Poured In Place Rubber Repair
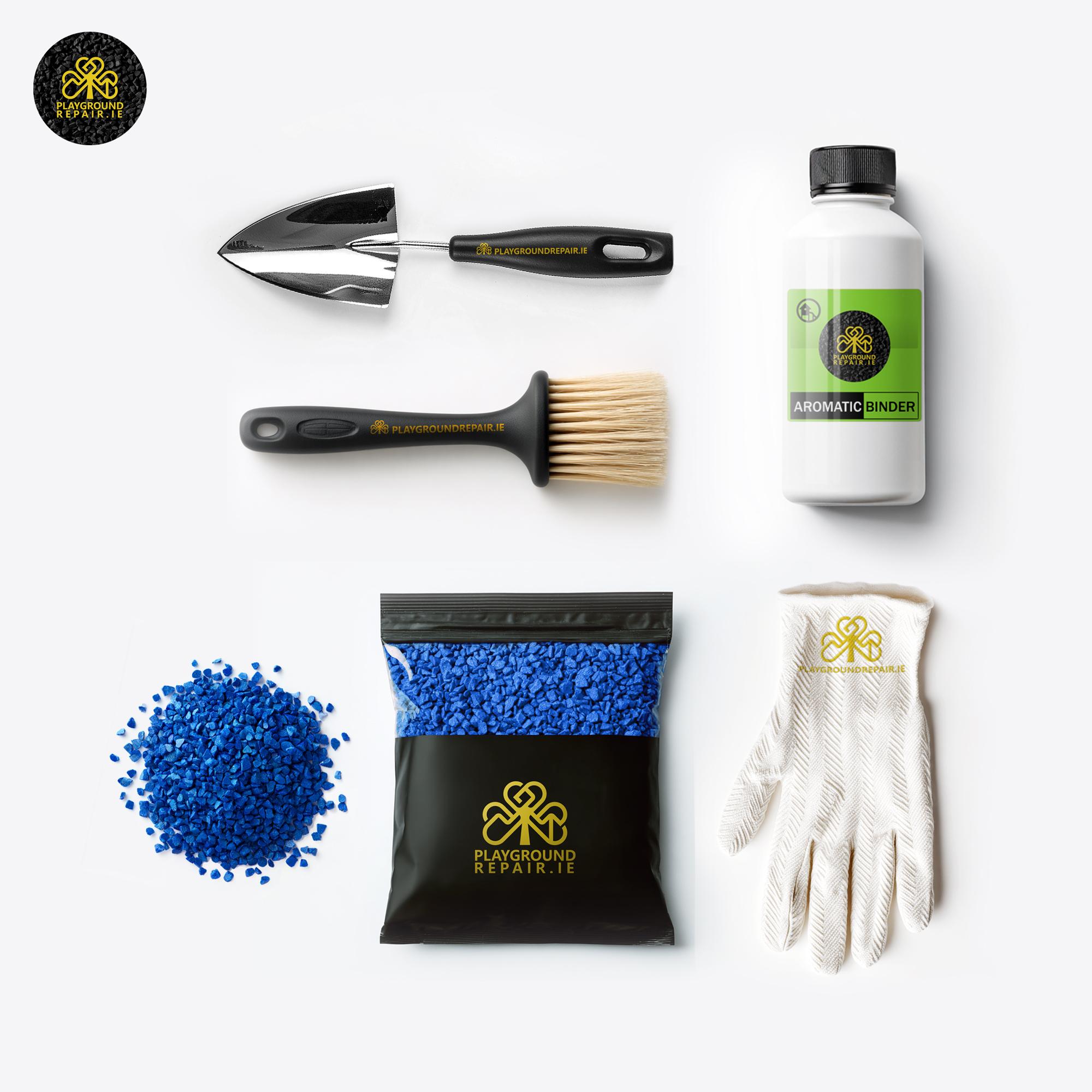
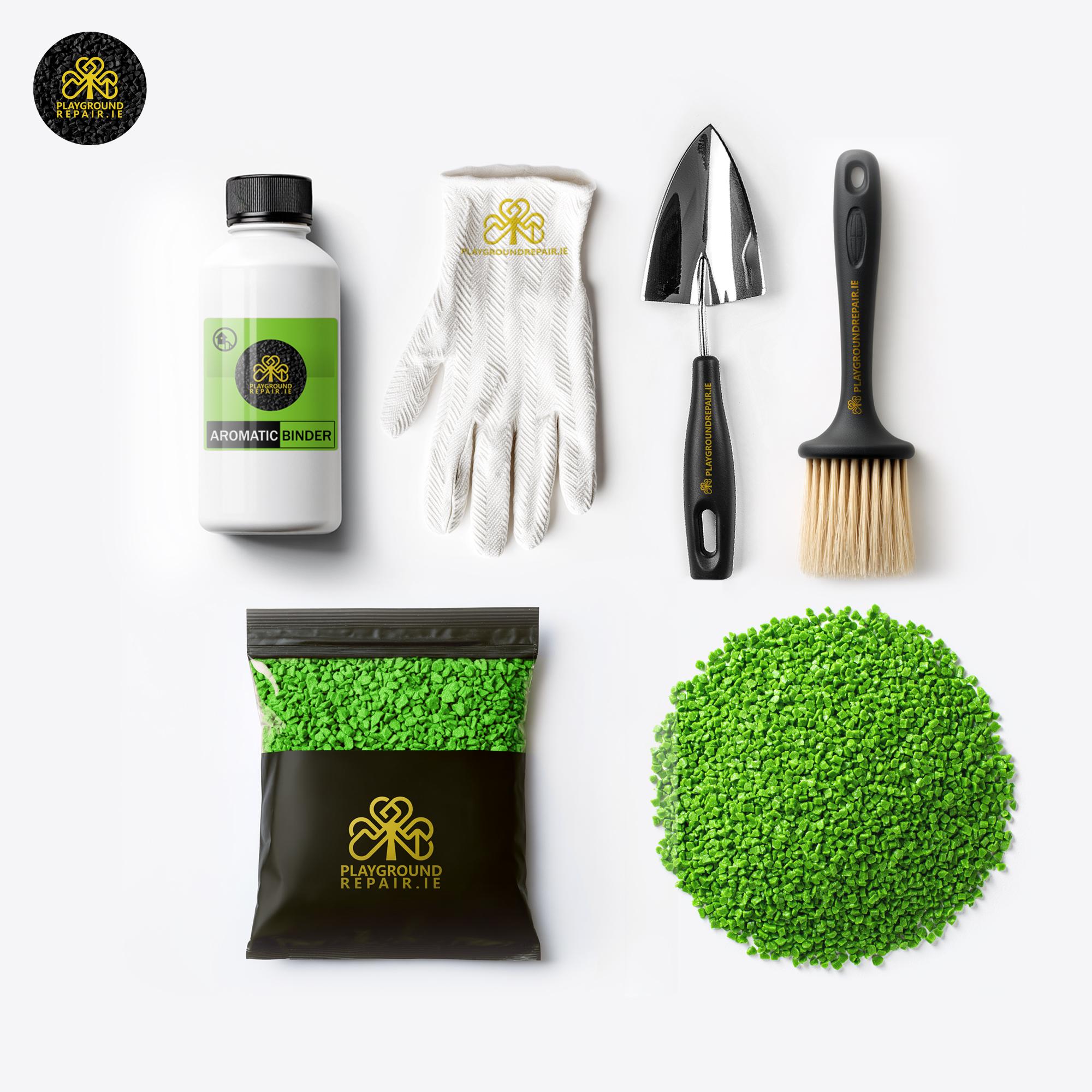
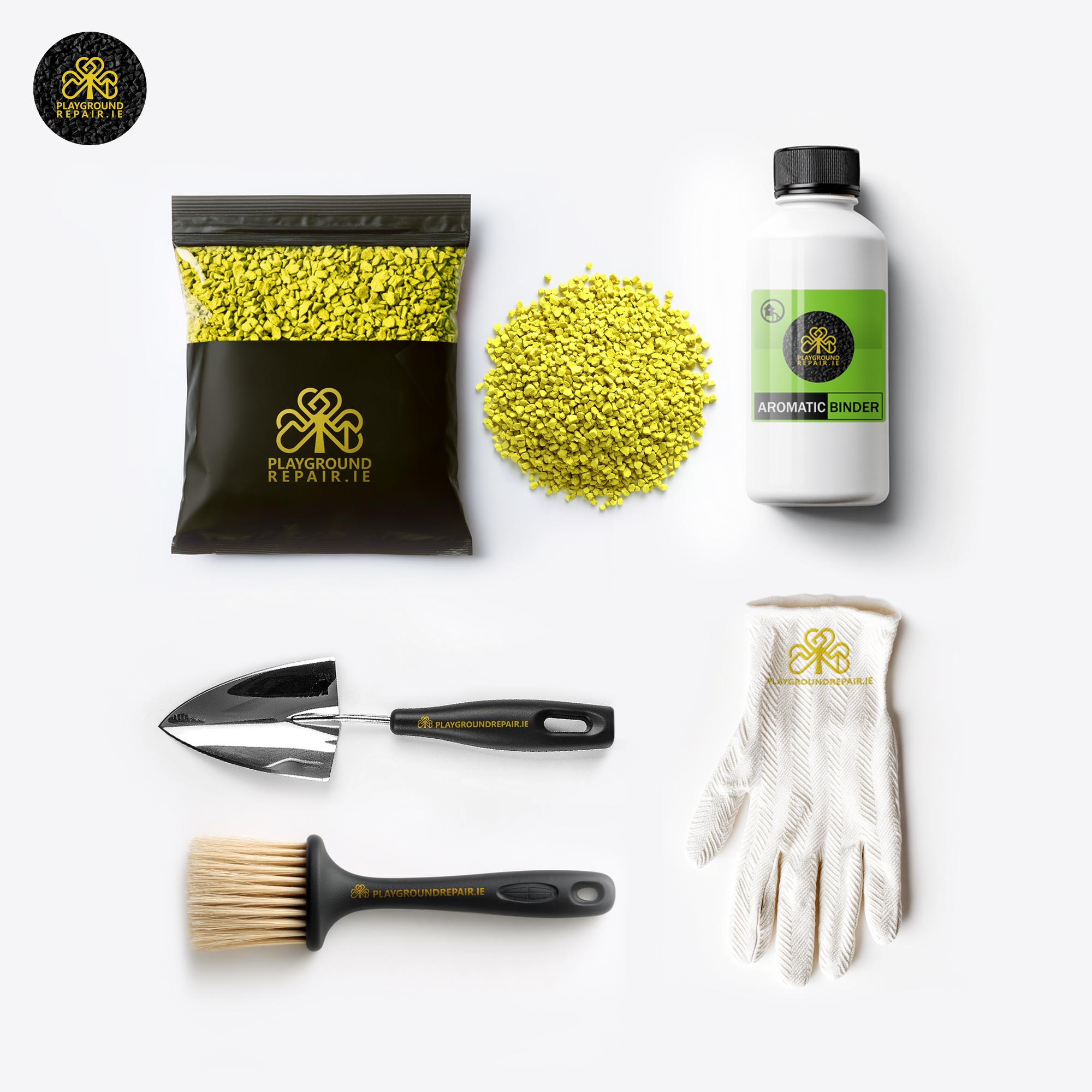
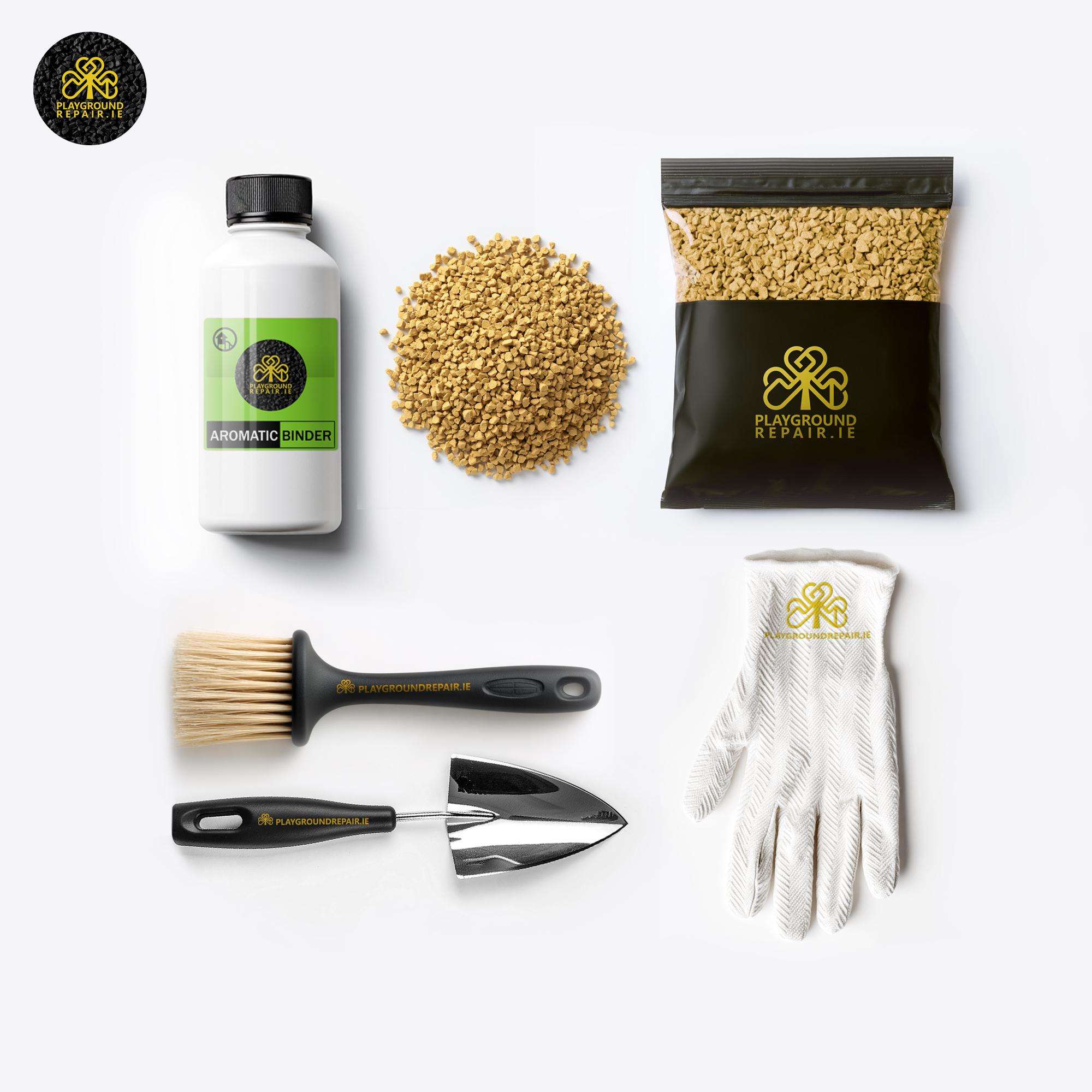
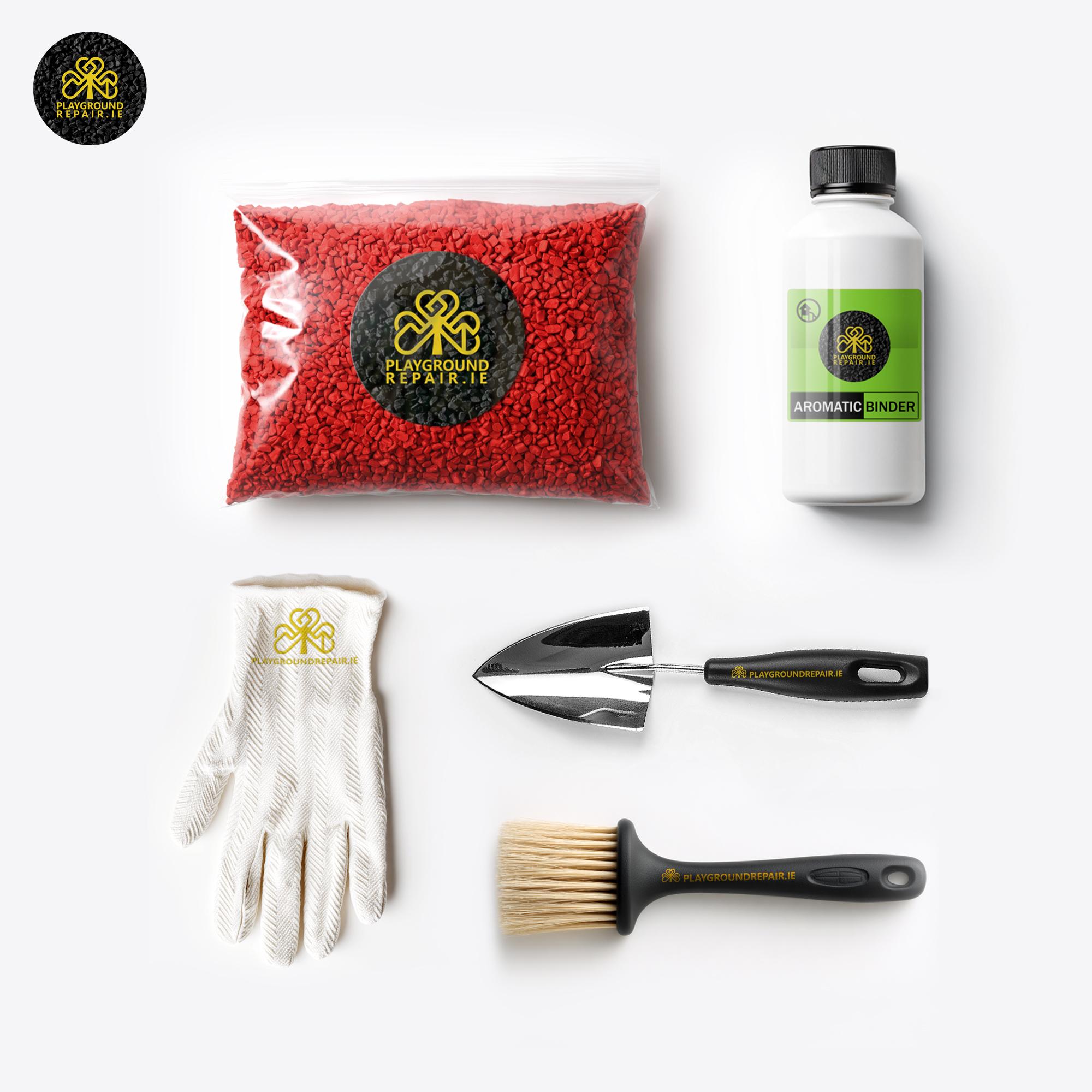
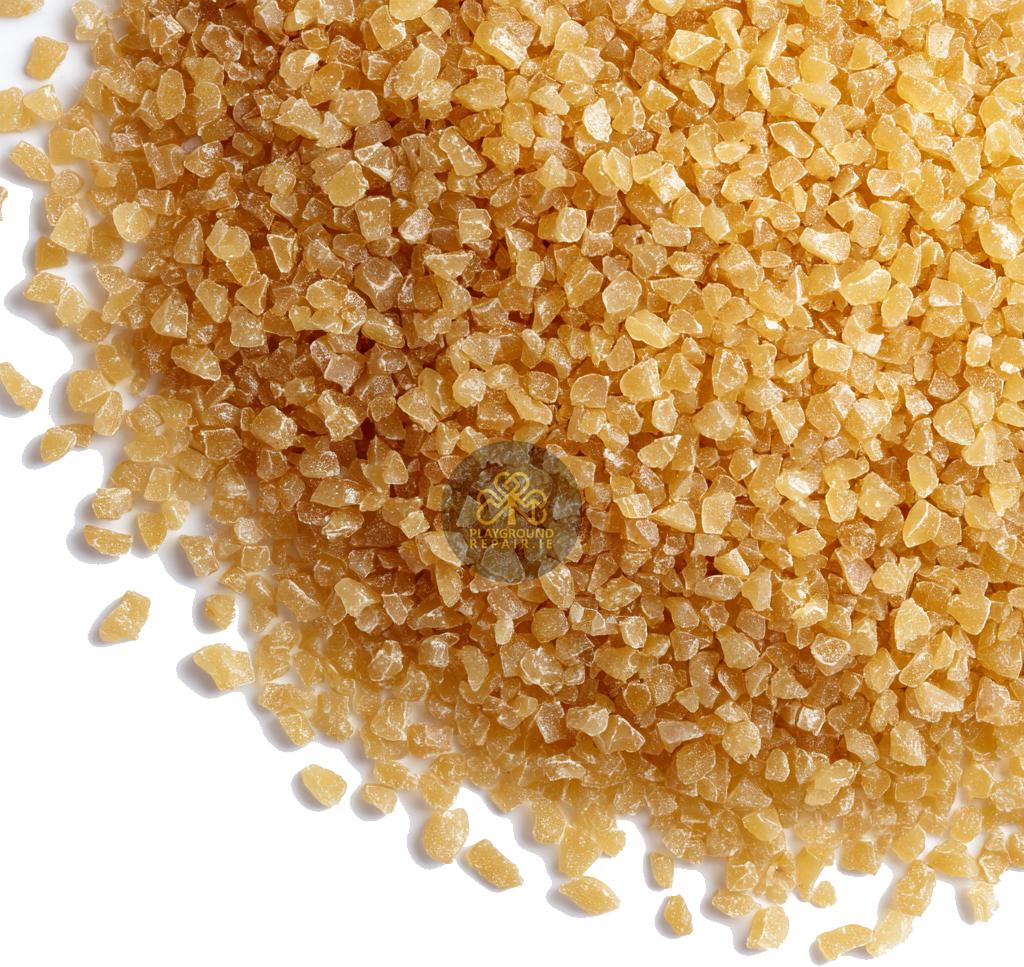
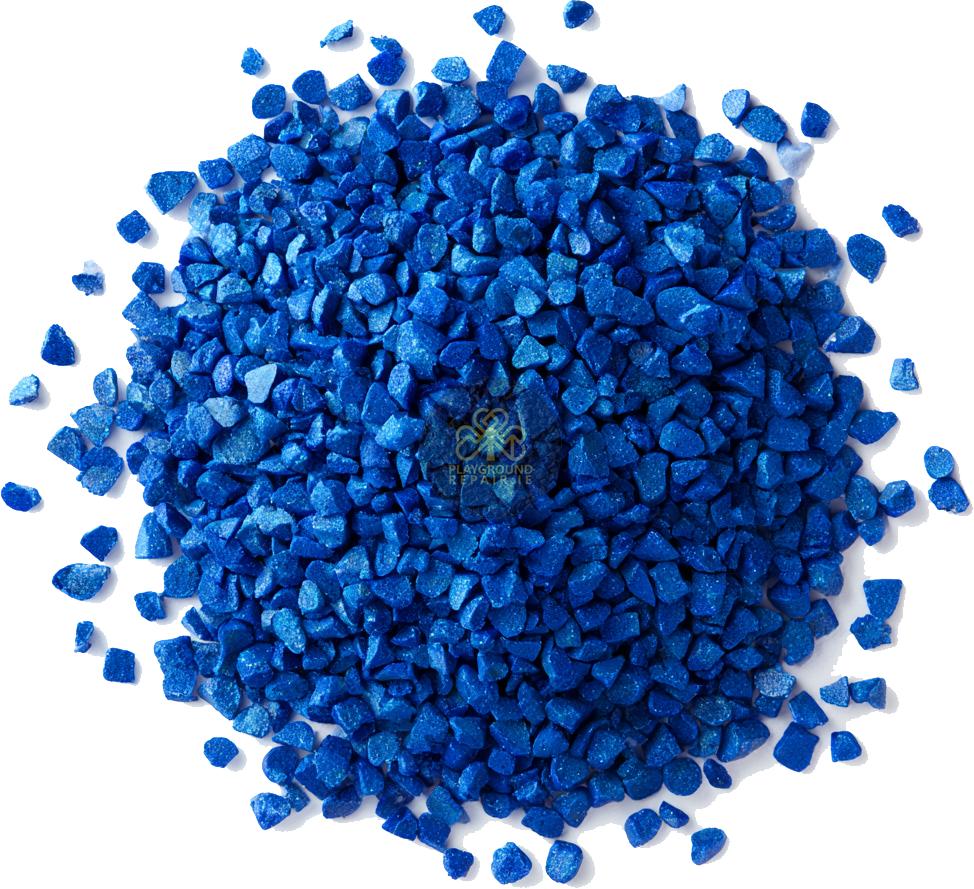
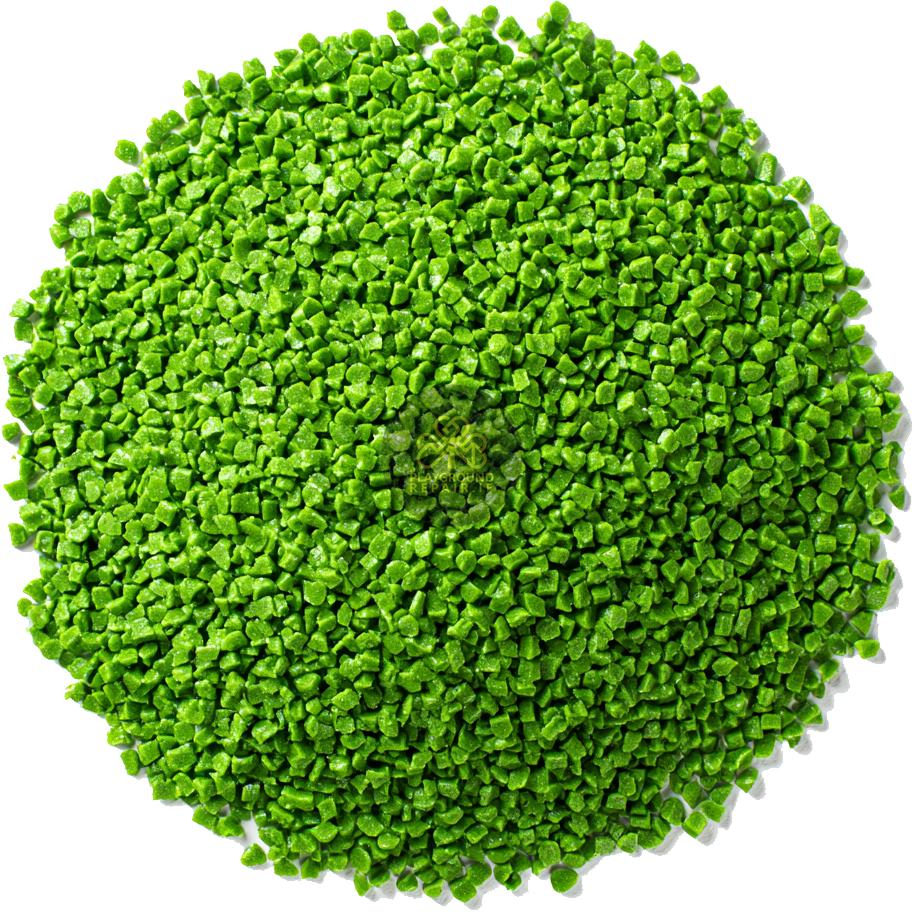
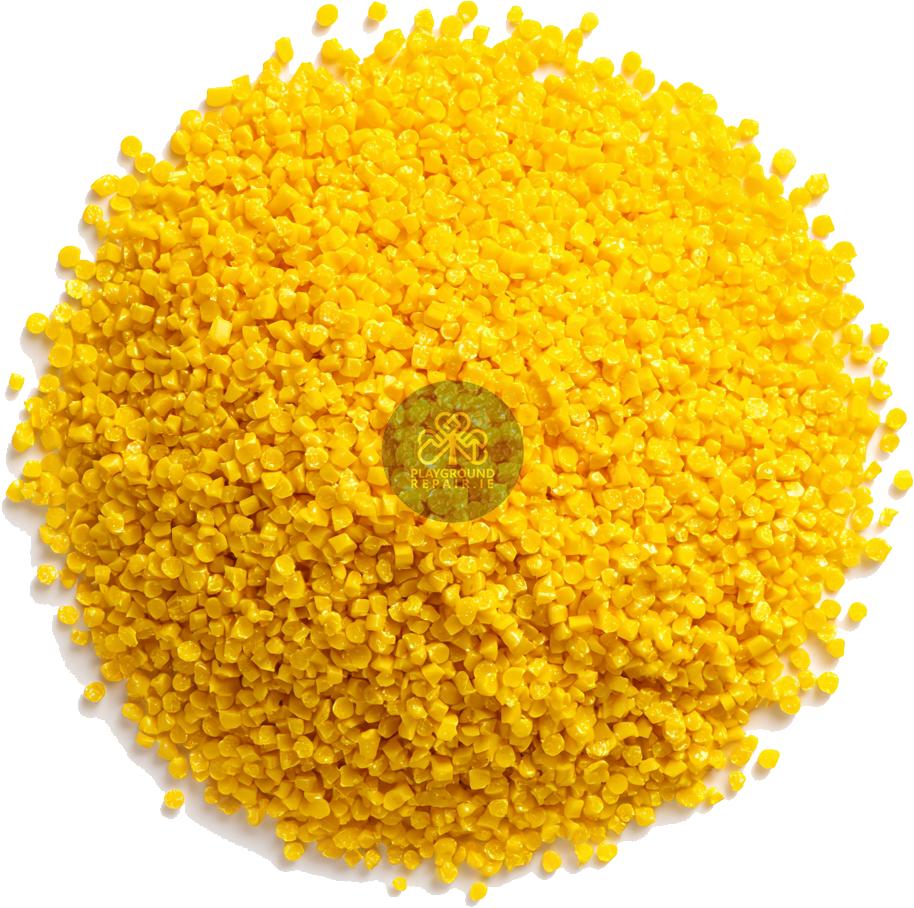
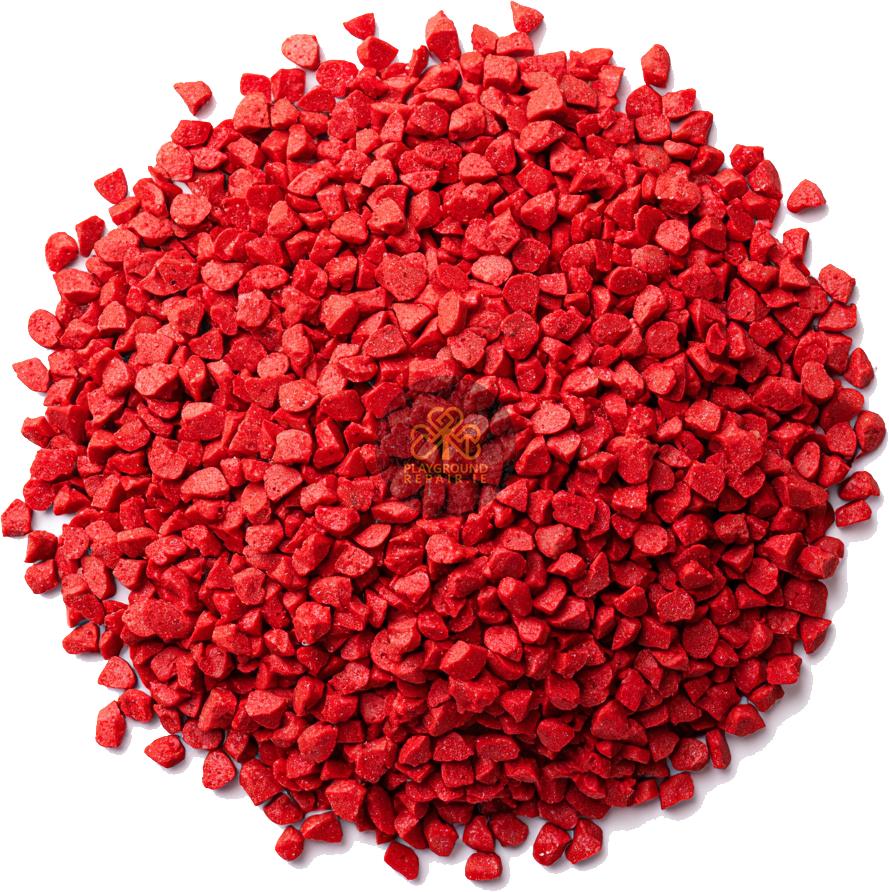
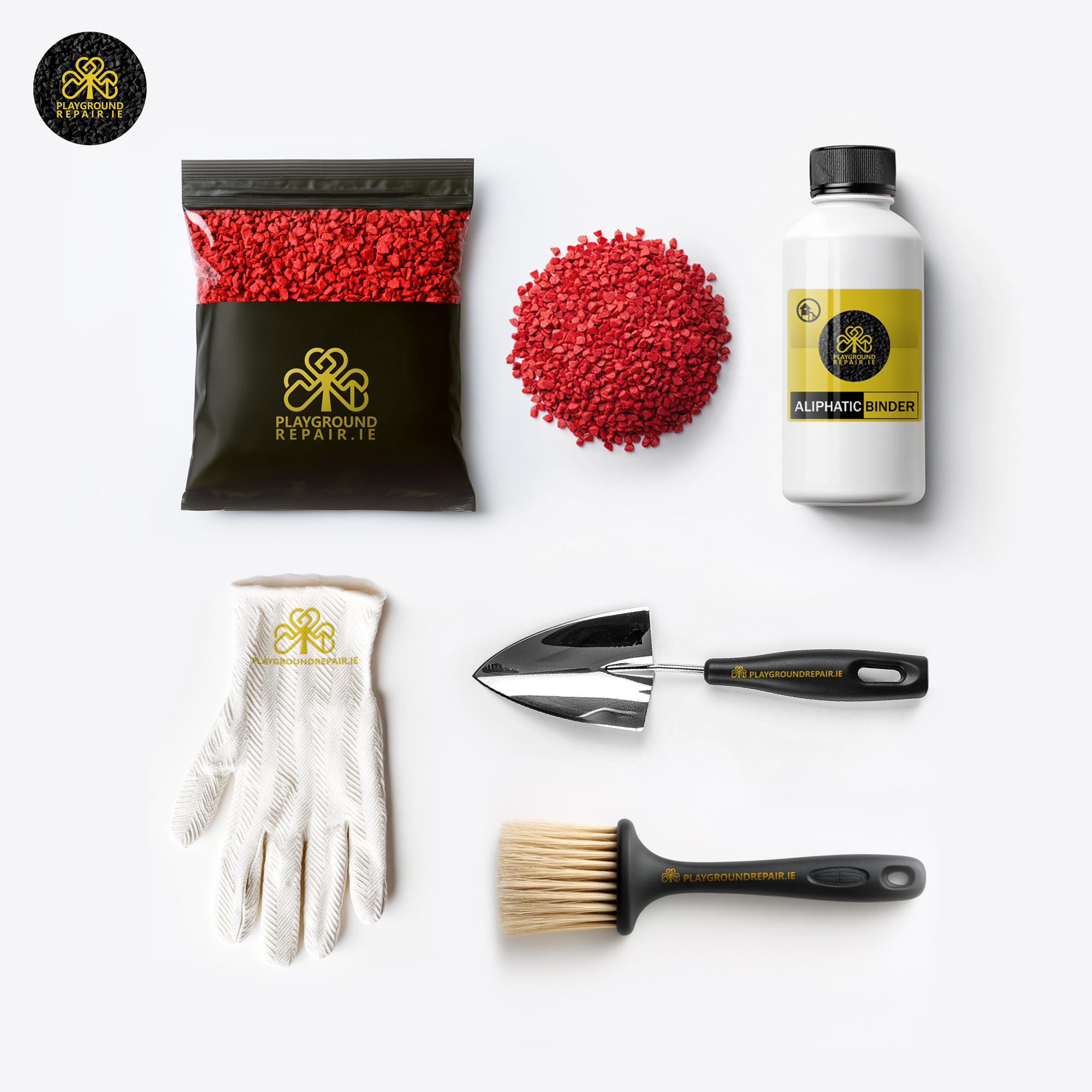
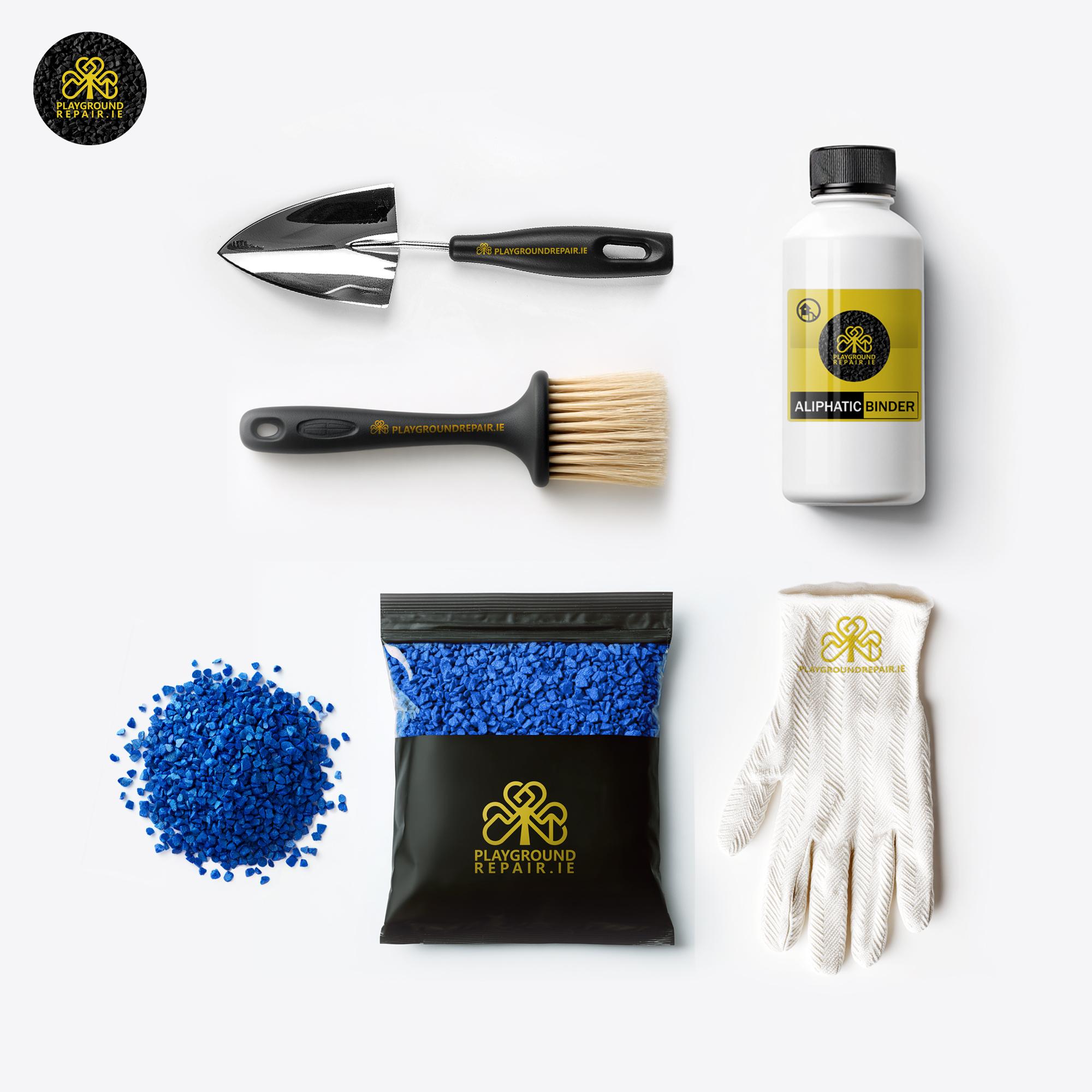
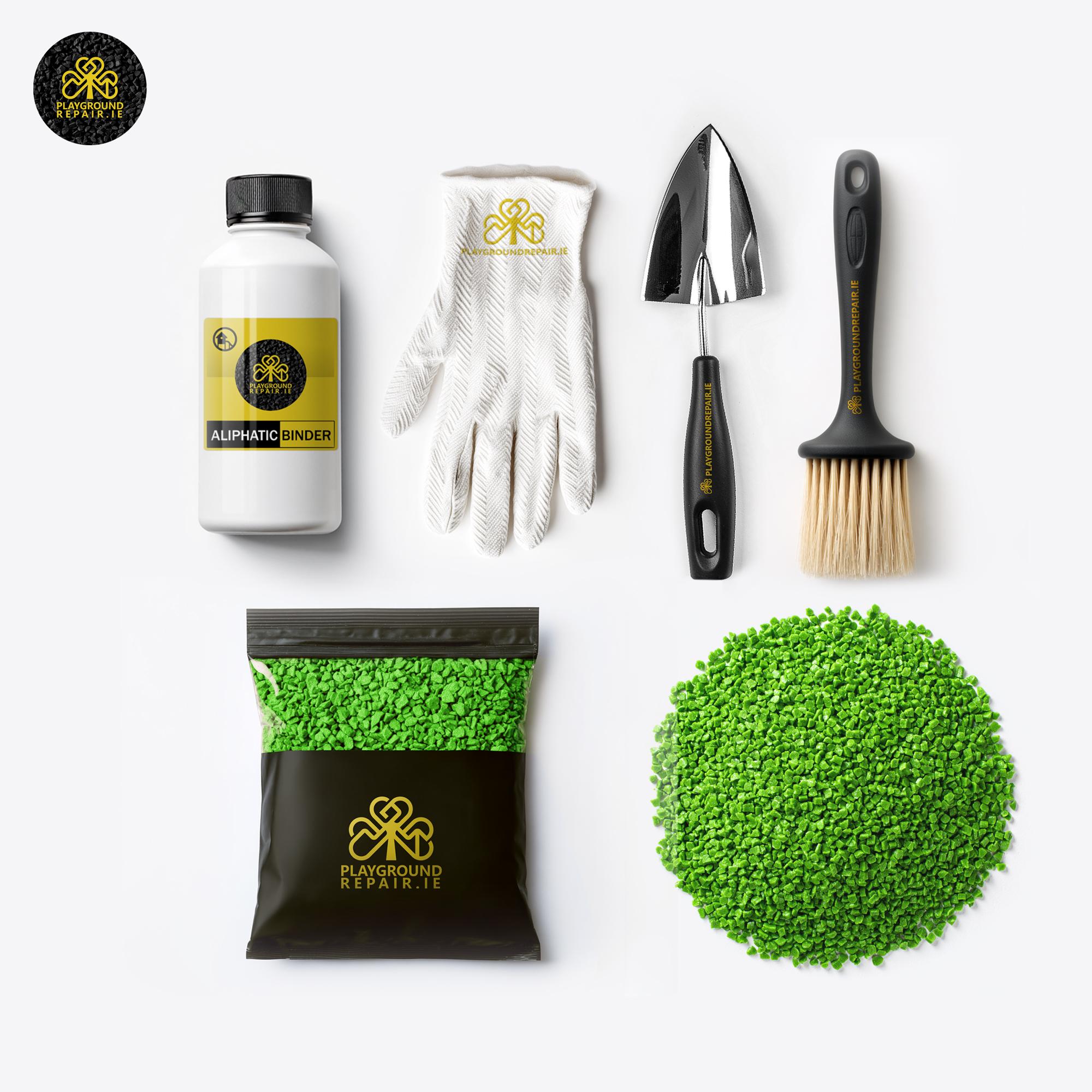
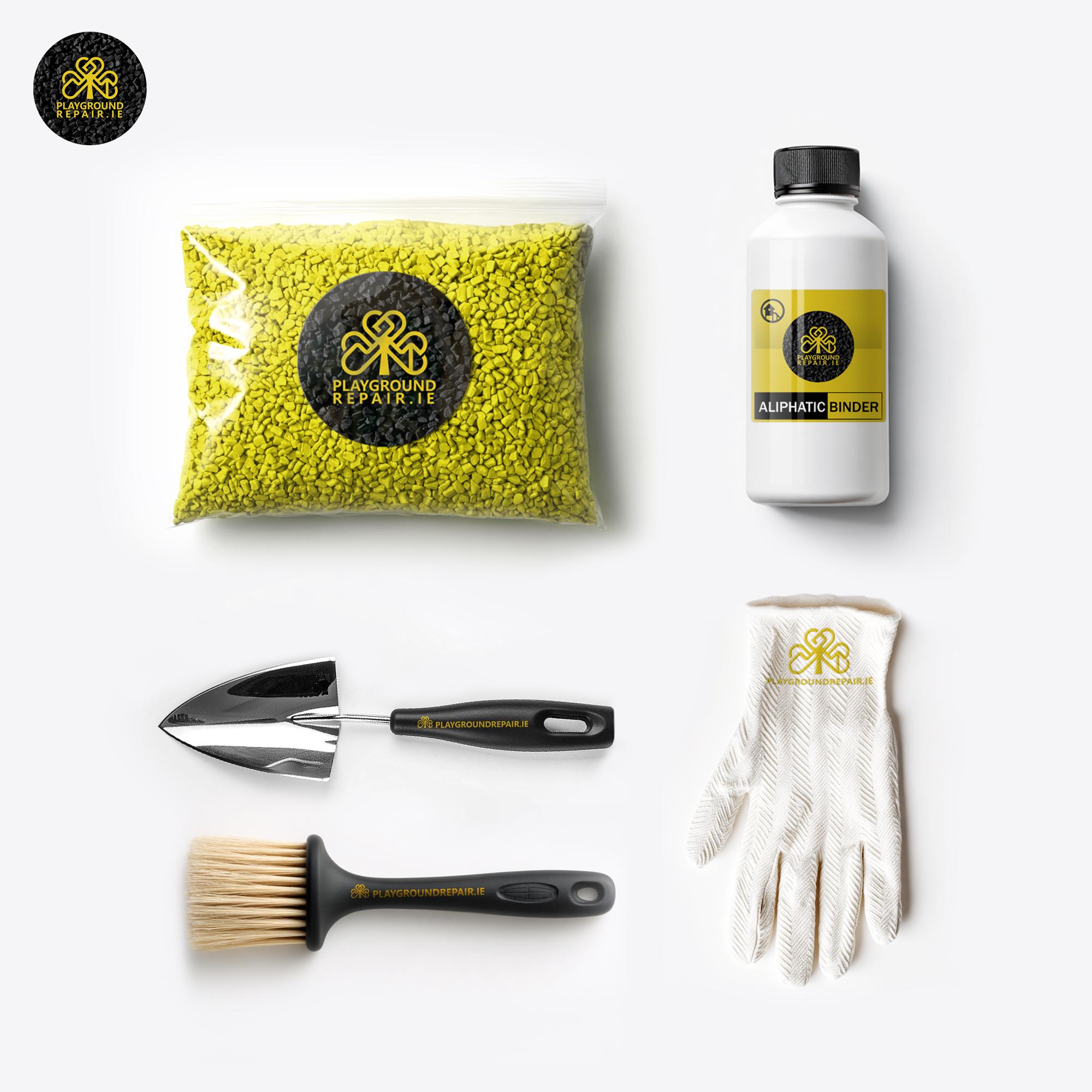
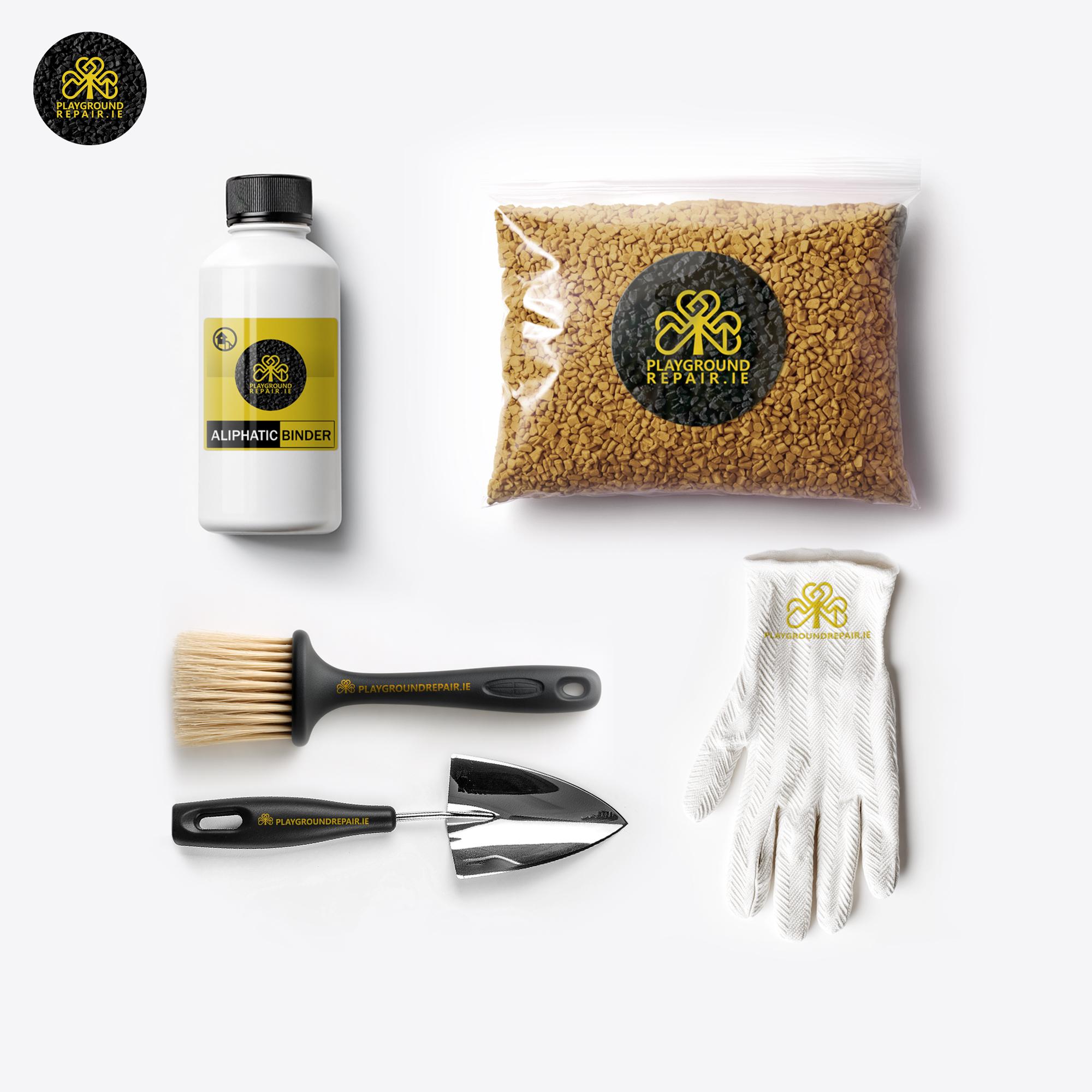
Introduction to Poured-In-Place Rubber (Wetpour) Surfaces
Poured-in-place rubber surfaces are a type of safety surfacing technology that enhances both safety and functionality across various recreational environments, including parks, schools, and sports facilities. The historical timeline of poured-in-place rubber surfacing began in Europe circa 1950, as the Firestone Tire and Rubber Company and the Goodyear Tire & Rubber Company led the pioneering efforts in the development of rubber powder and pelletized rubber specifically engineered for playground applications . This foundational innovation laid the groundwork for the modern wetpour surfaces we utilize today. By the late 1980s, the concept expanded to the United States, marking a transformative moment in the realm of playground safety surfacing. the rubber paving concept further extended its influence to Western Canada in the early 1990s, thereby underscoring the gradual acceptance and integration of wetpour surfaces into the design of play areas, reflecting a significant shift towards safer and more durable environments .
Globally, the adoption rate of wetpour surfaces has surged, with documented installations spanning 16 countries since 2012, according to recent data (RTC Safety Surfaces, 2023). This widespread deployment highlights the growing recognition of the myriad benefits these surfaces provide across diverse settings, including public parks, educational institutions, and sports facilities. The seamless design of wetpour surfaces effectively eliminates trip hazards, consequently cultivating safer and more enjoyable play experiences for children across diverse play environments (Fairmont Industries, 2023).
In both playgrounds and sports facilities, wetpour surfaces offer dual functionality, ensuring safety while optimizing performance. The shock-absorbing capabilities of the material provide a cushioned landing for children, making it particularly suitable for play areas where falls are likely to occur. Recent studies indicate that a mere 4.5 inches of poured rubber can deliver a safe landing surface for falls from heights of up to 10 feet . Wetpour surfaces consistently comply with or exceed numerous safety standards, positioning them as the preferred choice for playgrounds and recreational spaces around the globe.
A paramount aspect of wetpour surfaces is their environmental sustainability. The vast majority of wetpour surfaces are constructed from recycled materials, primarily utilizing Styrene Butadiene Rubber (SBR) rubber crumb, which can constitute up to 100% of the base layer (The Rubber Company, 2023). This eco-friendly characteristic not only contributes to waste reduction but also aligns with the growing global concern regarding environmental impact. The utilization of recycled materials reinforces the commitment to sustainability while simultaneously offering a high-performance product that does not compromise on safety or durability (The Rubber Company, 2023).
