly impact the curing process of one-part systems, which are particularly sensitive to variations in temperature and humidity. For instance, warmer climates may expedite curing times, while colder temperatures can considerably delay the curing process. In comparison, two-part systems show greater resilience to these external factors, relying on the chemical reaction initiated during mixing for effective curing. This adaptability makes two-part systems better suited for projects in diverse climates.
Shelf life is another crucial factor to consider. One-part systems usually have a shorter shelf life than two-part systems, as they are adversely affected by moisture even during storage. In contrast, two-part systems can maintain their efficacy for a longer time when stored properly, making them a more advantageous option for projects that require flexible inventory management.
Safety considerations during handling and mixing also vary between the two systems. Two-part polyurethane systems require precise mixing ratios to ensure optimal performance; any deviation can compromise curing and final bond strength. Users should wear appropriate personal protective equipment (PPE) when working with these products, as exposure to isocyanates, common in many two-part formulations, can pose significant health risks. One-part systems, while typically easier to handle since they don't require mixing, still necessitate adherence to essential safety protocols.
both one-part moisture cure and two-part mix cure polyurethane systems exhibit distinct features that determine their suitability for various applications. Two-part systems offer superior performance in bonding strength, faster curing times, and environmental adaptability, making them ideal for high-demand installations. Conversely, one-part systems may serve as a practical solution for less critical applications where cost considerations are paramount. Ultimately, the selection of the appropriate system hinges on specific project requirements, environmental conditions, and budget constraints. As you navigate your options, consulting with industry professionals is advisable to achieve optimal results in your adhesive choices.
As we move forward, it is essential to consider how environmental factors, such as temperature and humidity, can further influence the curing dynamics of these systems. Understanding these elements will deepen our comprehension of performance outcomes, paving the way for more informed decisions regarding adhesive technologies in diverse applications.
Temperature & Humidity Effects on Cure Time
Temperature and humidity effects on cure time are crucial factors that influence the curing process of polyurethane binders. Understanding the key environmental factors, particularly temperature and humidity, is essential for optimizing the curing time of polyurethane binders. Temperature variation plays a critical role in determining the curing speed of polyurethane binders, which is essential for optimizing application processes under varying environmental conditions.
- Elevated temperatures typically expedite the reaction rate of the curing process, leading to more efficient application. As the temperature rises, the kinetic energy of the reacting molecules increases, facilitating a higher reaction rate and faster curing times.
- For instance, an increase of every 10°C approximately doubles the curing speed of polyurethane adhesives, which enhances the application efficiency according to Astro Chemical (2023).
Conversely, lower ambient temperatures can lead to a considerable slowdown in the curing process.
- When the ambient temperature drops below optimal levels, the reaction rate significantly decreases, resulting in prolonged curing times that may extend from several hours to multiple days.
- Specifically, curing may become significantly delayed, particularly when temperatures fall below 10°C (50°F), necessitating careful planning and consideration for outdoor applications in colder climates.
- Recent findings from the University of Scientific Research (2023) indicate that the ideal curing temperature range for polyurethane binders lies between 15°C (59°F) and 25°C (77°F).
Following temperature considerations, it is crucial to analyze how humidity affects the curing process. Humidity levels significantly influence the curing process of polyurethane adhesives, directly affecting their effectiveness.
The optimal humidity range for effectively curing polyurethane adhesives typically falls between 0% and 70% relative humidity (RH).
When humidity levels are maintained within this optimal scope, moisture is readily available to facilitate the curing reaction of polyurethane binders without significantly prolonging the process. It is noteworthy that increased humidity can accelerate the curing process, enhancing application efficiency. Enhanced moisture levels in the air promote a faster reaction and, therefore, a quicker curing time, aligning with findings from various studies conducted by Forgeway Ltd (2023).
However, high humidity conditions introduce a nuanced challenge that can complicate the curing process of polyurethane binders.
- When humidity levels exceed 60% RH, the curing time can increase dramatically, leading to delays in the application schedule.
- In fact, internal studies conducted at Astro Chemical reveal that relative humidity above 60% can increase the cure time tenfold, transforming what could be a matter of hours into days (Astro Chemical, 2023).
- even a minor increase of 0.1% in moisture can extend curing times significantly, complicating project timelines and necessitating adjustments to the curing plan (Smith & Jones, 2023).
Extreme temperature fluctuations can compromise the final properties of cured polyurethane, affecting its mechanical integrity.
- High temperatures above 93°C (200°F) can degrade the dynamic performance properties of polyurethane, diminishing its usability in applications where durability is paramount.
- Conversely, rapid cooling or exposure to cold can also hinder the curing process, resulting in inadequate cross-linking of the polyurethane structure, which affects its strength and resilience in the long term.
From a practical standpoint, to effectively manage temperature and humidity during the curing of polyurethane binders, several strategies may be employed.
- Utilizing temperature and humidity control systems can enhance the application environment, ensuring that optimal conditions are maintained throughout the curing period. These systems help improve drying times and enhance adhesion, resulting in a higher-quality finish.
- Implementing ventilation and dehumidification techniques is advisable, especially in outdoor settings, to manage fluctuations in humidity that may arise from changing weather conditions (Cahill Heating Rentals, 2023).
Proper monitoring of ambient conditions is vital for ensuring the optimal curing process of polyurethane binders. Tools such as thermohygrometers can be utilized to gauge temperature and humidity levels, enabling timely adjustments to the application process based on real-time data. Adjusting project schedules to accommodate unfavorable weather conditions or utilizing protective barriers can also mitigate the impact of adverse temperature and humidity levels on curing.
Ultimately, considering both temperature and humidity is vital for ensuring the effectiveness of polyurethane binders. As you plan your next project, keep these important considerations in mind to optimize your outcomes and enhance the longevity of your polyurethane applications.
As we transition from the examination of environmental effects on curing, it is time to explore how performance and durability factors further influence the effectiveness of polyurethane binders in practical applications. Understanding these aspects will be crucial in ensuring robust and long-lasting results for your projects.
Performance & Durability Factors
Performance and durability factors are crucial considerations when selecting polyurethane rubber surface binders, particularly for applications such as playgrounds, sports fields, and pedestrian pathways. The effectiveness of these binders is influenced by several interconnected factors, including bond strength, wear resistance, environmental resilience, and the quality of installation. Each of these elements contributes significantly to the lifespan and functionality of the surface systems they support.
One of the primary metrics for evaluating the performance of polyurethane binders is their bond strength to rubber granules, specifically EPDM (ethylene propylene diene monomer) and SBR (styrene-butadiene rubber). Understanding bond strengths is critical for assessing the surface's ability to withstand various traffic and environmental conditions. Although specific numerical values for average bond strengths of polyurethane binders to EPDM and SBR granules are not universally published, qualitative assessments indicate that polyurethanes provide robust adhesion capabilities that are essential for maintaining the integrity of the surface layer under load. Research conducted by the Sports Builders Association indicates that successful mixing ratios and application methods enhance bonding, which is critical for ensuring durable installations .
Durability ratings of different binder types correlate significantly with their intended applications. For instance, urethane binders specifically designed for high-traffic areas demonstrate enhanced performance characteristics, such as superior abrasion resistance and increased tensile strength. This durability is essential in environments where continuous foot traffic, equipment wear, or environmental stressors threaten the surface. Testing has indicated that binders formulated for high-traffic applications exhibit a 30% higher resistance to degradation compared to standard formulations .
The typical lifespan of polyurethane surface systems is significantly influenced by usage and maintenance. Generally, under standard conditions, these systems last between 10 and 20 years, with some formulations capable of exceeding this range when proper maintenance practices are followed . Notably, surfaces experiencing extreme wear or exposure to harsh environmental conditions may have reduced lifespans. Conversely, well-maintained surfaces can achieve lifespans of 25 years or more, particularly in controlled environments where moisture and temperature factors are effectively managed.
Shock absorption capability represents a key variable that differs among various types of polyurethane binders. Softer binders are typically employed in cushioning applications, such as playground surfaces, where they must effectively absorb impact to reduce the likelihood of injuries from falls. Research indicates that polyurethane binders excel in shock absorption due to their unique compositional properties, allowing them to deform under stress and return to their original shape, thereby providing essential comfort and safety . This capability is particularly important in environments prioritizing children's safety.
Quantitative metrics for measuring wear resistance in polyurethane systems comprise standard tests, including ASTM G65, which assesses abrasion resistance through weight loss measurements after exposure to abrasive materials. These metrics provide vital insights into the longevity and performance of a surface under various wear conditions. Additional metrics may involve assessing changes in hardness and volume loss, crucial for evaluating the long-term viability of the binder .
Elastic recovery performance further distinguishes aromatic and aliphatic polyurethane binders. Aromatic binders typically exhibit increased rigidity compared to their aliphatic counterparts, which tend to be more flexible. This difference in elastic recovery can influence the choice of binder based on specific application requirements, such as whether a more resilient or softer surface is desired. The flexibility of aliphatic binders enables better performance under dynamic loads while preserving integrity over time .
Industry standards for evaluating the UV resistance of polyurethane binders, such as ASTM G154 and ISO 4892-2, are crucial for maintaining long-term performance. These standards assess how materials withstand prolonged exposure to ultraviolet light, which can lead to degradation and discoloration. Compliance with these benchmarks ensures that the surface systems remain visually appealing and functional over time .
Installation techniques also significantly affect durability. Proper preparation and application procedures are critical for achieving a stable substrate that can endure environmental stresses. Ensuring that the base layer is adequately compacted and that the binder is mixed at the correct ratios directly influences the durability of the surface. Poor installation can lead to premature failure, underscoring the necessity for skilled technicians during the installation process .
Finally, statistical data on the performance of polyurethane binders in extreme weather conditions demonstrate their robustness. Studies have shown that polyurethane binders effectively maintain their mechanical properties across a range of temperatures and humidity levels. For example, research indicates that polyurethane binders retain over 68% of their tensile strength after exposure to freeze-thaw cycles, underscoring their suitability for diverse climatic conditions .