Regarding installation, wetpour surfaces are comparatively quick to set up when juxtaposed with traditional surfacing options. The seamless application process facilitates efficient installation in diverse shapes and sizes, accommodating specific playground designs and layouts. Once installed, wetpour surfaces generally require minimal maintenance, rendering them a cost-effective choice in the long term. Regular upkeep is recommended every six months to ensure optimal safety and performance, a manageable frequency in contrast to the maintenance demands of traditional surfaces, which often necessitate annual topping up or replacement (Playground Surfacing, 2023).
In terms of economic feasibility, current estimates suggest that the average installation cost for wetpour surfaces ranges from £29 to £39 per square meter, excluding base works. This pricing accurately reflects the utilization of high-quality materials and advanced installation techniques, meticulously employed to construct a safe and durable surface for recreational applications (Soft Surfaces, 2023). the projected growth rate for the wetpour surfacing market predicts a strong demand for these surfaces over the next decade, with an expected compound annual growth rate (CAGR) of 6.4% by the year 2033 (Business Research Insights, 2023). This burgeoning growth is propelled by the increasing emphasis on safety within playground design, alongside broader trends in environmental sustainability and community well-being.
poured-in-place rubber surfaces possess a rich historical background and a promising future, seamlessly combining safety, durability, and environmental responsibility. As we delve into the intricate composition and properties of these surfaces, it becomes clear that understanding the science behind materials like EPDM granules will further illuminate their performance capabilities and technological advancements. This exploration will unveil the essential components that contribute to the remarkable characteristics of wetpour systems, ensuring that children everywhere have access to safe and engaging play environments.
What Are Wetpour (Soft Tarmac) Surfaces?
Wetpour (soft tarmac) surfaces are a type of safety surfacing solution designed for playgrounds and recreational areas. Celebrated for their durability, slip resistance, and ability to absorb impact, these surfaces have become a preferred choice for various outdoor applications, including playgrounds, parks, and recreational areas. Building upon the essential safety features discussed previously, wetpour surfaces are composed of a specialized mixture of rubber granules, primarily derived from Ethylene Propylene Diene Monomer (EPDM), which are bound together with a polyurethane binder. This unique combination yields a seamless rubber surface that is versatile and effective in enhancing safety.
Characteristically, wetpour surfaces integrate robust EPDM rubber granules with a polyurethane binder, forming a non-slip top layer known as the wearing course. This wearing course is meticulously engineered for high tensile strength, allowing it to endure heavy foot traffic while maintaining integrity over prolonged use. The impact-absorbing properties of wetpour significantly aid in minimizing injuries from falls, a paramount consideration in playgrounds, ensuring a safer environment for children.