The degradation of polyurethane binders over time is influenced by multiple factors, including hydrolytic deterioration and environmental stresses. Hydrolysis, particularly in ester-based polyurethanes, can lead to the breakdown of polymer chains, especially when combined with high temperatures and humidity. prolonged exposure to UV light, extreme heat, and chemical agents can exacerbate degradation, necessitating careful selection and application of materials .
the performance and durability of polyurethane rubber surface binders depend on a multitude of factors, from bond strength and wear resistance to environmental resilience and installation quality. By grasping these dynamics, one can appreciate the pivotal role that bond strength plays, particularly when considering the compatibility of binders with rubber granules like EPDM and SBR. This understanding sets the stage for examining the specific bond strengths and how they interact with various granule types, which will be key as we explore the next aspect of binder performance. As a leading expert in wet-pour and soft-tarmac solutions, Playground Repair Ltd. is committed to delivering high-quality systems that meet rigorous industry standards, backed by over 25 years of experience in the field.
Bond Strength to EPDM / SBR Granules
Bond strength to EPDM (Ethylene Propylene Diene Monomer) and SBR (Styrene-Butadiene Rubber) granules is a pivotal factor influencing the performance and longevity of surfaces bonded with polyurethane adhesives. Building on the understanding of bond strength metrics, comprehensive knowledge is essential for ensuring optimal performance and durability in various applications, including playgrounds, sports surfaces, and other outdoor structures.
Studies indicate that specific polyurethane binders achieve bond strength values on EPDM granules typically between 5 MPa and 7.78 MPa, influenced by formulation and application conditions documented by Li et al. (2023). In controlled tests, the mechanical strength of the polyurethane binder known as PU-AD-2 attained an impressive bond strength of 7.78 MPa, underscoring its superior performance when combined with EPDM granules, as evidenced in ScienceDirect (2022). The composition of the polyurethane adhesive profoundly impacts bond strength, with optimal adhesion typically achieved at an approximate mixture ratio of 20% adhesive to the total granule content, as reported by Fox Bau (2023). This precise formulation not only ensures robust bonding but also protects the color integrity of EPDM granules, maintaining their aesthetic vibrance across various applications.
Effective surface preparation is essential for improving bond strength between polyurethane adhesives and EPDM surfaces. Proper cleaning and treatment processes significantly elevate the surface energy of EPDM, facilitating a lasting bond. Data from the Gluegun blog indicates that maintaining a clean, dry, and contaminant-free EPDM surface is paramount for achieving a robust bond, as highlighted in Gluegun.com (2023). Contaminants such as oils, dust, or moisture can create barriers that impede adhesion, emphasizing the necessity for thorough surface preparation to achieve optimal bonding results.
Research reveals that polyurethane adhesives also demonstrate effective adhesion properties with SBR granules. Various studies have employed T-peel strength tests to quantify bond strength in polyurethane adhesives, revealing that SBR granules respond effectively to diverse bonding agents . Notably, one investigation found that polyurethane adhesives exhibited remarkable bond strength increases, achieving bond splitting strength figures of up to 91.4% when optimal conditions were maintained (Wiley Online Library, 2022). This research underscores the effectiveness of polyurethane systems when applied to SBR granules under specifically controlled environmental conditions.
the size of the granules significantly affects bond strength outcomes. Research indicates that larger granules lead to increased bond strength due to an enhanced surface contact area with the binder. A documented study revealed that as granule size increases, corresponding bond strength increases were also observed, while the duration of compaction played a critical role in achieving favorable bonding results . Optimizing these factors can substantially enhance the mechanical performance of the final product, ensuring durability and longevity in various applications.
In considering tensile strength, the average tensile strength of polyurethane systems applied to EPDM surfaces generally measures around 210 psi (Carlisle-Syntec, 2023). This figure is vital, as it reflects the bonded surfaces' ability to endure various stresses without failure. A strong tensile strength contributes significantly to the effectiveness of the surface in practical conditions, ensuring resilience against pedestrian traffic, environmental exposure, and other stressors.
other critical factors such as environmental conditions are paramount in influencing bond strength, affecting curing rates and adhesive performance. Research reveals that contamination from environmental exposure can degrade adhesive performance, emphasizing the need for protective measures during application (Oliver LLP, 2023). Extreme temperatures can notably reduce the strength of polyurethane bonds, especially at temperatures exceeding 302 °F (150°C) . Hence, maintaining optimal environmental conditions during and after application is crucial for ensuring bond longevity.
Common failure modes in systems bonded to EPDM and SBR granules often occur due to adhesive incompatibility, which can subsequently result in bond failures. Such incompatibility typically stems from the selection of inappropriate adhesive formulations, resulting in inadequate bonding performance (HM Royal, 2023). Understanding these failure modes is essential for implementing corrective actions during the bonding process, thereby enhancing long-term performance. The insights into common failure modes provide valuable context for the ongoing evaluation of bond strength and adhesive performance.
In laboratory settings, various testing methodologies are employed to assess bond strength quantitatively. To ensure robust performance, various testing methodologies are utilized, including widely recognized nominal bond strength tests such as macro-shear, micro-shear, and macro-tensile tests. The effectiveness of these tests depends on their ability to accurately measure the force exerted on the adhesive bond relative to the bonding area . This quantifiable approach facilitates reliable assessments and comparisons of different adhesives, ensuring that only the most effective binders are selected for specific applications.
the mechanical properties of the substrate significantly influence bond strength outcomes. Surface roughness can enhance bonding area, leading to heightened mechanical bonding strength . Chemical alterations to the substrate can also adversely affect bond strength, highlighting the necessity for meticulous consideration of substrate properties during adhesive system selection.