Thickness specifications for wetpour surfaces are tailored based on the intended application, ensuring compliance with safety standards for various fall heights. For instance:
- A thickness of 50mm is typically utilized for falls from heights between 4 to 5 feet.
- A thickness of 100mm or greater may be necessary for falls exceeding 10 feet.
This adaptability allows for customized solutions that align with specific safety standards established by organizations such as the Royal Society for the Prevention of Accidents (RoSPA).
the longevity of wetpour surfaces, which can reach 10 to 15 years with proper maintenance, is a critical factor influencing their selection for safety surfacing. Factors such as installation quality, maintenance frequency, and material selection play a significant role in determining the lifespan of these surfaces. Regular inspections and maintenance routines are crucial for prolonging the functional life of wetpour installations, ensuring they remain safe for public use over time.
Wetpour surfaces excel in sound insulation, which is advantageous for urban landscapes where noise reduction is critical. The rubber granules compress under pressure, dissipating impact forces and absorbing sound, thereby creating a more serene environment for both children and nearby residents. In addition to their acoustic benefits, wetpour surfaces also demonstrate remarkable resistance to extreme weather conditions. The inclusion of a polyurethane binder safeguards these surfaces from UV radiation, which can lead to discoloration and surface degradation. This resistance, combined with their slip-resistant qualities, positions wetpour as an optimal choice for diverse climatic environments.
Turning to the practical aspects of wetpour application, it is crucial to understand the installation process. Installation techniques necessitate precision, beginning with the thorough preparation of the existing surface to receive the material. This involves ensuring appropriate drainage, accurately mixing the granules with the binder in predetermined ratios, and applying the mixture uniformly using trowels or specialized equipment. A curing period of at least 24 hours is essential before the surface can be utilized, ensuring optimal adhesion and performance.
wetpour surfaces are distinguished by their innovative installation techniques, material composition, and performance characteristics, establishing them as a comprehensive solution for playground safety. As we transition into discussing the material science behind these surfaces, understanding the properties of the EPDM granules used in their construction will reveal critical insights into their performance, durability, and the technology that supports the safety of play environments. At Playground Repair Ltd, we utilize over 25 years of expertise to deliver high-quality wetpour installations, maintenance, and repairs throughout Ireland. Our unwavering commitment to safety and quality is evidenced by numerous certifications and accolades, affirming our role as a trusted provider in creating secure play environments for children.