Established industry standards, such as those from ASTM International, guide the measurement of bond strength in polyurethane applications, promoting consistency and reliability across industry practices. ASTM International provides vital testing procedures that ensure reliable evaluations of bond strength, such as ASTM D3574, focusing on measuring flexible polyurethane foam (Polyurethane Foam Association, 2023). These standards promote consistency in testing methodologies, enabling manufacturers to achieve optimal performance in their adhesive applications.
understanding the intricacies of bond strength to EPDM and SBR granules requires careful examination of a multitude of factors. This exploration not only enhances the performance of polyurethane adhesive systems but also lays the groundwork for considering their resilience to environmental challenges, such as UV exposure and wear over time. As we transition into the next segment of this guide, we will delve deeper into the effects of UV resistance and yellowing behavior, critical for sustaining both the aesthetic and functional qualities of polyurethane-based surfaces.
UV Resistance and Yellowing Behaviour
UV resistance and yellowing behaviour are critical characteristics of polyurethane binders that significantly influence the longevity and aesthetic quality of surfaces exposed to environmental elements. Prolonged exposure to ultraviolet (UV) radiation leads to substantial yellowing in polyurethane materials, particularly in formulations that utilize aromatic isocyanates. Building on this understanding, it is essential to recognize that over 50% of aromatic polyurethanes exhibit considerable yellowing after prolonged exposure to UV light. This statistic underscores the critical importance of careful material selection for outdoor applications where UV exposure is unavoidable.
Polyurethane compounds are particularly sensitive to UV radiation, which spans wavelengths from 295 to 380 nm, necessitating careful material selection. When these materials are subjected to UV light, a process known as photodegradation occurs, resulting in notable changes to the material properties. Such degradation highlights the necessity of integrating effective UV inhibitors within polyurethane formulations to combat the adverse effects of UV exposure. The degradation primarily results from an oxidation reaction, which accelerates yellowing and diminishes the aesthetic appeal of the material. For instance, studies indicate that aromatic polyurethane can manifest visible colour shifts after merely 200 hours of UV exposure, as documented in the study conducted by Lawrence Industries.
The differences in UV resistance ratings among polyurethane binders are noteworthy and warrant careful consideration in material selection. the formulation of polyurethane binders directly influences these ratings. Aliphatic polyurethanes exhibit superior UV protection compared to their aromatic counterparts, thereby enhancing their suitability for outdoor applications. Aliphatic variants exhibit enhanced colour stability and resistance to chalking, significantly lowering the likelihood of yellowing. This property renders aliphatic polyurethanes a preferred choice for applications requiring high durability against sunlight and adverse weather conditions, as shown in "High-Quality Polyurethane UV Coatings for Maximum Sun Protection" (2023).
To evaluate the UV resistance of polyurethane systems, several standardized tests are utilized. The AATCC Test Method 16-2004 measures colourfastness to light, while the ASTM D4329-05 assesses UV exposure durability. These standardized assays provide crucial insights into how effectively a polyurethane binder can withstand prolonged sunlight exposure without exhibiting significant yellowing or degradation of its structural integrity, as corroborated by "UV Light Resistance Testing for Polyurethane and Vinyl Materials" (2023).
Additives such as UV inhibitors are instrumental in enhancing the UV resistance of polyurethane binders. Even a modest percentage of ultraviolet inhibitors can dramatically improve resistance to UV damage, thereby mitigating yellowing. However, it is paramount to select these additives with caution to ensure they do not negatively impact other performance attributes of the polyurethane material. The study "Polyurethane Coating Chemistry - Chemical-Supermarket.com" (2023) elaborates on the effectiveness of such additives.
Environmental factors, including humidity and temperature, significantly contribute to the accelerated yellowing in polyurethane binders. Research shows that exposure to UV light in humid conditions can accelerate the rate of yellowing in polyurethane materials. Consequently, selecting the right polyurethane binders for outdoor use becomes paramount. Research indicates that aliphatic binders tend to demonstrate a longer lifespan regarding UV stability compared to aromatic binders, making them more suitable for environments with extended sunlight exposure. While aliphatic binders may be priced at twice that of aromatic options, their performance advantages justify the additional cost in various applications, as highlighted in "Rubber Binders: Aromatic vs Aliphatic - Playground Audit" (2023).
User satisfaction with polyurethane applications is significantly affected by the occurrence of yellowing, which impacts perceptions of quality. Surveys indicate that dissatisfaction occurs due to unattractive yellowing effects, which can foster perceptions of diminished quality and necessitate premature material replacement, according to "Photo-oxidation studies on polyurethane coating: Effect of additives" (2023).
The long-term effects of UV exposure on the mechanical properties of polyurethane have also been extensively studied. Prolonged UV exposure can lead to significant reductions in elastic modulus and mechanical performance. Notably, the degradation of these properties is influenced not only by the duration of UV exposure but also by environmental conditions such as temperature and humidity, as reported in "Study of UV-aging of thermoplastic polyurethane material" (2023).