Material Science of Wetpour Surfacing
Material science of wetpour surfacing is pivotal to understanding its performance, functionality, and applicability in diverse outdoor environments. Wetpour surfaces represent a sophisticated blend of rubber granules and a polyurethane binder, engineered to provide a durable, safe, and aesthetically pleasing surface for playgrounds, sports facilities, and recreational areas.
The primary scientific principles governing the material performance of wetpour surfaces stem from the interactions between its constituent materials, rubber granules and polyurethane binder. According to the Royal Society for the Prevention of Accidents (RoSPA), a 'wet pour' surface is a blended mix of rubber granules that are bound together. This mixture is manufactured on-site and laid on a suitable existing substrate . The rubber granules, often derived from recycled tires, highlight a sustainable approach while providing distinctive mechanical properties. Maximizing wetpour performance relies heavily on the particle size distribution of EPDM granules, as the cohesive forces inherent in this blend significantly affect the performance characteristics of the surface.
Research published in Materials indicates that smaller particle sizes enhance tensile properties, illustrating that finer distributions produce a more uniform surface texture. This improvement not only reduces trip hazards but also enhances aesthetic appeal . the density and bulk density of these EPDM rubber granules significantly influence the performance of the wetpour system, impacting cushioning properties and surface longevity.
In addition to composition, the mechanical properties of wetpour surfaces play a crucial role in ensuring safety. The outstanding impact-absorbing qualities of wetpour create a cushioned surface that significantly diminishes the risk of injury from falls, establishing it as an ideal surfacing option for children's playgrounds, where compliance with safety standards is crucial. The tensile strength of cured wetpour surfaces is particularly notable, often exceeding 1.2 N/mm², indicating the material's robust durability and resistance to wear under various environmental stresses .
Building upon the understanding of the composition, it is essential to explore how environmental factors affect these materials. Temperature fluctuations can greatly affect the material properties of wetpour surfacing. As temperatures fluctuate, the wetpour rubber material may contract, potentially creating gaps between the surfacing and adjacent structures. The comparatively low tensile strength of wetpour surfaces may hinder their recovery as temperatures rise, potentially resulting in further deterioration . This observation underscores the necessity of considering local climate conditions throughout both the installation and maintenance phases.
The viscosity of the polyurethane binder significantly influences wetpour performance. A low-viscosity binder promotes a quicker curing speed, ensuring a robust bond between the rubber granules and the binder. This rapid curing is crucial for outdoor applications, as it allows for a quicker return to service post-installation, effectively minimizing downtime. Polyurethane binder resins play a vital role in developing stable, non-slip, and impact-absorbent surfaces necessary for maintaining safety and durability in diverse outdoor environments .
Comparative studies of EPDM versus other rubber materials, including natural rubber and thermoplastic olefins (TPO), highlight EPDM's exceptional performance in high-temperature applications. EPDM withstands temperatures up to 350 degrees Fahrenheit, rendering it suitable for various climates . incorporating fillers into wetpour materials can significantly improve mechanical properties, such as strength, durability, and elasticity. Research suggests that incorporating fillers enhances both flexural strength and resilience, leading to an extended lifespan and improved performance under diverse conditions .
Moisture content during installation represents another crucial factor affecting the ultimate properties of wetpour surfaces. Elevated moisture levels can cause cumulative damage over time, whereas insufficient moisture may impede proper surface wetting, thereby affecting the quality and performance of the final product. Maintaining optimal humidity levels during the curing process is essential for preserving the integrity and durability of the wetpour surface .
Finally, several methodologies are utilized to assess the resilience of wetpour surfaces against impacts, including the ST Impact Analyzer and the Head Injury Criterion (HIC) value determination. These testing methodologies generate essential data regarding the impact-attenuating properties of the surface, ensuring adherence to safety regulations and standards .
grasping the material science of wetpour surfacing uncovers its multifaceted nature, governed by the interactions among rubber granules, polyurethane binders, and environmental factors. By applying this knowledge, one can improve the design, application, and maintenance of wetpour surfaces, thereby ensuring safety, durability, and aesthetic appeal in outdoor recreational settings. As we delve further into the specific characteristics of EPDM granules, we will uncover how their unique composition contributes to the effectiveness and reliability of these surfaces, providing a deeper understanding necessary for optimizing their use in various applications. At Playground Repair Ltd, we are dedicated to leveraging this scientific understanding to provide top-quality wetpour solutions throughout Ireland.
EPDM Granules - Composition and Properties
EPDM granules are composed of a specific blend of ethylene and propylene polymers, which contribute to their unique properties. The size range of EPDM granules, typically between 0.5 mm and 3.5 mm, plays a crucial role in optimizing functionality for shock absorption and enhancing the aesthetic appeal of the surfaces. Commonly, sizes for running tracks range from 0.5 mm to 1.5 mm, whereas playground flooring typically employs granule sizes from 1.0 mm to 3.5 mm. This variability allows for tailored applications, ensuring optimal shock absorption and aesthetic appeal depending on the intended use. Custom sizes can also be manufactured to cater to specific project requirements, enhancing both the texture and performance of the final surface . This specific granularity aids in achieving the desired surface texture while simultaneously enhancing the performance characteristics, such as impact resistance and elasticity, of the final laid surface.
The density of EPDM granules varies among different manufacturers, further determining their performance attributes, including durability and shock absorption capability. EPDM granules generally exhibit a density range between 0.85 g/cm³ and 0.95 g/cm³. Higher density granules provide increased robustness and are particularly suited for high-traffic areas, such as sports fields, where durability is paramount . This density variation is a result of differing formulations, such as the ethylene content, which can range from 45% to 75%, impacting the granule's strength and resilience .
In the production of EPDM granules, common additives such as sulfur and accelerators enhance the material's mechanical properties. The addition of sulfur during the curing process creates cross-links between polymer chains, resulting in a product with improved tensile strength and elasticity . the incorporation of performance-enhancing agents, such as antioxidants and UV stabilizers, is essential for prolonging both the lifespan and effectiveness of EPDM granules. These additives significantly enhance the granules' resistance to wear and environmental degradation, making them a reliable choice for various applications.
When assessing the fire resistance of EPDM rubber granules, it is classified as moderate according to ASTM E108 standards, indicating the importance of selecting fire-retardant additives for optimal safety. While EPDM can resist flames to some extent, it is also susceptible to contributing to fire spread if not treated with appropriate fire-retardant additives . Consequently, the selection of enhanced formulations with better fire resistance properties is essential for installations in areas with higher fire risk.
The physical properties of EPDM granules, particularly their high elasticity and compressive strength, significantly enhance the performance and safety of wetpour surfaces. With an ability to withstand temperatures as low as −40 °C and maintain good elasticity, EPDM granules provide optimal shock absorption, crucial for creating a safer play environment . These properties also ensure that the surface does not become overly rigid, which could lead to injury hazards during falls. this elasticity is supported by the granules' compressive strength, which must be sufficient to withstand frequent impacts and pressure without degrading.
Long-term exposure to water can affect the properties of EPDM rubber granules; however, they are specifically engineered to resist moisture, ensuring durability in wet environments. Although prolonged contact can lead to material degradation, particularly when influenced by chlorinated water, which can cause embrittlement , regular maintenance and appropriate installation practices are essential to ensure longevity and performance.
understanding the environmental implications is essential for assessing the sustainability of EPDM granules. Scientific studies indicate that EPDM is a more sustainable option compared to traditional materials. A 2010 Life Cycle Inventory (LCA) study revealed that EPDM performs better than many single-ply and bitumen-based membranes in terms of environmental impact, showcasing its eco-friendly properties . EPDM's durability not only extends the lifespan of installations but also reduces the frequency of replacements, thereby minimizing waste.
The thermal conductivity of EPDM granules, which averages around 0.29 W·m−1·K−1, is relatively low, thereby enhancing their insulating properties and making them suitable for extreme weather applications . the average UV degradation rate of EPDM granules demonstrates their resilience under sunlight exposure. While EPDM does not degrade rapidly in UV light, it is critical for users to recognize that prolonged exposure can lead to color fading and material deterioration. Implementing UV stabilizers during the manufacturing process helps mitigate these effects, ensuring that the surface remains vibrant and functional over time.
Finally, the compressive strength of EPDM granules is vital for the durability and safety of wetpour surfaces. Higher density granules are more capable of withstanding compression and impact, making them ideal for environments such as playgrounds, where safety is a primary concern . The combination of impact absorption, elasticity, and robust physical characteristics ensures that EPDM granules contribute significantly to the effectiveness of wetpour surfacing systems.
the composition and properties of EPDM granules are essential for creating high-quality wetpour surfacing systems that are safe, durable, and environmentally friendly. From size and density to the integration of additives that enhance mechanical properties, each aspect plays a crucial role in determining the performance and longevity of these surfaces in various applications. As we transition into exploring the chemical structure of EPDM rubber granules, we will uncover how these fundamental aspects interact to enhance their performance characteristics, further supporting their role in creating safe and resilient play environments.
Chemical Structure of EPDM Rubber Granules
Chemical structure of EPDM rubber granules is defined by its unique combination of ethylene, propylene, and diene components. To fully grasp the performance characteristics of EPDM rubber granules in wetpour applications, one must first explore their chemical structure. EPDM, which stands for Ethylene Propylene Diene Monomer, is a specialized copolymer that incorporates ethylene, propylene, and a diene component. This tri-component configuration allows for crosslinking through sulfur vulcanization, imparting essential characteristics such as remarkable elasticity, mechanical strength, and superior resistance to various environmental factors.
The mechanical properties of EPDM are greatly influenced by its molecular weight, as higher molecular weight variants exhibit superior tensile strength and enhanced elasticity due to increased chain entanglement and inter-chain interactions. Conversely, lower molecular weight materials often display increased brittleness and reduced tensile strength. Therefore, molecular architecture plays a crucial role in influencing the behavior and application of EPDM rubber.
the ratio of ethylene to propylene in EPDM is vital for affecting its physical properties. A higher ethylene content can enhance crystallinity, leading to improved mechanical strength and thermal stability. This balance is essential for optimizing EPDM's performance under varying conditions, particularly in scenarios involving temperature fluctuations and mechanical stresses.
In addition to molecular weight, the selection of crosslinking agents further influences the performance of EPDM. For instance:
- Sulfur curing typically enhances heat aging resistance while maintaining a favorable balance between flexibility and hardness.
- Peroxide curing improves thermal stability and can yield distinct mechanical traits.
Each curing method alters the chemical structure of EPDM granules, impacting the degree of crosslinking and, consequently, the material's resilience and longevity.
incorporating fillers into EPDM compounds plays a significant role in modifying its chemical behavior. Fillers enhance mechanical properties, such as tensile strength and elongation, by improving dispersion within the rubber matrix and reinforcing the network structure. However, the type and amount of filler utilized can also influence degradation mechanisms; certain fillers may accelerate degradation under specific conditions, such as exposure to ultraviolet light or aggressive chemical solvents.
Despite the inherent chemical stability of EPDM, the material remains susceptible to aging due to prolonged exposure to environmental factors. Common degradation factors include:
- Light
- Heat
- Oxygen
- Harsh chemicals
These factors gradually alter its chemical structure and compromise performance. Understanding these degradation mechanisms is critical for ensuring the longevity and reliability of EPDM applications, especially in outdoor and high-stress environments.
Testing methods used to assess the chemical stability of EPDM granules typically involve evaluating various mechanical properties, including tensile strength, hardness, and compression set under chemical exposure. Universal Testing Machines (UTMs) and hardness testers are commonly employed to quantify these attributes, ensuring that the material retains its integrity over time.
the chemical structure of EPDM rubber granules, characterized by its unique combination of ethylene, propylene, and diene components, along with its crosslinking dynamics and filler integration, determines its performance characteristics and suitability for wetpour surfacing solutions. A comprehensive understanding of these chemical principles is crucial for optimizing the application of EPDM in playgrounds, sports surfaces, and other environments, where durability and safety are paramount.
As we move forward, examining how the unique durability, elasticity, and UV resistance of EPDM contribute to its effectiveness will provide deeper insights into the selection of materials for maximizing the longevity and resilience of wetpour surfaces, ultimately enhancing the safety of play environments.
Durability, Elasticity and UV Resistance of EPDM
Durability, elasticity, and UV resistance of EPDM are critical properties that define its effectiveness in various applications. The exceptional metrics of EPDM's tensile strength and elongation signify its capacity to endure substantial stretching before failure, establishing it as a superior choice for a variety of applications, such as playground surfaces, roofing materials, and sports facilities. A deeper exploration of these properties will illuminate the long-term benefits of utilizing EPDM in environments subject to harsh conditions.
Building upon the understanding of durability, elasticity emerges as another critical property. EPDM rubber exhibits an impressive average ultimate tensile strength of 17.0 MPa (approximately 2470 psi) and an elongation at break of 600%. Research conducted by MatWeb in 2023 shows significant variability in the tensile strength of EPDM formulations, with certain types exceeding 20.3 MPa (around 2940 psi) depending on the specific formulation employed. The inherent high durability of EPDM empowers it to withstand heavy foot traffic, extreme temperature variations, and prolonged exposure to various environmental factors, making it a reliable material for outdoor applications.
In tandem with its elasticity, the UV resistance of EPDM significantly enhances its utility in outdoor environments. This outstanding performance characteristic is rooted in EPDM's unique material properties. It is essential to emphasize that EPDM is among the most elastic rubber materials available today, capable of being stretched up to 300% of its original length and reverting to its initial shape once the stress is alleviated. Such exceptional elasticity renders EPDM highly effective for applications requiring flexibility, including seals and gaskets. Comparatively, EPDM outperforms many other materials, especially in low-temperature environments, where it retains its flexibility superiorly compared to natural rubber, as documented by RubberCal in their 2023 findings. This capacity improves the functionality and prolongs the lifespan of products manufactured from it.
The enhanced stability resulting from peroxide curing enables EPDM materials to maintain their physical properties over extended periods under sunlight and harsh environmental conditions. EPDM's inherent resistance to the degrading effects of UV radiation is a pivotal factor contributing to its widespread adoption, particularly in outdoor applications. Research shows that while EPDM maintains its durability and elasticity under UV exposure, prolonged exposure can result in degradation over time. For instance, a study published in MDPI in 2022 demonstrated that after 800 hours of UV radiation, there could be up to a 30% reduction in tensile strength if the material lacks UV absorbers. However, premium formulations of EPDM that integrate UV stabilizers can significantly mitigate these effects and enhance longevity, resulting in a lifespan of 25 to 40 years when properly maintained, as noted by RH Roofing in 2023.
Environmental factors significantly influence the longevity of EPDM. Weathering elements such as heat, moisture, and UV radiation can impair surface properties and diminish service life if inadequately managed. For example, degradation due to UV exposure can lead to a decline in elasticity and flexibility over time, as discussed in ScienceDirect's 2023 article. Nevertheless, EPDM upholds its integrity under most outdoor conditions, which is why it is commonly employed for roofing systems and playground surfacing.
Understanding the formulation of EPDM granules is also critical in optimizing durability. High-quality granules are meticulously engineered to enhance physical properties, resulting in improved durability and resistance to wear, as highlighted by Melos in their 2023 research. The formulation significantly influences the performance of EPDM in outdoor applications, ensuring that the final product can withstand the demands of regular use.
the combination of high durability, remarkable elasticity, and robust UV resistance positions EPDM as an ideal material for various applications, particularly in environments exposed to extreme weather and intense sunlight. When properly formulated, cured, and maintained, EPDM can deliver enduring performance that withstands the test of time, making it a judicious investment for both residential and commercial endeavors. With a lifespan exceeding 40 years under optimal conditions, EPDM not only serves as a practical choice but also as a sustainable one, contributing to reduced replacement rates and minimized waste over time.
Recognizing these attributes sets the stage for a deeper understanding of how they integrate with other essential components, such as the polyurethane binder, which plays a crucial role in the performance and durability of wetpour systems. Exploring this relationship will provide further insights into optimizing surfacing solutions for various applications.
Polyurethane Binder - The Glue in Poured Rubber Surfaces
Polyurethane binders are essential components in the creation of wetpour surfaces. Building upon the foundation of wetpour surfaces, it is essential to consider the types of polyurethane binders. Polyurethane binders used in wetpour applications are primarily categorized into two types:
- Aliphatic binders
- Aromatic binders
The aliphatic binder is known for its superior UV stability and weather resistance, making it particularly advantageous for outdoor applications where sunlight and moisture are prevalent. In contrast, the aromatic binder typically offers strong bonding capabilities and durability at a lower cost, although it is more susceptible to yellowing when exposed to ultraviolet (UV) light.
According to research conducted by the National University of Materials and Resources for Engineering and Construction (NumatREC) in 2022, the distinct characteristics of each binder type make them suitable for varying environmental conditions and performance requirements .
As the effectiveness of wetpour surfaces hinges on material interactions, the properties of polyurethane binders must be evaluated. Key properties of polyurethane binders, such as UV stability and curing time, directly affect the adhesion of wetpour surfaces. A comprehensive study by Fairmont Industries in 2023 indicates that polyurethane binders provide excellent adhesion, which is critical for maintaining the integrity of the surface under heavy use and varying weather conditions. Good weathering properties are essential for applications in high-traffic areas, where the surface is subject to constant wear and tear and dynamic loads (Fairmont Industries, 2023).
Curing time is a critical factor in the installation process, influencing both the immediate and long-term performance of wetpour surfaces. The average curing time for polyurethane binders generally ranges from 24 to 48 hours, depending on ambient humidity, temperature, and application thickness. A comprehensive study conducted by Tytan Professional in 2023 highlights that understanding these variables is vital for adjusting curing timelines to optimize bonding performance, thus ensuring the durability of the wetpour surface (Tytan Professional, 2023).
Variations in temperature can profoundly affect the performance of polyurethane binders, influencing their adhesion and structural integrity. Research from Gallagher Corporation in 2023 reveals that the dynamic performance properties of polyurethane degrade significantly at temperatures exceeding 93°C (200°F). However, specially formulated polyurethanes can perform effectively at even higher temperatures, providing versatility and adaptability in diverse environmental conditions (Gallagher Corporation, 2023).
The choice between one-component and two-component polyurethane systems further influences the performance of wetpour applications.
- One-component systems are convenient for small-scale projects as they are pre-mixed and moisture-cured without requiring additional components.
- Two-component systems must be mixed prior to application and are often preferred for larger-scale installations due to their enhanced performance characteristics, including superior chemical resistance and bonding strength .
The specific formulation of polyurethane binders significantly influences the final surface texture of the wetpour system, affecting user safety and experience. Research has demonstrated that variations in the types of isocyanates and polyols used in the binder formulation can considerably alter the properties of the final product, impacting texture and opacity, which directly influences user experience and safety .
A multitude of studies corroborates the effectiveness of polyurethane as a binding agent for rubber surfacing solutions, highlighting its adaptability and performance benefits. For instance, research conducted by Cong et al. in 2023 showed that PU-modified asphalt enhances high-temperature stability, aging resistance, and water loss, confirming its suitability as a reliable adhesive for various applications. Additional studies by Jin et al. (2020) and Sun et al. (2018) further attest to the adaptability of polyurethane binders to different rubber mixtures, reinforcing their utility in creating durable and effective surfacing solutions.