Innovations in polyurethane technology are continually emerging to enhance UV stability, including new formulations and advanced additives. Research efforts are primarily focused on identifying new formulations and additives that can effectively counteract the deleterious effects of UV exposure on polyurethane products, ensuring that they maintain their integrity and aesthetic appeal over extended periods, as cited in "Recent Advances in UV-Cured Encapsulation for Stable and Durable Applications" (2023).
comprehending the complexities surrounding UV resistance and yellowing behaviour in polyurethane binders is vital for selecting the appropriate materials for your projects. By taking into account factors such as formulation, additives, environmental influences, and testing methods, you can effectively navigate the challenges posed by UV exposure, ensuring the durability and performance of polyurethane surfaces in outdoor applications. As we move forward, it will be beneficial to explore how these characteristics interact with shock absorption, elasticity, and wear resistance, all crucial for optimizing the performance of polyurethane systems in demanding environments.
Shock-Absorption, Elasticity & Wear Resistance
Shock-Absorption, Elasticity & Wear Resistance are essential properties of polyurethane binders that make them ideal for various applications. Polyurethane binders excel in shock absorption, elasticity, and wear resistance, key indicators of their performance metrics, particularly in applications demanding resilient, high-performance materials. Understanding these properties is essential, as they directly influence the safety and comfort of environments such as playgrounds, sports facilities, and industrial settings. Polyurethane surfaces are specifically renowned for their ability to absorb shock effectively, which establishes them as leading materials in this domain. The average shock absorption rating for diverse polyurethane binders exceeds 45%, underscoring their prominence.
the performance of polyurethane in absorbing impacts is further influenced by the thickness of the applied layer. As layer thickness increases, the material's capacity to absorb and dissipate energy concurrently enhances, leading to improved performance in impact scenarios. Optimal thickness ensures effective energy dissipation while providing the requisite resilience to absorb impacts efficiently . However, it is essential to strike a balance; excessive thickness may adversely affect user comfort and usability, particularly in contexts such as playgrounds and sports surfaces.
Polyurethane binders exhibit superior elastic properties compared to traditional materials like rubber and concrete, which enhances their utility in various demanding applications. Specifically, polyurethane systems demonstrate unique elastic characteristics attributed to their molecular structure, allowing them to deform under load and revert to their original shape without incurring permanent deformation. To quantitatively assess elasticity, tensile testing is commonly utilized, revealing valuable data on the elastic modulus of polyurethane formulations.
Research shows that elongation at break for specific polyurethane binders can reach a remarkable 1122.52%, which underscores their exceptional resilience compared to conventional materials . Advanced techniques, including atomic force microscopy (AFM) and near-infrared (NIR) spectroscopy, have emerged, enabling researchers to achieve nanoscale resolution in studying the elastic properties of polyurethanes .
Industry benchmarks for wear resistance in polyurethane applications are established through rigorous testing protocols. One premier methodology is ASTM D5963 , Standard Test Method for Rubber Property , Abrasion Resistance (Rotary Drum Abrader), which allows for comprehensive assessments through both two-body and three-body abrasion measurements . Polyurethanes have consistently demonstrated superior wear resistance, effectively enduring challenges posed by high-impact environments and frequent utilization. The remarkable resilience of polyurethane elastomers stems from their high elasticity and propensity for elastic deformation, which collectively mitigate wear and extend service life .
Distinct formulations of polyurethane significantly affect wear resistance over time, adapting mechanical properties to meet specific application needs. Thermosetting polyurethanes, characterized by their cross-linked structures, generally exhibit higher abrasion resistance when compared to thermoplastic variants, rendering them suitable for demanding environments . Polyurethanes are engineered with varying hardness levels, from soft, flexible formulations to hard, rigid types, accommodating a wide array of applications that necessitate differing degrees of wear resistance, durability, and shock absorption .
Quantitative analyses concerning the performance of polyurethane in high-impact environments accentuate its adaptability and resilience. In sectors such as automotive, aerospace, and hydraulic systems, urethane shock absorbers are recognized for their exceptional resistance to oils, solvents, and other rigorous environmental conditions . The global polyurethane market has experienced significant growth, currently valued at approximately USD 78.07 billion, with a projected compound annual growth rate (CAGR) of 4.5% from 2024 to 2030, highlighting the material's essential role in high-impact scenarios .
Fluctuations in temperature significantly affect the elastic properties of polyurethane binders. Research indicates that as temperatures rise, the elastic modulus typically decreases, signifying a transition from a predominantly elastic to a more viscous state, which can adversely affect material performance in high-temperature environments . Conversely, lower temperatures generally lead to increased modulus and yield strength, thereby enhancing the toughness of the material .
As we explore these attributes of polyurethane binders, it becomes evident that they are not only designed for optimal performance but also require careful selection based on specific application needs. Understanding how these properties interact with external factors is crucial, particularly when considering the various climates and conditions in which these binders will be used. This understanding lays the groundwork for making informed decisions related to binder selection, a vital aspect we will delve into next, as we examine how to match binders to the specific needs of different environments and budgetary considerations.
Binder Selection Quick Reference
Binder selection is crucial for polyurethane rubber surface applications, as it involves considering various critical factors, particularly those tied to climate conditions, budget constraints, color options, performance metrics, safety standards, and the compatibility of binders with existing surface materials. This comprehensive guide serves as a quick reference for evaluating different binders, enabling informed decisions that align with specific project requirements and environmental contexts.
Climate Considerations
Understanding the impact of climate on binder selection is paramount. The longevity and performance of the binder are significantly influenced by local climate conditions, including temperature fluctuations, humidity levels, and exposure to ultraviolet (UV) light. For instance, warm climates can soften binders, potentially leading to issues such as rutting, while cold climates may induce brittleness, resulting in a higher incidence of cracks (World Highways). Therefore, selecting a binder that aligns with historical climatic data and anticipated temperature extremes is crucial for bolstering performance (Pavement Interactive).
Considering the local climate conditions not only affects binder selection but also significantly impacts maintenance strategies and long-term durability. The Superpave Performance Grading (PG) system provides a framework for assessing binder suitability based on climatic conditions. This performance-oriented approach evaluates how binders respond to specific temperature and loading scenarios, ensuring that the selected binder maintains its structural integrity throughout its intended lifespan (Pavement Interactive). Utilizing PG specifications allows for the determination of which binder grade will best withstand the environmental elements prevalent in your region. According to Liu et al. (2023), the selection of a climate-appropriate asphalt binder significantly enhances pavement surface longevity, providing empirical support for binder selection in various climatic scenarios (Liu, Y., & Zhang, L. (2023). Climate change and asphalt binder selection across Ontario. ScienceDirect).
Budget Implications
Budget implications are significant in the decision-making process regarding the selection of appropriate binders. While aromatic polyurethane binders frequently present a cost-effective choice, they often fall short in durability compared to aliphatic variants (Fairmont Industries). It is essential to balance cost with performance expectations; while aromatic binders can fulfill specific budgetary requirements, they may not deliver the same longevity and UV stability as their aliphatic counterparts (Robertson Surfaces).
With budget constraints influencing material selection, it is also vital to consider the aesthetic aspect of your project. When evaluating options, consider eco-friendly binders that come with lower volatile organic compound (VOC) emissions. These green alternatives can be slightly more expensive but could yield long-term savings through reduced maintenance costs and enhanced durability (Fairmont Industries). Thus, while the initial investment may be higher, investing in a quality binder could lead to lower lifecycle costs. Understanding the average costs associated with different binder types, such as aromatic and aliphatic polyurethane, can greatly impact the selection process for surface applications. For instance, asphalt binders typically have a reference cost derived from market prices, influencing budget allocations (WSDOT).
Color Options
Color options for polyurethane binders are another important consideration that can influence the decision-making process. Various binder types offer a spectrum of color choices, ranging from bold reds and greens to more neutral tones (ESCO Plastics). Aliphatic binders, in particular, provide superior UV stability and color retention, making them an excellent choice for outdoor applications where both aesthetics and durability are vital (BBSurfaces). In contrast, aromatic binders, while generally less expensive, may exhibit color degradation over time when exposed to sunlight.
It is essential to collaborate with suppliers to understand the available color options and their implications regarding performance and aesthetics. Custom colors are often achievable but may come with additional costs, so discussing these specifications beforehand can streamline the selection process. After addressing aesthetic choices, it is crucial to evaluate the performance metrics that ensure the chosen binder meets application demands.
Performance Metrics
Prioritize performance metrics based on the intended use of the surface. For play areas or athletic fields, shock absorption and wear resistance are critical to ensure safety and longevity (CPSC). Metrics such as elasticity, bond strength to ethylene propylene diene monomer (EPDM) or styrene-butadiene rubber (SBR) granules, and resistance to UV light should be evaluated to ensure that the selected binder meets the demands of its application (MDPI).
understanding the specific performance characteristics required for different surfaces can guide binder selection. High-traffic areas may require binders that offer enhanced durability and low maintenance, while decorative surfaces might prioritize aesthetics over physical resilience (Pavement Interactive). By aligning the binder's properties with its intended use, you can avoid common pitfalls associated with premature failure or unsatisfactory performance.
Compliance with Safety Standards
Compliance with established safety standards, such as ASTM and CPSC guidelines, is non-negotiable for playground and recreational surface applications. Relevant safety regulations dictate specific requirements for surface materials, including adequate shock absorption and minimum fill depths (CPSC). Selecting a binder compliant with safety standards is essential to ensure user protection, especially for children's play areas.
the binder should not introduce any toxic elements into the environment, thereby aligning with modern safety and environmental standards (Health and Environment). Choosing a compliant binder not only guarantees user safety but also mitigates liability risks for operators responsible for the play area.
Matching Binders to Existing Materials
The compatibility of the selected binder with existing surface materials, such as asphalt or concrete, is another essential factor in ensuring successful integration. For effective adhesion, it is crucial that the binder is appropriate for the surface texture and material composition of previous installations (Bepex). This ensures that the binder can effectively bond to the underlying materials and provide a seamless finish.
some existing surfaces may require specific types of binders to maintain their structural integrity and appearance. For example, utilizing a PG binder specification in surface treatments may not yield the desired results due to differences in application methods and binder characteristics (Texas DOT). Therefore, conducting a thorough assessment of existing materials and their needs is vital before finalizing a binder choice.
Local Climate and Longevity
The local climate not only influences the immediate performance of the binder but also its long-term longevity. Specific binder types may degrade faster under certain conditions, such as extreme temperatures or moisture cycles (ScienceDirect). Therefore, selecting a climate-appropriate binder can significantly reduce maintenance frequency and enhance the lifespan of the installation (MDPI).
Temperature variations, especially in regions with significant seasonal shifts, can lead to materials expanding and contracting, causing stress that may compromise binder integrity (Old Town Pavers). A carefully selected binder can help mitigate these issues, ensuring that your surface remains intact and functional for years to come.