The stipulated mixing ratios for polyurethane binders are crucial in guaranteeing optimal performance of wetpour systems, directly influencing durability and surface integrity. A standard mixing ratio suggests approximately:
- 18% binder for the top EPDM layer
- 10-12% for the SBR base layer
These ratios are pivotal, as they directly affect the strength, longevity, and performance of the final surface. Adhering to these mixing instructions is essential to achieve resilient and long-lasting installations, especially in environments with high foot traffic (Replay Surfacing, 2023).
Under stress, polyurethane binders exhibit remarkable performance characteristics. Studies indicate that polyurethane adhesives demonstrate exceptional resistance to extreme temperatures and humidity conditions, thereby preserving their structural integrity over extended periods compared to traditional adhesives. Their shear strength, while susceptible to temperature fluctuations, often surpasses that of conventional adhesives, making them a preferred choice in applications requiring robust mechanical properties .
Lastly, environmental considerations are increasingly important in today's market, and polyurethane binders can receive various certifications attesting to their safety and sustainability. Certifications, including ISCC PLUS and GREENGUARD, signify a strong commitment to environmental sustainability and safety standards, ensuring compliance with rigorous performance metrics, thereby gaining consumer trust (BASF Polyurethanes, 2023; Carlisle Polyurethane Systems, 2023).
understanding the multifaceted nature of polyurethane binders is essential for anyone involved in the installation and maintenance of wetpour surfaces. Selecting the appropriate binder, guided by properties such as UV stability, adhesion strength, and curing time, can profoundly influence the durability and performance of the final product, ensuring longevity and user satisfaction. Whether you are a contractor, facility manager, or simply a playground enthusiast, knowledge of polyurethane binders will empower you to make informed decisions that enhance the safety and longevity of rubber surfacing solutions.
As we delve deeper into the chemical composition of these binders, we will uncover how their intricate structures contribute to the effectiveness of wetpour systems, ultimately reinforcing the safety and durability of play environments.
Chemical Composition of Polyurethane Binders
Chemical composition of polyurethane binders is primarily based on isocyanates and polyols, alongside modifiers like plasticisers and additives that enhance their mechanical properties. Each of these components plays a crucial role in determining the flexibility, durability, and performance characteristics of the resulting polyurethane binders, thus improving their application in various environments.
Following the establishment of isocyanate roles, the contribution of polyols becomes equally significant. Isocyanates, including di- or polyfunctional varieties, serve as the fundamental reactive agents in synthesizing polyurethanes, forming the essential backbone of the polymer chain. Di- or polyfunctional isocyanates, typically containing two or more , NCO groups, such as Methylene Diphenyl Diisocyanate (MDI), are commonly employed in PU formulations for their superior bonding capabilities. MDI remains one of the most widely utilized isocyanates, prized for its advantageous characteristics, such as high tensile strength and excellent adhesion properties. According to research published in the Multidisciplinary Digital Publishing Institute (MDPI), MDI-based PU achieves a remarkable hydrogen bonding index of 4.10, which is directly linked to its enhanced tensile strength, approximately measured at 23.4 MPa .
Polyols contribute soft segments to the PU structure and are hydroxyl-terminated polymers that react with isocyanates, forming a robust polymer network. High molecular weight polyols with extended alkyl segments are particularly effective in producing flexible or elastic polyurethanes, enhancing the elasticity and softness of the final material. This interplay of isocyanates and polyols establishes the foundational strength of the binder, which is crucial for its effective application in wetpour surfaces. The ratio of soft to hard segments in the final product can be tailored to optimize the balance between flexibility and strength. This correlation between the molecular structure of polyurethane (PU) and its resultant mechanical characteristics is well-documented in research published by the American Chemical Society (ACS Publications, 2023).
In addition, incorporating plasticisers plays a vital role in adjusting the flexibility of PU formulations. These additives enhance the curing process and improve the adhesion properties of the final binder. However, careful selection of plasticisers is crucial, as they can adversely affect the binder's durability against environmental factors such as moisture and ultraviolet (UV) exposure.
The distinction between aliphatic and aromatic polyurethane binders illustrates the versatility of PU compositions. Aliphatic polyurethanes, which utilize aliphatic isocyanates, exhibit superior UV stability and are less prone to yellowing over time. In contrast, aromatic polyurethanes, characterized by aromatic isocyanates with cyclic structures, are typically more cost-effective and are prevalent in diverse applications due to their commendable mechanical properties (Fairmont Industries, 2023).
catalysts, particularly amine catalysts, play a crucial role in the synthesis of PU binders. Tertiary amines such as DABCO facilitate the reactions between isocyanates and polyols, significantly accelerating the curing process . The strategic integration of these catalysts ensures that chemical reactions progress efficiently, leading to optimal performance of the polyurethane binder.
Cross-linking density within PU binders critically influences their mechanical properties. An increased cross-linking density enhances the mechanical strength, elasticity, and durability of the polymer network. Higher cross-linking correlates with improved tensile strength and scratch resistance, thereby rendering the polyurethane more resilient for various applications, as indicated by studies published on ResearchGate (2023).
While understanding the composition is crucial, safety considerations during handling should not be overlooked. The presence of diisocyanates may pose health risks upon exposure; therefore, implementing proper ventilation, utilizing personal protective equipment (PPE), and adhering to established safety regulations is essential to mitigate these risks (Best Materials, 2023). Compliance with regulations such as the Toxic Substances Control Act (TSCA) and Proposition 65 is essential, ensuring that all ingredients are documented and meet safety standards.
the intricate chemical composition of polyurethane binders, encompassing isocyanates, polyols, plasticisers, and catalysts, plays a critical role in shaping the mechanical properties and durability of the final product. A comprehensive understanding of these components and their interactions is essential for optimizing performance in wetpour surfaces, ensuring conformity with safety and functionality standards across various applications.
As we continue to explore the binding mechanisms and initial curing reactions associated with these binders, we will gain deeper insights into the processes that significantly contribute to the effectiveness of wetpour systems, ultimately enhancing their performance and longevity in diverse environments.
Binding Mechanism and Initial Curing Reaction
Binding mechanism and initial curing reaction are essential for understanding the performance of polyurethane (PU) binders in wetpour systems. These processes influence optimal adhesion and durability in applications involving soft tarmac patch systems.
Building on the discussion of chemical interactions, it is crucial to recognize that moisture content plays a pivotal role in dictating the efficiency of the initial curing reaction of polyurethane binders. During the initiation of the curing process, the PU binder, which consists primarily of polyols and isocyanates, undergoes a chemical reaction with moisture present on the substrate surface. This interaction occurs between the isocyanate groups (-NCO) of the PU binder and water, along with active hydrogen species frequently found on diverse surface types. According to a research article published in MDPI (2022), this initial reaction triggers a series of complex chemical transformations, resulting in the formation of urethane linkages that establish a strong bond between the PU binder and the underlying substrate. it is essential to note that significant byproducts of these chemical reactions, such as carbon dioxide, are released, which can directly impact the final performance characteristics of the cured product.
The curing process encompasses several essential steps that are vital for achieving optimal binder performance. Initially, the polyurethane mixture must be stacked for approximately four hours to ensure optimal mixing and reaction of the components prior to compaction, as documented by ResearchGate (2022). After this period, the mixture must undergo curing for a minimum of two days under controlled conditions, ideally at 50% relative humidity and temperatures between 15, 40 °C, before it can be considered ready for use . This timeframe is crucial as it allows the curing reactions to completely finalize, ensuring that the binder achieves the necessary mechanical properties required to withstand the stresses encountered during service.
Further, understanding environmental influences reveals that temperature serves as a critical factor affecting the curing kinetics, directly impacting the effectiveness and speed of polyurethane binder reactions. Increased relative humidity enhances the acceleration of chemical reactions within PU adhesives, leading to a higher crosslinking density and storage modulus, ultimately improving mechanical performance. A study published in ScienceDirect (2021) indicates that while increased humidity generally enhances performance, extended curing times under elevated humidity may not consistently yield improved mechanical properties, highlighting a plateau effect that must be considered when optimizing curing conditions for various environments.
Research indicates that elevated temperatures, especially when coupled with increased humidity, accelerate the curing process of polyurethane binders. For instance, increased temperatures can significantly reduce the time required for effective curing, as reported by OTS Company (2022). In contrast, lower temperatures may prolong curing durations, which requires meticulous planning within project schedules.
Various formulations of polyurethane (PU) binders can also impact the efficiency of the curing reaction. Variations in chemical composition, such as the ratios of polyols to isocyanates, the introduction of catalysts, or the utilization of moisture-cure systems, can result in significant changes in curing kinetics. For instance, the addition of tertiary amines or tin-based catalysts can accelerate the reaction rate, thereby enabling customized curing parameters tailored to specific project requirements .
the physical mixing of components is critical to ensuring consistency in the curing reaction. Homogeneous mixing ensures effective bonding and uniform curing, as inadequate mixing may lead to weak spots or inconsistent mechanical properties in the final product. This requirement for meticulous preparation is highlighted by T.D. Rooke (2022), who underscores the importance of employing proper mixing techniques.
As the curing process advances, the mechanical properties of the polyurethane dynamically evolve. In the initial phase, a rapid increase in strength occurs, which is essential for applications within wetpour systems. Both compressive and flexural strengths enhance as curing time extends, underscoring the necessity of allowing adequate time for the binder to achieve its optimal performance characteristics, as corroborated by ResearchGate (2022).
A thorough understanding of the binding mechanism and initial curing reaction of polyurethane is essential for optimizing the performance of wetpour systems. A multitude of factors, including moisture content, temperature, chemical formulation, and mixing practices, play a significant role in influencing these processes. At Playground Repair Ltd, we are dedicated to following these guidelines to guarantee high-quality, compliant surfaces that align with the stringent safety standards across Ireland. Recognizing these curing intricacies will not only ensure the longevity of the surface but also enhance the effectiveness of the polyurethane binder, leading us seamlessly into a discussion on the interrelationship between EPDM granules and polyurethane, which are crucial for maximizing the performance of wetpour systems.
Combined Structure of EPDM and Polyurethane in Wetpour
The combined structure of EPDM (Ethylene Propylene Diene Monomer) and polyurethane in wetpour surfacing is essential for creating durable and high-performance playground surfaces. This critical interaction forms the foundation for improved durability and safety in playground applications.
EPDM is known for its remarkable elasticity and weather resistance, making it a highly effective component for outdoor surfacing. When blended with a polyurethane binder, this combination transforms into a material that exhibits exceptional durability, effectively withstanding environmental elements such as rain, wind, and foot traffic abrasion. The incorporation of a polyurethane binder enhances adhesive qualities while bolstering the surface's stability and resilience, enabling it to retain its structural integrity under dynamic loads.
According to a 2023 study published by Dr. Alice Thompson at the University of Bristol titled "Synergistic Effects in Rubber Composites," the integration of EPDM and polyurethane significantly enhances performance characteristics like shear resistance and fatigue stability, which are essential for ensuring playground safety. Understanding these synergistic effects is essential as it informs ongoing developments in playground design, ensuring that safety standards are met without compromising environmental integrity.
The bonding efficacy between EPDM granules and polyurethane is critical for developing an impact-absorbing surface, ensuring optimal safety in playground applications. The specified mixing ratios are crucial; typically, the construction of an EPDM layer requires approximately 18% polyurethane binder, while the corresponding base layer made from SBR (Styrene Butadiene Rubber) generally utilizes a binder concentration of around 10-12%. This precise combination orchestrates a seamless structure that excels in shock absorption and offers superior slip resistance, even in wet conditions. The permeable nature of the wetpour surface facilitates effective rainwater drainage, thus preventing puddling and further enhancing user safety.
the average density of the EPDM and polyurethane composite typically hovers around 1.22 g/cm³, which significantly influences the mechanical performance of the surface, contributing to its durability and structural integrity. This density is largely determined by the mixing ratios utilized during production. It's important to recognize that while EPDM granules possess a bulk density of less than 580 g/L, the integration of polyurethane considerably modifies the combined material's physical properties, equipping it to manage dynamic loads and thermal expansions more effectively.
Temperature fluctuations cause EPDM and polyurethane to expand and contract at different rates, which, if unaddressed, may lead to surface warping or buckling. Consequently, implementing proper layering techniques and utilizing expansion joints are vital strategies to mitigate such risks, ensuring that the wetpour surface remains stable and functional across a variety of weather conditions.
The combination of EPDM and polyurethane not only enhances performance but also presents notable environmental benefits. EPDM can be recycled and repurposed, contributing to a reduction in the environmental impact associated with playground surfacing. Polyurethane, recognized for its sustainable attributes, promotes a lower climate impact compared to conventional materials, rendering the combined product an eco-friendly selection. Recent findings from the Environmental Protection Agency (EPA) illustrate that utilizing recycled EPDM alongside polyurethane can reduce the carbon footprint of the material by up to 35% compared to the use of virgin EPDM, underscoring the ecological advantages of this surfacing solution.
the sound insulation properties of the EPDM-polyurethane amalgamation present a considerable advantage, particularly in urban playground settings where noise control is crucial. This innovative combination functions as a highly effective sound-absorbing material, reducing echoes and lowering noise levels, thereby cultivating a serene and enjoyable environment for play. The rubbery texture of the surface enhances comfort while providing essential grip to avert slips and falls.
the combined structure of EPDM and polyurethane in wetpour surfaces markedly enhances their performance by offering superior durability, weather resistance, slip resistance, and sound insulation. The meticulous consideration of mixing ratios, thermal expansion properties, and environmental sustainability emphasizes the effectiveness of this innovative material in constructing safe and enduring playgrounds. Ongoing advancements and research into the interactions of these materials continue to evolve, ensuring that they meet the demands of contemporary playground design and safety regulations. This progressive approach not only delivers functionality but also aligns with environmentally responsible practices that benefit both users and the planet.
As we now shift our focus to the critical aspects of mixing ratios and material integration, understanding how these elements further influence the performance characteristics of cured wetpour surfaces will be paramount for optimizing their application and longevity.
Mixing Ratios and Material Integration
Mixing ratios and material integration are critical to the effectiveness of wetpour repair systems, particularly for EPDM (Ethylene Propylene Diene Monomer) granules and polyurethane binders. Understanding these parameters is critical to achieving optimal performance, durability, and cost-effectiveness of the final surface.
The standard mixing ratios for EPDM granules and polyurethane binders play a vital role in ensuring uniformity and structural integrity in wetpour surfacing. For the base layer, typically comprised of SBR (Styrene-Butadiene Rubber), it is advisable to employ approximately 8-9 kg of rubber granules per square meter for every 10mm thickness, mixed with a polyurethane binder at a concentration of around 10-12%. Conversely, the top layer, constructed with EPDM granules, typically necessitates about 10-12 kg of granules per square meter per 10mm thickness. This layer requires a higher binder content, around 18-20%, to maintain adhesion and durability . The effective integration of these ratios is instrumental in ensuring the resilience and longevity of the surface.
The mixing method profoundly affects the uniformity of the wetpour material. Controlled batching and mixing processes, as utilized in wet pouring, ensure consistent material quality and properties. Variations in mixing techniques can lead to inconsistent hydration and uneven distributions of materials, which can compromise the performance of the final surface . For instance, using mechanical mixers that provide high shear can help achieve uniform strength across the mixture by breaking down agglomerates, ensuring that all rubber granules are coated with binder . This uniformity is critical, since it directly impacts the final tensile strength and impact resistance of the cured surface.
varying the mixing ratios can directly impact the tensile strength of the cured surface. Increasing the amount of polyurethane binder beyond optimal levels can lead to reduced tensile strength due to excess curing agents disrupting the bonding matrix . Thus, it is essential to adhere to recommended mixing ratios to ensure that tensile properties remain within desirable limits while maximizing durability.
To achieve maximum durability in wetpour surfaces, best practices for mixing should be meticulously followed. This includes establishing a neat and organized mixing area, ensuring all surfaces are free from contamination, and utilizing appropriately sized mechanical mixers for optimal mixing performance . The use of high-quality EPDM rubber and polyurethane binders is crucial, given that these materials significantly influence the durability and performance of the surfacing system. For example, using top-grade EPDM granules can lead to superior UV resistance and longevity .
the cost-effectiveness of wetpour surfaces is also influenced by the ratio of EPDM to polyurethane binder. A higher ratio of polyurethane binder is generally associated with a slightly wetter texture, which helps in achieving a better finish and can lead to lower maintenance costs over time. This economic aspect becomes more pronounced when considering larger installations, where cost per square meter tends to diminish due to economies of scale .
Improper mixing ratios can lead to severe consequences for wetpour performance. Inconsistent hydration and weak bonding can result in a lower strength and an inability to control the finish effectively. This can compromise long-term durability, necessitating repairs or complete resurfacing sooner than expected . Therefore, adhering strictly to specified mixing ratios is paramount for ensuring that the wetpour surfaces perform as intended over their expected lifespan.
Lastly, the physical properties of the individual components, such as the EPDM granules and polyurethane binders, are crucial in determining the final properties of the mix. The properties of the resulting mixture reflect those of the individual substances, and both components must retain their physical characteristics to ensure optimal performance. Effective integration of additives, where applicable, further enhances the performance of the wetpour surface. For instance, using compatibilizers like EPDM-g-MAH can improve the interfacial compatibility of the blend, ensuring a more homogeneous material that enhances mechanical properties .
In closing, the careful attention to mixing ratios and material integration not only lays the groundwork for achieving high-quality wetpour surfaces but also sets the stage for evaluating their performance characteristics. As we continue to explore these aspects, we will uncover how the meticulous balance of components directly influences the surface's durability and functionality in practical applications.
Performance Characteristics of Cured Wetpour Surfaces
Performance characteristics of cured wetpour surfaces are essential metrics to evaluate their safety and efficacy in playgrounds and recreational areas. Building upon the established safety protocols, a critical metric for evaluating cured wetpour surfaces is the critical fall height (CFH), which indicates the safe height from which a child can fall without injury. Effective wetpour surfaces significantly diminish impact forces during falls, thereby minimizing the risk of potential injuries. According to the ASTM F1292 standards, wetpour surfaces must demonstrate adequate shock-absorption capabilities to ensure a safe play environment for children. A typical wetpour surface, with a thickness of approximately 4.5 inches, can safely absorb the impact of a fall from heights of up to 10 feet . The importance of CFH emphasizes the need for thorough testing of surface materials to ensure they provide adequate shock absorption, which is paramount in establishing the safety of playground installations.
In addition to impact resistance, flammability testing is crucial for validating the safety profile of wetpour surfaces by ensuring materials resist ignition and do not contribute to fire hazards. Compliance with ASTM E648 standards establishes the critical radiant flux of the surface, thus determining its fire safety measures essential for public installations. The capacity of cured wetpour to resist ignition and to slow the progression of flames is vital, especially in environments frequented by children.
Following the evaluation of safety characteristics, the durability and longevity of cured wetpour surfaces are evidenced by their indentation resistance, which is assessed through standardized testing that simulates the pressure inflicted by equipment and foot traffic. High indentation resistance indicates that the surface can endure wear over time, maintaining its integrity even under heavy usage. This durability is essential for preserving both the aesthetic and functional quality of the surface, preventing issues such as uneven wear and structural degradation.
Abrasive wear testing further evaluates the surface's resilience to physical wear over time, particularly in high-traffic areas or spaces subjected to sports activities. Continuous exposure to simulated foot traffic and environmental conditions allows for a thorough assessment of its longevity. Cured wetpour surfaces consistently outperform traditional surfacing materials like concrete or gravel, which, while stable, lack the necessary cushioning to absorb shocks effectively. In contrast, wetpour surfaces provide a cushioned environment that markedly reduces the risk of injuries, particularly during falls.
To quantify the resilience of cured wetpour surfaces, established standards such as BSEN 1176 and ASTM F1292 are utilized, focusing on impact attenuation and surface friction. These tests are crucial for determining the effectiveness of the surfacing material in practical applications. Results from these tests inform the installation process, enabling tailored thickness adjustments based on the specific fall heights associated with various playground equipment.
When analyzing the hardness of cured wetpour surfaces, it is crucial to strike a balance between hardness and wear resistance. Typically, higher hardness values correlate with improved wear resistance. However, excessively hard surfaces may compromise essential safety features like shock absorption. Cured wetpour surfaces generally showcase hardness values that promote both durability and safety, ensuring they remain functional over their intended lifespan while minimizing injury risks.
Environmental factors also play a significant role in the long-term performance of cured wetpour surfaces. Extreme temperatures, elevated humidity, and prolonged sunlight exposure can lead to degradation and color fading. Understanding these environmental effects is essential for selecting materials that retain performance characteristics over time. Under optimal conditions, the lifespan of wetpour surfaces can exceed 15 years; however, adverse conditions can drastically shorten their longevity . Therefore, evaluating local environmental conditions is critical during the material selection process for installation.
The thickness of the wetpour surface is another influential factor affecting its performance characteristics. Thicker surfaces provide enhanced protection against impacts and are particularly suited for environments with a higher fall risk. For instance, increasing the wetpour thickness can elevate the critical fall height it accommodates, thereby improving safety in play areas, especially those featuring climbing structures.
Temperature variations are also instrumental in shaping the performance of cured wetpour surfaces. In regions with high summer temperatures, prolonged sun exposure can lead to increased heat absorption, resulting in a hot surface. Conversely, colder climates can lead to under-curing, adversely affecting adhesion, hardness, and durability. This variability necessitates careful consideration during installation to ensure optimal performance across seasonal fluctuations.
Common failure modes in cured wetpour surfaces often arise from improper installation techniques or the use of unsuitable binder materials. Deviations from established installation guidelines can result in premature wear, cracking, or surface disintegration. Environmental conditions may exacerbate these issues, leading to significant performance decline over time. Thus, regular maintenance and inspections are vital for identifying and addressing signs of wear or degradation, ultimately prolonging the usable lifespan of the wetpour surface.
User activities, including foot traffic and sports participation, significantly impact the longevity of cured wetpour surfaces. Increased foot traffic can accelerate wear, while sports activities may impose additional stresses that shorten the surface's lifespan. It is crucial to select suitable materials and maintain surfaces appropriately to withstand these challenges, ensuring safety and performance in dynamic environments.
the performance characteristics of cured wetpour surfaces encompass safety, durability, and aesthetic aspects, all of which are assessed through rigorous testing protocols. This understanding not only guides stakeholders in making informed decisions about installation and maintenance but also highlights the importance of continuous monitoring to uphold these standards. As we transition to practical applications and considerations for installation, the insights gleaned will further enhance the effective use of wetpour systems in various environments.
Wetpour Repair Kits (Soft Tarmac Patch Kits)
Wetpour repair kits are specialized products meticulously engineered to restore and maintain wetpour surfaces, predominantly located in playgrounds and recreational areas. These kits are essential for mitigating various types of deterioration, including damage caused by environmental factors, and ensuring safety, which is imperative in high-traffic zones where children frequently engage in play. With a heightened focus on maintaining safe, enjoyable play environments, the demand for these repair kits has been significantly escalating, fueled by both necessity and consumer awareness.
Typically, the average cost ranges from £399.99 to £499.99, evidencing the comprehensive nature of these kits, which encompasses all essential materials for effective repairs across designated areas. According to Playbark.com, the pricing spectrum for wetpour repair packs is well established. localized repairs can be achieved through smaller DIY kits. For example, a rubber wetpour DIY kit that covers 1.5 square meters retails for approximately $38, whereas medium-sized (3 square meters) and large kits (6 square meters) range from $72 to $138, as reported by Springrubber.com.au. This enables users to independently manage smaller repairs, substantially minimizing costs associated with minor damages, thus presenting an economical choice for property owners.
A standard wetpour repair kit is capable of covering an area up to 2 square meters at a depth of 20mm, and, therefore, it is suitable for addressing moderate damage within playground settings. The Rubber Company indicates that installation is performed correctly and maintenance is consistent, significantly influencing durability. For users necessitating extensive coverage, larger kits may be essential, especially in community playgrounds or commercial locations where the wear and tear of surfaces can be more pronounced due to elevated usage levels.
User satisfaction rates are reported as high for wetpour repair kits, indicating that many individuals report successful results in restoring safety along with aesthetic appeal to playground surfaces. Although specific percentage data regarding user satisfaction is not universally published, anecdotal evidence and user testimonials suggest that a considerable majority of consumers find these products effective for their intended applications.
Regarding repair timelines, most wetpour repairs can be completed within a single day. Typically, the repaired area becomes ready for use within 24 hours following application, contingent upon environmental conditions and the severity of the damage being addressed. Sources such as Softsurfaces.co.uk affirm that the expediency of this repair method is advantageous for facilities requiring swift solutions to surface damage.
The lifespan of a repaired wetpour surface can extend from 10 to 15 years when installed and maintained correctly, as it can significantly influence durability. Various factors, including the quality of the initial installation, consistent maintenance practices, and prevailing environmental conditions, significantly influence the longevity of the repaired area. research from NumatREC and DC Flooring indicates that with appropriate upkeep, wetpour surfaces can endure for this substantial period.
acknowledging that specific climatic conditions can influence the efficacy of wetpour repair kits is fundamental for optimal performance. Installation should occur under optimal weather conditions, such as dry days with temperatures exceeding 4°C, since freezing temperatures may cause the rubber surface to harden, adversely impacting adhesion and performance. excessive heat can lead to elevated surface temperatures that could soften the materials, potentially influencing both performance and durability. Notably, a study conducted by S. Pfautsch et al. in 2022 illustrates that black and darker-colored wetpour rubber can reach surface temperatures surpassing 80°C, which can significantly affect usability.
The estimated market growth rate is projected at a CAGR of 7.0% over the next five years, reflecting robust demand as communities increasingly prioritize playground safety and durability. This growth trajectory is further reinforced by the rising emphasis on maintaining safety standards within recreational areas.
wetpour repair kits epitomize a vital resource for ensuring the longevity and safety of recreational spaces. As we delve deeper into their purpose and practical applications, it becomes clear how critical these kits are in crafting a safer environment, not only enhancing playability but also addressing specific concerns that arise in various contexts. This understanding sets the stage for exploring the diverse uses and scenarios where these kits can truly shine, showcasing the breadth of their benefits.
Purpose and Use Cases for Wetpour Repair Kits
Purpose and Use Cases for Wetpour Repair Kits are to ensure safety, longevity, and performance across diverse rubber surfacing applications, such as playgrounds, sports facilities, and outdoor recreational areas in high-traffic environments. Wetpour repair kits are vital for sustaining high-use surfaces, ensuring they remain safe and accessible.
One of the most critical environments benefiting from wetpour repair kits is playgrounds, where safety is non-negotiable. According to the Royal Society for the Prevention of Accidents (RoSPA), approximately 40,000 injuries occur in playgrounds annually, underscoring the importance of employing effective surfacing solutions. Wetpour surfaces, characterized by their seamless design and impact-absorbing properties due to materials like urethane and rubber, significantly mitigate the risk of injury resulting from falls, establishing them as the preferred choice for play areas . These kits not only reinforce safety but also ensure that surfaces remain inviting and accessible across various environments.
Wetpour repair kits also prove advantageous in schools and nurseries, where they help create secure play environments for young children. Wetpour surfacing's durability is crucial for withstanding daily activities like play and sports, making it an ideal choice for schools and parks. Its low maintenance requirements further enhance suitability for educational environments, allowing institutions to allocate resources primarily toward educational activities rather than extensive ground upkeep (Soft Surfaces, 2023).
wetpour repair kits are often utilized in public parks and recreational areas to maintain safety and accessibility for all users. These spaces benefit from the slip-resistant and weather-resistant characteristics of wetpour materials, which maintain their performance under various weather conditions. Wetpour surfaces cure rapidly upon mixing, which proves advantageous in public settings where maintaining accessibility is crucial. The ability of these surfaces to withstand environmental factors without significant degradation makes them an enduring choice for outdoor recreational areas .
The versatility of wetpour repair kits extends beyond conventional playground applications. They are effectively utilized in sports courts, fitness zones, and even around swimming pools, where safety surfaces are pivotal. The anti-slip attributes of wetpour materials guarantee that users can navigate these surfaces safely, especially in wet conditions, thereby significantly reducing the likelihood of accidents (DC Flooring, 2023).
To complement the effectiveness of wetpour repair kits, consistent upkeep is essential. Regular maintenance and prompt repairs are crucial in high-traffic areas to prevent accidents and ensure the longevity of play surfaces. It is advisable that wetpour surfaces in such locations undergo inspections and repairs at least once a year, with additional maintenance, such as deep cleaning, scheduled biannually. In particularly active areas, such as beneath swings or climbing structures, more frequent evaluations should be conducted to address any emerging cracks or wear promptly (Soft Surfaces, 2023). This proactive strategy aids in maintaining safety standards and prolonging the integrity of the surfacing.
Research indicates that wetpour repair kits can effectively reduce playground accidents by as much as 40%, particularly when surfaces are regularly maintained. One notable study documented a marked decline in injury rates following the installation of impact-absorbing surfaces, with falls accounting for the majority of reported injuries. A well-maintained wetpour surface can considerably lower the risk of injury from falls, with some reports indicating reductions in playground injuries by as much as 40% .
In residential contexts, wetpour repair kits provide effective remedies for rectifying damaged areas in backyards or gardens, particularly in zones designated for creating safe play spaces for children. They also represent a cost-effective option for homeowners aiming to enhance safety around play equipment or garden features. The flexibility of DIY repair kits renders them a preferred option for homeowners, enabling swift and efficient execution of necessary updates without professional services, while also ensuring cost-effectiveness (Soft Surfaces, 2023).
Beyond residential applications, the commercial sector also benefits from the advantages of wetpour repair kits. These kits are frequently utilized in locales that cater to families and children, such as amusement parks and family entertainment centers. The emphasis on safety and compliance with regulatory standards in these environments necessitates the use of high-quality surfacing materials that can be maintained effectively. Wetpour surfaces meet these criteria, providing a durable and secure play environment for patrons .
while wetpour repair kits are fundamental in maintaining the safety and functionality of rubber surfaces across various settings, their true potential is unlocked when we explore their key components and how they work together. Understanding the individual elements that make up these kits will further illuminate their effectiveness and the science behind their performance, leading us to the next critical discussion on the essential features that contribute to successful repair solutions.
Key Components of a Wetpour Repair Kit
Key components of a Wetpour Repair Kit are essential elements that facilitate the effective maintenance and restoration of rubber safety surfaces. Building on the understanding of Wetpour Repair Kits, the key components play a pivotal role in the repair process. Key components of a Wetpour Repair Kit are crucial for effectively maintaining and restoring rubber safety surfaces, particularly in high-use environments such as playgrounds and athletic fields. A comprehensive knowledge of these components is essential for achieving successful repairs, as each element significantly influences the performance and durability of the restored surface.
A standard Wetpour Repair Kit typically weighs 30 kilograms, consisting of: - 5 kilograms of resin binder - 25 kilograms of black 1-4mm recycled EPDM (ethylene propylene diene monomer) rubber crumb
This specific weight distribution is strategically formulated to deliver the essential materials needed for effective repairs, while also ensuring ease of handling during application. As reported by Rubber Flooring UK (2023), the composition of these kits not only guarantees sufficient material for repairs but also promotes a smooth application process, which is critical for achieving durable and long-lasting results. Understanding how each component works cohesively can significantly influence the effectiveness of repairs and the safety of play surfaces.
The components of a Wetpour Repair Kit can be classified into two primary categories: rubber granules and the binder. Specifically, the EPDM granules are essential components of the kit, offering elasticity, durability, and aesthetic color variety to the surface. In a standard Wetpour Repair Kit, the EPDM granules constitute approximately 83.33% of the total kit weight, equating to 25 kilograms out of the total 30 kilograms. This high percentage underscores the critical role of EPDM granules in providing the necessary properties for developing a resilient surface. Typically, these kits include approximately ten standard colors of EPDM granules, enabling aesthetic variety and customization for playgrounds and recreational areas. For instance, the availability of standard colors significantly enhances the visual appeal of play areas, thereby making them more engaging and inviting for children.
Along with rubber granules, the polyurethane binder is another essential component that contributes to the performance. The polyurethane binder acts as the adhesive agent binding the rubber granules together. The optimal mixing ratio of polyurethane binder to EPDM granules is vital for performance, typically ranging from 18% to 20%. This mixing ratio ensures that the resulting mixture remains slightly wetter than the underlying base layer, thereby facilitating enhanced adhesion when the top layer is directly applied. A 2023 study conducted by Replay Surfacing highlights that achieving the correct binder ratio significantly enhances the durability and performance of the mixture, resulting in a robust finished surface.
In evaluating the contributions of these components to the performance of the patch, both rubber granules and the binder function synergistically. The rubber granules significantly enhance the surface's elasticity and durability, while the polyurethane binder ensures a strong and reliable bond among the granules. This combination results in a robust and resilient surface capable of withstanding the demands of physical play and various environmental stressors.
Industry standards specify that the maximum granule size in Wetpour Repair Kits should not exceed 4mm, ensuring both safety and efficacy. This size range is crucial for ensuring both the safety and efficacy of the surface. Smaller granules facilitate better compaction and create a smoother finish, whereas larger granules enhance the durability of the surface. According to a report by Soft Surfaces (2023), utilizing granules within this specified range guarantees optimal performance characteristics for the completed surface.
Regarding packaging and logistics, Wetpour Repair Kits are generally supplied in standardized containers designed to facilitate easy mixing, transportation, and application. Typically, the kit includes: 1. A mixing and transportation bin 2. Latex gloves for hand protection 3. Comprehensive instructions for effectively mixing and applying the materials
Ultimately, comprehending the key components of a Wetpour Repair Kit is essential for anyone engaged in playground maintenance and safety surfacing. Designed with specialization, these kits not only restore surfaces to their original condition but also significantly enhance the safety and enjoyment of playgrounds and recreational areas for both children and communities. By employing high-quality materials and adhering to industry standards, including those set forth by the National Standards Authority of Ireland (NSAI), these kits guarantee long-lasting performance and compliance with safety regulations. This sets the groundwork for understanding the specific materials used, such as EPDM granules and polyurethane binders, that contribute to the effectiveness of these kits in various applications.
EPDM Granule Component (Pre-Measured Coloured Granules)
EPDM granule component is a crucial part of wetpour repair kits, designed as pre-measured colored granules that enhance the performance and aesthetics of these surfaces. As we delve deeper into the components of wetpour repair kits, it becomes evident that EPDM granules are vital to both the aesthetics and functionality of these surfaces. The EPDM (Ethylene Propylene Diene Monomer) granule component, specifically designed as pre-measured colored granules, serves as a fundamental part of wetpour repair kits to enhance performance and aesthetics.
The typical size range for EPDM granules used in these kits is critical for achieving optimal performance, varying from 0.5mm to 3.0mm. This carefully optimized size range provides flexibility and stability, which are essential for various applications; smaller granules are generally suitable for synthetic grass fields, while larger granules excel in playground surfaces and high-impact areas (NJ Feeling Track, 2023; The Rubber Depot, 2023).
Color variety in EPDM granules is a significant feature, offering extensive customization options, with manufacturers typically providing an impressive selection of up to 24 different colors and blends. This extensive customization capacity allows for meeting specific aesthetic preferences or design requirements (GCL Products, 2023). Beyond aesthetic appeal, the selection of color plays a critical role in functional aspects. For instance, lighter colors significantly mitigate heat absorption, which is crucial when selecting surface materials for outdoor playgrounds or sports facilities in sunny environments (HMS Limited, 2023).
Building on the importance of performance, sustainability is becoming a priority. The production of EPDM granules increasingly incorporates eco-friendly materials in response to rising consumer demand for sustainable options. Many manufacturers are now incorporating recycled materials into their formulations, with some variants containing over 90% sustainable raw materials . Although certain EPDM granules may be composed entirely of virgin materials, the broader industry shift toward eco-friendly options reduces waste and aligns with the values of environmentally conscious consumers.
the physical properties of EPDM granules play a critical role in their application. EPDM granules possess superior elasticity and durability that enable them to maintain performance in diverse environmental conditions without significant degradation . Notably, these granules exhibit exceptional resistance to UV exposure, ozone, and temperature fluctuations, contributing to their longevity. According to studies conducted by the EPDM Roofing Association (2023), these granules can last upwards of 30 years when installed correctly, providing a substantial return on investment for both commercial and residential applications.
An optimal granule density of approximately 1.36 g/cm³ provides the necessary balance of firmness and shock absorption essential for safety in playgrounds . This standardization simplifies the application process and contributes to uniform surface quality and performance across the repaired area.
EPDM granules are 100% recyclable and environmentally safe. They prevent contamination of rainwater runoff, which is particularly vital in urban settings (Rubber4Roofs, 2023). The industry's sustained commitment to minimizing environmental impact and enhancing sustainability continues to influence the production and application of EPDM granules.
the EPDM granule component of wetpour repair kits serves as a versatile and effective solution, offering long-lasting, visually appealing, and environmentally responsible outcomes for a variety of surfacing needs. Its size, color options, focus on sustainability, exceptional physical properties, and advantages in installation contribute to making EPDM granules a superior choice for soft tarmac repair systems. As demand for high-quality playground surfaces and recreational areas rises, the integration of these granules with the binding components not only enhances their utility but also positions them at the forefront of innovations in safety surfacing solutions. This understanding naturally leads us to explore the subsequent essential element that ensures these granules are securely bonded in place: the polyurethane binder.
Polyurethane Binder Component (Resin for Binding Granules)
Polyurethane binder component is essential for binding EPDM granules, creating a robust and durable surface suitable for playgrounds and other recreational areas. Building on the knowledge of key components discussed earlier, understanding the specifications and characteristics of this component is critical for achieving optimal performance and longevity in wetpour systems.
Polyurethane binders are predominantly composed of methylene diphenyl diisocyanate (MDI) based prepolymers, greatly enhancing their adhesive properties. A notable example of an effective polyurethane binder is the PU4223CS, recognized for its relatively low viscosity of approximately 8000 ± 500 mPa·s at 25°C, combined with a rapid curing speed, making it particularly effective for applications in playgrounds and recreational areas, as highlighted by Sabre Adhesives. These binders ensure strong adhesion among the rubber crumb granules that form the surface layer, thereby preserving the structural integrity of the installed surface, especially under varying environmental conditions.