Average Costs Associated with Different Binder Types
Understanding the average costs associated with different binder types can significantly impact the selection process. The cost may vary based on the binder type, environmental conditions, and specific project requirements (WSDOT). For instance, asphalt binders typically have a reference cost that is averaged from market prices, influencing budgeting (PSU).
It is essential to factor in not only the material costs but also installation and maintenance expenses. Quality binders may come at a higher upfront cost but can save money in the long run through reduced repair needs and increased durability (Fairmont). Thus, a clear financial analysis should guide your binder selection process to achieve the best balance between cost and performance.
Common Missteps in Binder Selection
Several common missteps in binder selection, such as inadequate evaluation of performance metrics and neglecting environmental conditions, can potentially lead to significant product failures. One frequent error is the inadequate evaluation of performance metrics against the expected conditions of use, resulting in binders that fail to meet application demands (Paveman Pro).
Another critical misstep is overlooking the importance of proper mix designs. An improper ratio of binder to aggregate can lead to premature failure, such as alligator cracking, indicating structural weakness (NEWARE). neglecting to assess environmental conditions during binder selection can result in long-term consequences, including binding material degradation due to moisture or extreme temperatures (Pavement Interactive).
Resources for Evaluation
Consumers have access to a variety of resources to assist in evaluating binder options effectively. Industry publications and studies can provide insights into the latest advancements in binder technology and performance expectations (Blue Summit Supplies). engaging with suppliers who can offer brand tests, product samples, and comprehensive guidance can streamline the selection process.
Consulting commercial printers or manufacturers specializing in binding options can also yield valuable insights, particularly when considering tailored solutions for specific applications (Thomas Group Printing). These resources empower consumers to make informed decisions, leading to better outcomes and longer-lasting installations.
By carefully considering these factors in binder selection, you can ensure that your choice enhances the performance, safety, and longevity of your polyurethane rubber surfaces. Choosing the right binder is vital not only for immediate effectiveness but also for sustaining the surface's quality over time. This understanding sets a strong foundation for delving into how environmental conditions, color choices, and compliance with safety standards will further influence your selection process.
Matching Binder to Climate, Colour & Budget
Matching binder to climate, colour, and budget is essential for achieving optimal performance, ensuring long-term durability, and fostering aesthetic appeal in outdoor applications utilizing polyurethane rubber surface binders. The intricate relationship among these factors can decisively impact the success of your project. Understanding how each factor interacts allows for informed decisions that meet both functional and aesthetic needs, ultimately optimizing your investment.
Climate serves as a pivotal criterion in selecting binder materials for outdoor applications. Variations in temperature, humidity, and other environmental conditions can drastically affect the performance characteristics of polyurethane binders. For instance, according to R. Sepaspour et al. in their comprehensive study titled "Global Warming and Its Effect on Binder Performance Grading" (2024), rising temperatures may result in diminished stiffness properties, leading to softening of the binder and increased susceptibility to rutting. Conversely, lower temperatures can cause brittle fractures, compromising the material's integrity during colder months. Hence, selecting a binder tailored to withstand specific regional climate conditions is essential to guarantee longevity and reliability.
Transitioning from climate considerations, it's also critical to evaluate color options. In sunny climates, specific color options such as light hues and thermochromic pigments offer significant advantages. Light-colored or thermochromic binders effectively reflect solar energy, thus prolonging surface lifespan and enhancing user comfort. Research focusing on thermochromic materials shows that the ability to reflect solar energy can lead to a substantial decrease in temperature-related degradation of binder materials, ultimately preserving their performance.
When selecting color options for different binder types, ensure they align with the climatic conditions of the installation area. Neutral colors such as whites and grays are beneficial as they typically absorb less heat, mitigating degradation from UV exposure. While darker colors may be aesthetically pleasing, they warrant careful consideration due to their potential for heat retention, which can accelerate the aging process of the binder, thus affecting its durability.
Budget considerations are equally vital in the selection process, influencing both material choice and project sustainability. Opting for less expensive binders may be tempting, yet it often leads to increased maintenance costs and frequent replacements. In fact, the price difference between standard color binders and custom colors can be significant, sometimes reaching an upcharge of 10-12% for specific custom colors, as noted in various pricing analyses. Therefore, it is wise to balance budget considerations with the potential longevity and maintenance requirements of the selected binder, ensuring a more sustainable investment.
consider the adaptability of the chosen binder to local environmental conditions, as this will directly impact maintenance costs. As highlighted in previous sections, the performance of binders directly impacts maintenance frequency and project costs. Certain binder types may require frequent upkeep due to environmental stresses, escalating project expenses. For example, some binders may have a reduced lifespan in high humidity environments, necessitating increased investment in maintenance and repairs. Thus, selecting high-quality materials specifically designed for expected local conditions can save costs over time and enhance the project's sustainability.
Addressing misconceptions surrounding color, budget, and performance is essential. Many individuals believe that choosing a cheaper binder is sufficient without recognizing that this choice can compromise performance and lead to increased maintenance needs. This misunderstanding can skew decision-making processes, resulting in selections that adversely affect both aesthetic appeal and functional performance, as highlighted in multiple studies.
To assist in selecting binders that maintain aesthetic appeal over time, several guidelines should be evaluated. Key considerations include:
- Choosing high-quality materials that provide UV resistance and longevity.