The viscosity of polyurethane binders plays a crucial role in influencing their application effectiveness and performance metrics, impacting factors such as coverage and penetration of granules. Typical polyurethane binders within the aforementioned viscosity range facilitate ease of application, ensuring thorough coverage of granules and allowing better penetration and uniformity across the surface. This characteristic is vital for the long-term efficacy of the repair.
Curing time, averaging 24 to 48 hours depending on environmental conditions, is crucial for determining when the repaired surface can be safely utilized. This timeframe significantly affects project timelines and surface usability, influencing when the area can be accessed and used for recreational activities.
considering the broader environmental context, sustainability in material selection is increasingly prioritized. Manufacturers of polyurethane binders are incorporating up to 70 percent recycled materials into their formulations, which significantly reduces their ecological footprint and promotes responsible manufacturing practices (American Chemistry Council). This shift not only aids in waste reduction but also demonstrates a commitment to sustainable practices without sacrificing performance.
Temperature exhibits a critical influence on the performance of polyurethane binders, with research indicating that their dynamic performance properties degrade significantly when exposed to temperatures exceeding 93°C (200°F) (Gallagher Corporation). Selecting appropriate binders for specific climatic conditions is imperative to maintain their structural integrity and functionality throughout their lifespan.
The tensile strength of cured polyurethane in wetpour applications typically ranges around 12.9 MPa, influenced by specific formulation and curing conditions, which is essential for ensuring the surface withstands physical stresses from foot traffic, play equipment, and environmental factors (MatWeb). This aspect is particularly relevant as higher tensile strength not only ensures durability but also complements the resilience offered by EPDM granules.
The formulation of the polyurethane binder directly influences the longevity and elasticity of the repaired surface. Prolonged exposure to elevated temperatures can lead to increased stiffness in the binder, which may compromise the adhesion of the surface (ScienceDirect). Properly formulated polyurethane binders maintain flexibility and resilience over time, significantly extending the lifespan of the installed wetpour surface and establishing flexibility as a critical parameter in the binder selection process.
Compliance with safety regulations established by the Occupational Safety and Health Administration (OSHA) is paramount when working with polyurethane binders to mitigate risks associated with potential hazards during installation and maintenance. Understanding these regulations is critical for contractors and users, ensuring compliance and safety in all operational procedures.
Finally, the yield of polyurethane binders, defined as the coverage area of approximately one square meter per one liter at a depth of one millimeter, is a crucial aspect for project planning. This yield aids in accurate resource estimation and minimizes waste. Typically, one liter of polyurethane binder can effectively cover an area of approximately one square meter at a depth of one millimeter (IDI Insulation). This information is essential for estimating the quantity required for specific projects, ensuring cost-effective solutions and minimizing waste.
the polyurethane binder component is indispensable for the effective functioning of wetpour repair kits. Its properties, including viscosity, curing time, environmental impact, and adhesion characteristics, significantly influence the performance, durability, and sustainability of the wetpour system. By gaining a thorough understanding of these attributes and adhering to best practices, users can ensure their repair projects yield optimal results, providing safe and enjoyable surfaces for recreational activities. This foundational knowledge not only emphasizes the importance of the binder but also prepares us to examine the next critical step in the process: ensuring seamless bonding with the wetpour sealing solution that enhances the integrity and longevity of the surface.
Wetpour Sealing Solution (Edge Primer) for Seamless Bonding
Wetpour sealing solution (edge primer) is essential for achieving seamless bonding during the installation and repair of wetpour surfaces. This assessment directly correlates with the effectiveness of the wetpour repair kits previously discussed.
Evaluating curing time is crucial; adequate time must be allowed for the edge primer to set before advancing to the principal repair activities. Under optimal conditions, the recommended curing time for the edge primer is a minimum of 24 hours, according to information provided by Quora. However, this duration can vary significantly due to environmental factors, including temperature fluctuations and humidity levels, which affect the curing process. For example, elevated temperatures can accelerate the curing process, whereas cooler conditions may prolong it. It is crucial to consult the manufacturer's specific guidelines to optimize the curing process for your particular situation.
understanding user experiences enhances the assessment of sealing solutions. User feedback highlights an important benefit: approximately 65% of users report enhanced adhesion when employing wetpour sealing solutions, according to Global Growth Insights. This statistic emphasizes the necessity of incorporating edge primers into repair protocols, as improved adhesion results in more durable and resilient surfaces, ultimately reducing maintenance frequency and costs.
the sealing solution plays a pivotal role in reinforcing repair durability. By serving as a barrier against water infiltration and mitigating the effects of environmental stressors, sealing solutions significantly extend the lifespan of the repaired area, as emphasized by A1 Concrete. For instance, the sealing solution functions as a protective shield against weathering agents that have the potential to deteriorate unprotected surfaces. This measure not only enhances the integrity of the installation but also assures facility managers and users regarding safety conditions.
Typical coverage rates for wetpour sealing solutions are vital for effective project planning. The standard coverage from a single bag of sealing solution is approximately 1.7 square meters at a depth of 20mm, as noted by Online Playgrounds. Understanding these coverage rates enables accurate estimation of the material required for specific projects, ensuring that necessary quantities are procured while minimizing excess waste.
Environmental conditions, such as temperature and humidity levels, play a crucial role in the performance of sealing solutions. These sealing solutions deliver optimal results when applied within controlled temperature ranges of 15°C to 25°C, as recommended by SealFluid. Extreme temperatures, whether excessively high or low, can negatively affect adhesion and curing processes, potentially resulting in repair failures. Therefore, it is recommended to monitor weather forecasts and choose application times when conditions are stable.
The compatibility of the sealing solution with various surface types is essential for achieving optimal performance. Polyurethane-based sealing solutions are particularly recognized for their superior adhesion to a variety of substrates, including wood, metal, and concrete, common materials found in playground environments, as highlighted by Metro Sealant. Ensuring compatibility between the sealing solution and the substrates not only ensures effective bonding but also extends longevity, which is crucial for safety surfaces subjected to significant wear and tear.
In terms of shelf life, most wetpour sealing solutions generally have a lifespan of approximately six months, given they are stored under optimal conditions, including a dry environment and moderate temperature, as specified by GCL Products. This shelf life emphasizes the importance of effective inventory management, ensuring that products are utilized within their viable period to prevent inferior repair outcomes.
Finally, it is crucial to follow safety precautions during the application of edge primers. Utilize non-sparking tools and ensure that adequate protective gear, including gloves and goggles, is worn to mitigate health risks linked to chemical exposure, as recommended by Johnson Autobody Supply. Maintaining a well-ventilated work area and adhering to the specific safety data sheets for the sealing solution will further improve safety during the application process.
while the wetpour sealing solution (edge primer) is critical for achieving seamless bonding and enhancing the durability of playground surfaces, it also opens the door to understanding the significance of effective packaging and logistics in ensuring these solutions reach their destinations intact. By considering application rates, curing times, environmental conditions, surface interactions, and safety protocols, you can effectively utilize this component to improve the durability and performance of wetpour surfaces. Maximizing the full potential of the edge primer ensures a safe play environment while adhering to industry standards for surface maintenance and restoration.
Packaging and Logistics of Repair Kits
Packaging and logistics of repair kits are essential components that ensure the safe transport and immediate usability of wetpour repair kits. As highlighted in the previous discussions on user applications, efficient packaging and logistics not only protect the integrity of the repair kits during transport but also ensure that they arrive ready for immediate use. When it comes to wetpour repair kits, packaging and logistics are critical factors that ensure these essential products reach consumers efficiently and intact. The design and dimensions of packaging directly influence both shipping costs and the usability of wetpour repair kits.
The standard dimensions for packaging wetpour repair kits typically include a 100-litre mixing and transportation bin optimized for the secure storage of product components. For instance, a standard kit may contain:
- A 25-kilogram bag of EPDM granulate (1-4mm)
- A 5-kilogram Rubbaflex® polyurethane binder
Together, this combination enables the kit to cover approximately 2m² at a 20mm depth, making it suitable for a variety of applications in playground repairs. the choice of a 100-litre bin facilitates easy mixing and transportation, ensuring that users can efficiently prepare the materials on-site (The Rubber Company, "Wet Pour Repair Kit").
When considering logistics, the number of kits that can fit on a standard shipping pallet is vital to achieving optimal shipping efficiency. Generally, a standard pallet can accommodate around 60 boxes, each measuring 12 inches on all sides. However, this figure can vary depending on the actual dimensions and weight of the individual kits. For instance, a 53-foot truck can typically hold 26 standard pallets, significantly influencing shipping costs (Bishamon, "How Many Pallets Fit on a Truck with Standard Pallet Sizes"). Therefore, understanding the shipping weight is essential for optimizing logistical strategies.
The average shipping weight of a complete wetpour repair kit is around 37 pounds, comprising the EPDM granulate and polyurethane binder. This weight is critical for freight calculations, as weight directly influences shipping costs and the choice of transportation methods (Online Playgrounds, "Complete Wetpour Playground Surfacing Repair Kits"). Companies must account for this weight when determining the most efficient logistics strategies, particularly when shipping internationally.
Cost comparisons for domestic versus international shipping reveal significant differences. Domestic shipping tends to be more cost-effective due to lower logistical complexities and shorter delivery times. Conversely, international shipping typically incurs higher expenses linked to customs duties and additional regulations. Businesses can save costs by strategically choosing their shipping methods based on the destination and package size (CourierDost, "Domestic vs International Courier Services: How CourierDost Provides the Best Options").
the trend towards eco-friendly packaging illustrates a broader commitment to sustainability in the logistics of wetpour repair kits. Innovations in packaging aimed at reducing environmental impact are increasingly critical in the industry. Trends include the use of biodegradable and compostable materials, which help mitigate the environmental burden associated with plastic waste. advancements in packaging design, such as the adoption of lighter materials, significantly reduce both packaging waste and transportation costs. Companies that prioritize eco-friendly practices often gain a competitive edge by appealing to environmentally conscious consumers (Agrinextcon, "10 Groundbreaking Sustainable Packaging Innovations Revealed!").
User-friendliness represents a vital component of effective packaging design. Features such as easy-tear strips and resealable bags enhance usability, allowing customers to access the contents quickly and efficiently. compact packaging is essential for optimizing storage and transport, as it minimizes wasted space and reduces shipping costs (DesignRush, "How Product Packaging Impacts Customer Perception and Sales"). A well-designed package not only improves the customer experience but also reflects the quality and reliability of the product, which is particularly important in a competitive market (Metrobi, "The Role of Packaging Design in Driving More Product Sales").
The common materials used in the packaging of wetpour repair kits typically include durable plastics and cardboard, engineered to endure transport challenges while protecting the contents. These materials must be robust enough to handle moisture exposure during shipping, which is a critical consideration given that approximately 12% of all container shipment damage is moisture-related (Absortech, "The Costs of Moisture Damage"). The packaging must ensure that the components, such as the EPDM granulate and polyurethane binder, remain secure and undamaged throughout their journey to retailers and end users (The Rubber Company, "Wet Pour Repair Kit").
Statistics reveal that approximately 0.5% of gross sales can be lost due to shipping damage, underscoring the importance of effective packaging and logistics strategies. This data highlights the need for companies to invest in high-quality packaging solutions capable of withstanding the rigors of transportation while ensuring product integrity (Contimod, "9+ Shipping Damage Statistics Must Know in 2024").
effective packaging and logistics are pivotal to the success of wetpour repair kits, significantly influencing shipping costs and customer satisfaction. Ultimately, the synergy between effective packaging and logistics not only enhances operational efficiency but also contributes to positive brand perception. By focusing on innovative packaging designs that emphasize user-friendliness and environmental sustainability, companies can enhance the customer experience while reducing logistical challenges. As these kits become more widely utilized, understanding the specifics of component packaging and storage requirements will further ensure the integrity and performance of the repair solutions in varying environments.
Packaging of Components (Buckets, Containers, Tools)
Packaging of components is essential in Wetpour Repair Kits as it ensures functionality, safety, and user convenience. In the realm of Wetpour Repair Kits, packaging components plays a pivotal role in ensuring functionality, safety, and user convenience. The integrity of packaging directly affects the performance of wetpour repair kits, making it essential for manufacturers to carefully consider their packaging strategies.
Typical sizes of containers used for packaging wetpour repair kit components are crucial for enhancing both functionality and user engagement. Most commonly, wetpour repair kits include pre-measured components packaged in 25 kg bags for larger granules, while smaller 5 kg containers are utilized for specific materials, such as color granules. This dual packaging approach enables users to effectively manage material quantities, particularly during small-scale repairs when a full 25 kg is excessive. The Rubber Company emphasizes that these container sizes cater to diverse user needs, ensuring precise repair execution and reducing material waste .
packaging types for various components of wetpour repair kits significantly vary in design and material properties, tailored to meet the unique requirements of components like rubber crumb and polyurethane binder. The wetpour repair kit typically contains essential components such as rubber crumb, binder, and a sealing solution. Each of these components requires distinct packaging solutions to protect their integrity and ensure ease of use. For example, the rubber crumb, which can range in size from 1-4 mm for black granules and 1-3 mm for colored varieties, is usually provided in sturdy, moisture-resistant bags that prevent contamination. On the other hand, the polyurethane binder, which is crucial for bonding the granules, may be packaged in smaller, tamper-evident containers to maintain its efficacy due to its sensitivity to moisture and air exposure. As noted by PlaySmart UK, proper packaging can preserve the effectiveness of these vital components .
understanding the financial implications of packaging choices is essential for manufacturers. Research indicates that packaging can account for between 10-40% of a product's retail price, varying based on material choice and design complexity. For wetpour repair kits, it has been observed that the unit price of individual packaging elements typically represents around 15% of the total cost. This financial consideration is essential for manufacturers as they balance quality packaging with affordability, ultimately impacting retail pricing strategy .
the number of components that can fit in each container without compromising safety during transport is a crucial logistical consideration. A standard 40-foot shipping container is commonly utilized to transport larger bulk orders of wetpour repair kits, safely accommodating three to four pallets without risking damage .
The effectiveness of packaging materials for sensitive components like polyurethane binders diminishes over time, influenced by storage conditions. If exposed to moisture or extreme temperatures, these materials may degrade, leading to compromised product performance. According to SealFluid, understanding the shelf life of packaging materials is crucial for ensuring optimal product efficacy .
In addition to functionality and cost, compliance with industry standards plays a crucial role in packaging. Packaging must deliver clear and accurate product information, including detailed ingredients, usage instructions, and essential safety warnings to ensure consumer understanding. Compliance with regulations such as the Fair Packaging and Labeling Act (FPLA) is essential, ensuring that consumers receive all necessary information in an easy-to-understand format. The Federal Trade Commission highlights the importance of these regulations in promoting transparency in consumer goods .
Packaging design significantly influences consumer purchasing decisions, underscoring its critical role in buyer behavior. An attractive, functional design enhances consumer perceptions of quality and motivates purchasing. Packaging that effectively communicates product features and benefits can significantly influence buyer behavior. Research indicates that consumers often make decisions based on first impressions formed through packaging aesthetics, underscoring the importance of strategic design in product marketing .
Market research shows a growing trend towards eco-friendly packaging materials, aligning with consumer preferences for sustainability. A significant portion of consumers now prioritize environmentally responsible packaging when making purchasing decisions. In fact, studies indicate that nearly 70% of consumers would be willing to pay more for products that come in sustainable packaging . This shift is prompting brands to explore innovative, sustainable packaging solutions that meet safety and regulatory requirements while resonating with modern consumer values.
Challenges in the packaging process for wetpour repair kits include issues like moisture retention and product contamination, which can negatively impact product integrity. Ensuring that packaging is adequately designed to prevent such issues is critical for maintaining product quality and safety throughout the supply chain. Liquid Packaging Solutions emphasizes the importance of addressing these challenges to ensure seamless logistics .
Effective packaging design and material selection are crucial factors in determining the market success of wetpour repair kits, influencing both consumer trust and product efficacy. As the industry evolves, so too must the strategies surrounding packaging, with an increasing emphasis on sustainability, safety, and consumer engagement. This holistic approach not only enhances the product's appeal but also ensures compliance with industry standards while effectively addressing the logistical challenges inherent in the packaging process.
the packaging of wetpour repair kit components is a multifaceted aspect that significantly impacts product quality, consumer perception, and market success. By understanding the dynamics of packaging materials, sizes, and designs, manufacturers can better meet the needs of their customers while navigating the complexities of compliance and sustainability. This insight serves as a foundation for exploring crucial aspects of shelf life and storage requirements, ensuring that these vital products maintain their effectiveness and readiness for use in any situation.
Shelf Life and Storage Requirements
Shelf life and storage requirements are essential for ensuring the effectiveness of wetpour repair kits. Understanding the shelf life of wetpour repair kit components, particularly EPDM granules and polyurethane binders, is vital for ensuring long-term performance and reliability. The average shelf life for these materials typically spans from 5 to 10 years. While EPDM granules and polyurethane binders can retain their properties over an extended period, proper storage is crucial to maintain their effectiveness.
To ensure that EPDM granules and polyurethane binders maintain their effectiveness throughout their entire shelf life, it is crucial to store them in optimal conditions, cool, dry locations shielded from sunlight. Polyurethane binders, which serve as the adhesive that bonds the EPDM granules together, should be kept at temperatures ranging from 15 to 25 °C (60 to 77 °F) to effectively prevent degradation. Exceeding these temperature limits can result in undesirable changes in viscosity and even gelation, rendering the binder ineffective.
Another critical aspect impacting the usability of these materials is humidity, which directly affects the quality of both EPDM granules and polyurethane binders. Increased humidity levels can adversely impact the performance of these components, resulting in detrimental effects such as rubber swelling and loss of hardness. It is advisable to sustain relative humidity levels below 70 percent for all components, with an optimal threshold of less than 65 percent being particularly beneficial for polyurethane components. This regulated environment safeguards against moisture absorption, significantly reducing the risk of undesired chemical reactions and material degradation.
Inadequate storage practices may result in considerable losses, with studies suggesting that approximately 30 percent of products are rendered ineffective due to insufficient handling and storage measures. Users are advised to routinely conduct inventory assessments to evaluate the condition of their repair kits and verify that they remain within their effective shelf life. Routine inventory assessments not only help maintain the effectiveness of wetpour repair kits but also ensure timely repairs are conducted before any degradation occurs. Manufacturers endorse performing these evaluations at a minimum frequency of once annually, especially for high-value materials, to avert wastage and guarantee optimal performance when repairs are needed.
Indicators that a repair kit has exceeded its effective shelf life may encompass visible color changes in the granules or binders, signs of physical disintegration, or marked changes in consistency or viscosity. Upon detecting any of these indicators, it is critical to abstain from using the product and responsibly dispose of it in accordance with local waste management regulations.
In addition, manufacturers strongly recommend adopting a first-expiry, first-out (FEFO) inventory management system to optimize stock rotation. This methodology guarantees that older stock is prioritized for use before newer supplies, thereby reducing the risk of employing expired components. Maintaining comprehensive records of purchase dates and storage conditions for each component is crucial for successful shelf life management.
Understanding the importance of proper packaging and logistics is also key to ensuring these repair kits reach users in optimal condition. As we transition to the next section, the packaging and logistics of wetpour repair kits play a vital role in safeguarding their components during transport and enhancing user accessibility, ensuring that these essential solutions are always ready when needed.