- Integrating protective features that preserve the binder's appearance against environmental wear.
- Utilizing eye-catching designs to enhance visual interest and foster community engagement in recreational or educational spaces.
Ultimately, the complexities of binder selection encompass not only immediate performance and aesthetic considerations but also compliance with industry safety standards, which are paramount for ensuring user protection. Understanding these layers of binder selection allows for a thorough evaluation that accounts for safety regulations, thus ensuring that the materials chosen not only serve their intended purpose but also meet the legal and ethical expectations of outdoor spaces. By prioritizing durability and compatibility with local environmental conditions, you enhance both the enjoyment and safety of outdoor spaces, ensuring they remain visually attractive for years to come.
Compliance with EN 1176 / EN 1177 Safety Standards
Compliance with EN 1176 and EN 1177 safety standards is essential for ensuring the safety of playgrounds and recreational areas for children. The EN 1176 standard governs the safety of playground equipment, while EN 1177 specifically addresses impact-attenuating surfaces, ensuring the materials utilized in these environments adhere to stringent safety criteria.
The fundamental mandates of the EN 1176 safety standard that pertain to rubber surfaces dictate that rubber surfaces must provide adequate cushioning to mitigate the risk of injury from falls. This standard is organized into seven parts, with Part 1 delineating general safety requirements and test methodologies. The subsequent sections detail specific safety criteria tailored to various types of equipment and surfacing. It is vital for manufacturers and playground operators to adhere to these regulations, as they govern the safety and operability of play areas in public domains, such as parks and schools.
Building on the need for rigorous compliance, assessments are essential to confirm that materials meet the standards established in EN 1176. Compliance assessments are typically conducted by accredited third-party agencies, which validate the performance and reliability of materials used in playground surfacing. Non-compliance exposes manufacturers to substantial legal liabilities and safety risks, including both civil and criminal consequences, as it may subject users to hazardous conditions.
To achieve compliance with the EN 1177 safety standards, specific testing protocols assess the impact-attenuating properties of playground surfaces. These protocols involve calculating the HIC (Head Injury Criterion) value, which quantifies the potential for head injuries resulting from falls onto the surface. The maximum permissible HIC value under EN 1177 is stipulated at 1000, representing a critical threshold for safety that must be satisfied to protect children from severe injuries. This testing is essential, as it not only aids in maintaining compliance but also fosters public confidence in the safety of playground equipment and surfaces.
adherence to safety standards underscores the necessity for binders used in wetpour rubber surfaces. To comply with EN 1177, polyurethane binders must exhibit exceptional shock absorption and energy attenuation properties, ensuring that the surfaces effectively mitigate the impact forces experienced during falls. The synergy of EPDM granules and polyurethane binders generates a resilient and secure surface that meets the energy absorption mandates outlined in EN 1177.
The pathway to obtaining certification of compliance with EN 1176 and EN 1177 is intricate. It encompasses comprehensive audits and inspections that evaluate both the manufacturing process and the final product's performance against the established standards. Manufacturers often collaborate with third-party testing agencies, such as TÜV Nord or the British Standards Institution (BSI), to validate compliance through extensive inspections and testing of materials. Upon successful completion of these evaluations, manufacturers receive certification, allowing them to market their products as compliant with the pertinent safety standards.
Understanding the implications of these standards lays the groundwork for evaluating performance metrics, which will be critical in ensuring the longevity and user safety of playground surfaces. Failure to comply with EN 1176 and EN 1177 standards exposes manufacturers to substantial legal liabilities and safety risks. The injuries sustained from non-compliance can range from minor injuries to severe consequences, often resulting in legal action against manufacturers and operators. Therefore, compliance serves not only to protect children but also to shield manufacturers from potential lawsuits and financial liabilities.
The ramifications of EN 1176 and EN 1177 extend beyond immediate compliance; they significantly shape market trends in safety surfacing. As awareness of safety standards escalates, so too does the demand for compliant materials. Manufacturers increasingly focus on creating high-quality, compliant surfacing solutions that meet or exceed these rigorous safety benchmarks. This shift towards compliance is steering the evolution of innovative materials and techniques in the playground surfacing market, promoting a safer play environment for children.
Evaluating the average costs associated with compliance with EN 1176 and EN 1177 indicates that manufacturers and operators should prepare for financial implications. The costs of playground equipment compliant with EN 1176 can span from £2,000 to £20,000, while playground surfacing compliant with EN 1177 typically averages between £40 and £100 per square meter. These figures underscore the capital investment necessary to ensure safety and compliance within playground environments.
The evolution of safety standards, influenced by regulatory shifts and increased public consciousness, is transforming the playground safety landscape. Manufacturers are required to adapt to these evolving requirements by prioritizing eco-friendly practices and materials in their product development. The continuous advancement and refinement of safety standards, alongside an amplified focus on sustainability, will likely influence future binder development, encouraging innovation in the creation of safer and more environmentally responsible playground surfacing solutions.
the nuanced understanding of compliance with EN 1176 and EN 1177 not only ensures safety in playground environments but also sets the stage for a deeper exploration of how these standards integrate with the performance metrics of various materials used in surfacing. As we shift our focus, it will be essential to examine the specific performance characteristics that underpin safety and durability, ensuring that the surfaces not only meet regulatory requirements but also provide a secure environment for children to play and grow.