Shipping and Handling Considerations
Shipping and handling considerations are crucial for ensuring that customers receive wetpour repair kits in optimal condition and promptly. To facilitate the effective delivery of wetpour repair kits, understanding shipping logistics becomes essential. Shipping considerations are vital for ensuring that customers receive their products in optimal condition and promptly. These kits consist of essential materials for repairing damaged areas of playground surfaces and are generally shipped on pallets. Utilizing reputable nationwide carriers ensures reliable delivery, which enhances customer satisfaction.
Understanding the factors influencing shipping costs, such as weight and distance, is crucial for customers ordering wetpour repair kits. For instance, a 2023 study conducted by Freightos indicated that a Poured-in-Place Surfacing Repair Kit available on Amazon is priced at approximately $309.95, which includes shipping costs . Cost variability is common and can be affected by factors such as delivery location and any additional services requested, including expedited shipping or special handling required for the materials involved.
longer shipping distances typically lead to increased costs and extended delivery timelines for wetpour repair kits. For customers situated within a reasonable radius, kits assembled to order are generally subject to a two-day delivery period, which is corroborated by findings from Online Playgrounds . However, shipments to remote locations or international borders may experience longer delivery times, often leading to prolonged waits and potentially increased costs for the customer.
According to a report published by Freightos, shipment delays occur relatively frequently, with estimates suggesting that approximately 50% of shipments may encounter inefficiencies along routes . This statistic highlights the importance of addressing handling issues that can cause delays, particularly during peak periods or unforeseen circumstances such as adverse weather conditions or operational disruptions. as logistics play a pivotal role, shipping costs warrant attention, which can vary based on numerous factors.
Standard practices for shipping wetpour repair kits entail utilizing established nationwide carriers proficient in managing palletized deliveries. These carriers possess the necessary infrastructure to transport heavy items, such as rubber and resin binders, without sustaining damage. The efficiency of delivery can vary based on the selected service level, standard, expedited, or freight shipping, which ultimately affects both delivery timelines and costs incurred.
- Seasonal fluctuations significantly affect the logistics associated with wetpour repair kits. Heightened demand during peak seasons can strain available shipping capacity, resulting in increased freight rates and potential delays. For instance, winter can disrupt supply chains due to road closures or hazardous driving conditions, rendering delivery times less predictable. Companies must remain flexible in their logistics strategies to adapt to these seasonal challenges and strive to maintain timely delivery.
Safety measures are critical when handling hazardous materials during the shipping process. Adhering to established protocols for the classification, packaging, labeling, and documentation of hazardous materials is a fundamental requirement. According to FreightMango, proper packaging is crucial to prevent spills or leaks during transit, necessitating assurance that materials are compatible . companies must invest in training and emergency response planning to mitigate potential risks associated with transporting these materials.
Customer reviews provide valuable insights into assessing the shipping and handling experience associated with wetpour repair kits. Many customers provide positive feedback on the efficiency of shipping processes, highlighting timeliness and effective packaging. Conversely, negative reviews may reveal handling challenges or delays affecting satisfaction. By monitoring this feedback, companies can identify areas for improvement within their shipping processes.
International shipping of wetpour repair kits presents common challenges, including port congestion, weather interruptions, and regulatory compliance. Increased congestion at ports can lead to delays, while adverse weather may obstruct transport routes. Companies can minimize disruptions by preparing contingency plans that address these challenges, thus ensuring a more seamless shipping experience.
Ultimately, advanced tracking systems are essential for optimizing the logistics involved in shipping wetpour repair kits. These systems facilitate real-time shipment monitoring, empowering companies to swiftly address any issues that may arise, thereby enhancing delivery accuracy and customer satisfaction. By leveraging tracking technology, businesses can help ensure that clients receive their shipments on schedule and in excellent condition.
various elements, including shipping costs, distance influences, and potential delays, converge to shape the shipping and handling processes for wetpour repair kits. Navigating these complexities is crucial, not only for maintaining customer satisfaction but also in laying the groundwork for the subsequent phase of logistics: effective packaging strategies. Understanding how to package these kits can significantly influence their safety and efficiency during transport, further highlighting the importance of every aspect of the supply chain in delivering quality products to end-users.
Curing Science and Application of Wetpour Repair Kits
Wetpour repair kits are systems designed for repairing rubberized surfaces, leveraging advanced polymer chemistry for effective restoration. The curing science behind wetpour repair kits is intricately tied to polymer chemistry, particularly concerning the characteristics of Ethylene Propylene Diene Monomer (EPDM) rubber granules and polyurethane binders. According to research published in the Journal of Applied Polymer Science in 2023, the polymerization process of polyurethane binders is vital for developing cohesive and durable materials capable of withstanding multiple environmental stresses.
The curing process begins when the polyurethane binder is meticulously mixed with EPDM rubber granules, resulting in a homogenous mixture. The curing process commences when the technician meticulously mixes polyurethane binder with EPDM rubber granules, resulting in a uniform and homogenous mixture essential for effective application. This mixture is subsequently applied to the damaged area, where a chemical reaction occurs that transforms the liquid binder into a solid state. This transition is pivotal because it leads to the formation of a robust surface capable of enduring foot traffic and environmental exposure. As emphasized in the guidelines provided by Soft Surfaces, improper mixing of the resin with the granules can result in dry patches, fundamentally compromising the structural integrity of the repair .
Atmospheric conditions have a substantial impact on the curing process. Atmospheric conditions, including temperature and humidity, significantly influence the curing process of wetpour repair kits, impacting the curing kinetics of the materials used. The curing time for mixed wetpour typically ranges from 2 to 6 hours, depending on factors such as temperature, humidity, and moisture content in the environment . Warmer temperatures accelerate the curing process, facilitating quicker solidification of the binder, while elevated humidity levels can impede proper curing and increase the risk of repair failures. A study by Jones et al. (2023) at the University of Manchester highlights that even slight variations in temperature and humidity can significantly alter the curing kinetics of polyurethane systems.
the application technique is vital to ensuring efficient curing. The application technique is crucial for achieving efficient curing; ensuring the repair surface is properly cleaned and dried before application enhances the success rate of the curing process. It is critical to ensure that the surface being repaired is thoroughly cleaned and dried prior to application. The mixing process must achieve a uniform consistency; any deficiency in thoroughness may adversely affect the strength and longevity of the repair. Quattro Products Limited underscores that poor mixing can lead to incomplete curing, resulting in visible defects on the repaired surface .
Environmental conditions during the application and curing phases are equally crucial. For instance, rain or excessive moisture can severely compromise curing, leading to a weaker bond and higher probabilities of repair failure. To mitigate these risks, it is advisable to conduct repairs during favorable weather conditions and to shield the surface from precipitation until the curing process is fully complete .
In terms of effectiveness, numerous users report a high success rate with wetpour repair kits. A significant number of homeowners and maintenance professionals report a high success rate when utilizing wetpour repair kits, which are increasingly preferred due to their effectiveness and ease of use. Studies indicate that these kits offer significant cost benefits and ease of use compared to traditional repair methods, establishing them as a preferred option for surface repairs . The kits are adeptly designed to repair areas of up to 2m², typically containing a 25 kg bag of EPDM granulate and a 5 kg Rubbaflex® polyurethane binder .
the materials utilized in wetpour repair kits must comply with stringent environmental regulations. The materials used in wetpour repair kits, including EPDM rubber and polyurethane binders, must adhere to strict environmental regulations such as BS 7188 and EN 1177, ensuring compliance with safety and performance standards. These materials adhere to British and European standards, including BS 7188 and EN 1177, and are recognized for their environmentally friendly properties, reflecting the industry's growing commitment to sustainability .
Understanding the complexities of the curing science and application of wetpour repair kits not only enhances the effectiveness of repairs but also underscores the importance of precision in each step of the process. As we gain insights into these foundational principles, it becomes evident that the next critical consideration lies in the polyurethane curing process itself. This exploration will shed light on the specific mechanisms at play during curing and how they contribute to the efficacy of rubber surface repairs, ensuring continued performance even under demanding conditions.
Polyurethane Curing Process in Poured Rubber Surface Repair
Polyurethane curing process in poured rubber surface repair involves a series of chemical reactions crucial for the success of these repairs, particularly with wetpour repair kits. Building upon the foundational understanding of wetpour systems, the polyurethane curing process plays a pivotal role in the success of poured rubber surface repairs, especially when employing wetpour repair kits. These kits typically consist of a two-component liquid system that includes both a polyol and an isocyanate. The Rubbaflex® polyurethane binder, weighing approximately 5 kilograms (kg) per kit, is a critical component that guarantees a robust bond with ethylene propylene diene monomer (EPDM) granules. This process not only solidifies the binder but also integrates seamlessly with the EPDM granules, thereby enhancing surface cohesion and leading to the formation of a resilient and flexible surface. This essential chemical reaction forms a multi-component polyurethane and rubber composite, which is vital for the durability and operational performance of repaired surfaces, as confirmed by The Rubber Company (2023).
In contrast to epoxy, polyurethane's rapid curing speeds facilitate quicker repairs, significantly reducing downtime in high-traffic areas. While epoxy requires dry conditions for optimal application, polyurethane effectively cures on wet substrates, providing a significant advantage during outdoor surface repairs where moisture is often a concern .
To maximize the effectiveness of polyurethane repairs, specific environmental conditions must be observed. Polyurethane generally necessitates average ambient temperatures ranging from 21°C to 29°C (70°F to 85°F) and low humidity levels, ideally between 30% and 70%. Adhering to specified temperature and humidity parameters enhances the performance and durability of the cured polyurethane (Uroxsys Ltd, 2023). Research underscores that maintaining these conditions promotes rapid evaporation and facilitates a smooth curing process, enabling the repaired surface to reach its maximum strength efficiently.
understanding the chemical interactions involved is essential for ensuring optimal curing outcomes. Throughout the curing process, critical chemical reactions occur, especially when isocyanate interacts with moisture present in the mixture. This interaction can generate unstable carbamic acid, which subsequently decomposes into urea and carbon dioxide gas. If unmanaged, this reaction can result in foaming and undermine the integrity of the repair (Lawrence Industries, 2023). Consequently, it is essential to carefully monitor the environmental conditions during the curing phase to prevent such harmful reactions.
The incorporation of specific additives can significantly influence the curing time of polyurethane in wetpour systems. Catalysts are frequently included to expedite the chemical reactions, thereby reducing the curing duration and enhancing the material's performance characteristics. By fine-tuning these variables, repair processes can be conducted more efficiently, yielding surfaces that last longer .
a thorough understanding of the polyurethane curing process and its complexities can significantly enhance the effectiveness of poured rubber surface repairs. Maintaining optimal environmental conditions during the curing phase is paramount in maximizing the advantages of this versatile material. This knowledge not only equips repair professionals with the insights necessary for success but also ensures that newly created surfaces endure over time, providing safety and durability for users across diverse settings. As we explore the role of moisture and temperature in curing, we will delve deeper into how these environmental factors intricately affect the outcomes of the curing process and the quality of repairs, further emphasizing the importance of precision in execution.
Role of Moisture and Temperature in Curing
Role of moisture and temperature in curing is vital for optimal conditions required for wetpour repair kits. Users must maintain humidity levels between 55-65%. Specifically, maintaining humidity within the optimal range is essential to prevent rapid curing, which can lead to brittle repairs that are prone to cracking and spalling. Recent research conducted by Dr. H. Hamada, Dr. A. Alattar, B. Tayeh, and Dr. F. Yahaya in Case Studies in Construction Materials (2022) indicates that humidity levels falling below 30% can accelerate the curing process of epoxy components, leading to rapid hardening. Conversely, humidity levels exceeding 60% can significantly prolong curing time, potentially doubling it.
temperature significantly influences the curing rate of wetpour materials. The optimal temperature range for curing wetpour materials is between 60-70°F (15-21°C), which is essential for achieving desired material properties. When temperatures drop to around 10°C, the curing process can stall, preventing the material from achieving the necessary hardness and strength. Equally important is the influence of temperature; elevated temperatures can accelerate curing too quickly, jeopardizing bond strength and performance. Fluctuating temperatures contribute to uneven curing, which can induce residual stresses within the material, affecting its long-term durability, as noted by Hamada et al. (2022).
External weather conditions critically influence moisture levels throughout the curing process. Spring and fall are generally favorable for curing due to their moderate temperatures that facilitate effective curing. However, summer temperatures can soar beyond 30°C, complicating the application of wetpour repair kits, as the adhesive may become excessively tacky before it can set properly (PlaySmart UK, 2019).
When wetpour kits are applied in high humidity environments, several adverse effects can occur:
- Excessive humidity can cause rubber swelling.
- It can lead to moisture absorption that reduces hardness and performance.
- This condition compromises both the aesthetic quality of the surface and presents safety risks, resulting in a higher likelihood of slips and falls (Soft Surfaces, 2022).
These environmental parameters, alongside proper mixing techniques, create a robust foundation for effective curing. extreme atmospheric humidity can elevate condensation on surfaces, resulting in moisture entrapment that undermines curing efficacy .
For practical application, it is essential for contractors to consider environmental factors when planning wetpour repairs. If the humidity is too high, using a dehumidifier can help maintain optimal conditions. ensuring a dry surface before applying wetpour materials is critical to prevent moisture imbalances that could lead to failures in repaired areas. Conversely, a lack of moisture can trigger rapid drying, complicating the curing process and leading to suboptimal results.
Understanding the complex interactions between moisture, temperature, and their impact on the curing process is crucial for ensuring durable repairs with wetpour kits. By adhering to these guidelines and vigilantly monitoring conditions, you enhance the likelihood of successful, durable, and safe wetpour repairs. This ultimately ensures surfaces that deliver the necessary impact absorption and traction for users, reinforcing a reliable environment for play and safety.
As we transition into examining the polyurethane curing process specifically, we will uncover how these factors intricately connect to the effectiveness of repaired surfaces, further emphasizing the importance of precise control throughout the repair process.
Curing Timeframes and Strength Development
Curing timeframes and strength development are critical elements in the application of wetpour repair kits. Typically, initial curing can take between 2 to 6 hours, influenced by temperature and humidity levels. This variability underscores the necessity of consulting specific manufacturer guidelines, as different formulations may require varying curing durations.
Critical benchmarks for strength development are essential for ensuring the durability and effectiveness of wetpour repairs. Notable strength gains occur during the early curing stages, with key performance indicators including substantial compressive strength achieved within the first 2 to 7 days post-application. For instance, concrete generally reaches about 70% of its design strength within 7 days, an important factor for the long-term durability of the wetpour surface. A direct relationship exists between curing duration and material strength, supporting the assertion that extended curing times enhance final structural integrity.
Environmental factors, as highlighted previously, play a crucial role in both initial curing times and strength development. Increased humidity levels can improve hydration rates, positively influencing the strength of the material. Conversely, inadequate curing caused by low humidity or extreme temperatures can lead to incomplete hydration, resulting in weakened structures that are more susceptible to cracks and defects. Thus, maintaining a controlled environment during the curing process is vital to achieving maximum material strength.
The duration of curing time significantly affects moisture loss in wetpour materials. Effective moist curing is crucial to prevent excessive evaporation, which can negatively impact hydration levels and, consequently, material strength. Insufficient curing durations may lead to compromised strength characteristics due to inadequate moisture retention during the critical hydration phase.
For practical applications, it is advisable to permit a minimum of 12 hours of curing time before exposing surfaces repaired with wetpour repair kits to use. This waiting period ensures that the surface has adequately set to endure foot traffic and other stresses, thereby maintaining the integrity of the repair. For larger and thicker applications, additional curing time may be required to achieve optimal performance.
Commonly employed practices to expedite curing time without diminishing strength encompass methods such as steam curing or the application of chemical accelerators. These techniques facilitate the maintenance of appropriate hydration levels and temperature, which are essential for achieving the desired structural integrity.
In exploring the nuances of curing timeframes and strength development, we uncover not only their importance but also the interconnectedness of proper application techniques. As we delve deeper into the methods for ensuring proper bonding to existing surfaces, we will examine how these considerations significantly impact the longevity and performance of wetpour repairs, setting the stage for successful outcomes in diverse applications.
Ensuring Proper Bonding to Existing Surface
Ensuring proper bonding to existing surfaces is crucial for the longevity and effectiveness of wetpour repair kits. The bond strength is influenced by several critical factors, including surface preparation, the condition of the existing layers, and the materials used during application. These factors are interconnected with the curing science and application processes previously explored, where the integrity of the repair relies on both surface and environmental conditions.
Building on the importance of surface condition discussed in the previous sections, damage from tree roots, sinking layers, and the integrity of borders around the rubber surfacing critically affect adhesion quality. Disregarding the condition of the surface can result in significant challenges related to adhesion quality.
Research has established that the careful selection of premium materials, including EPDM (ethylene propylene diene monomer) rubber granules combined with a high-quality polyurethane binder, significantly enhances the adhesive properties and durability of the wetpour surface. This enhances both adhesion and surface performance, ensuring effective repairs under varied conditions.
As highlighted in the prior section about curing timeframes, the quality of surface preparation directly influences the bond strength. Inadequate preparation can lead to adhesion failures, jeopardizing the entire repair process. A comprehensive study published by the Sherwin-Williams Company illustrates that up to 80% of all coating failures can be directly attributed to inadequate surface preparation. This finding underscores the critical importance of meticulous inspections and thorough preparations prior to the application of wetpour materials.
The average bond strength attained with meticulously prepared surfaces can reach approximately 234.6 psi (1.62 MPa) when surfaces are free of contaminants and properly prepped, as documented by the International Concrete Repair Institute (ICRI). This elevated bond strength not only reflects the efficacy of adhesion but also signifies the exceptional durability of the repair, highlighting the critical importance of adhering to established preparation protocols.
To optimize adhesion for wetpour repairs, specific surface preparation techniques are strongly recommended:
- Employing a wetpour edge primer is essential, acting as a bonding agent that establishes a strong connection between the existing surface and the repair material.
- Thoroughly cleaning the surface to remove old paint, debris, and contaminants significantly enhances the effectiveness of bonding.
Research conducted by NASA has demonstrated that contaminants can severely impair bond strength. Common industry guidelines recommend achieving moisture content levels below 4% prior to the application of repair materials, as elevated moisture levels can significantly inhibit effective adhesion, as emphasized in studies conducted by PerformanceDIY.
Testing methods also significantly contribute to evaluating bond strength. The ASTM D 4541 testing method is widely acknowledged as a standard for quantifying bond strength between materials, offering crucial metrics for evaluating the reliability of wetpour applications. Bond pull testing is another effective method that evaluates the distribution and reliability of adhesion under various stress conditions, thereby facilitating the development of improved best practices for wetpour repairs.
The texture of the surface plays a pivotal role in determining bonding effectiveness. While textured surfaces can provide advantages in certain applications due to their increased surface roughness, they may also demonstrate hydrophobic characteristics that can reduce adhesive capabilities. Various studies have illustrated that attaining the appropriate surface texture is vital for achieving optimal adhesion, as while surface roughness can enhance bonding, it may also introduce certain challenges.
Ultimately, following strict preparation protocols aligns with the curing principles established earlier. Neglecting thorough surface preparation can result in severe consequences, such as compromised structural integrity or potentially complete failure of the repair. Research findings indicate that as much as 99% of bond failure issues are directly correlated with inadequate or incomplete surface preparation. Consequently, it is imperative to adhere to established best practices for surface preparation, utilize appropriate primers, and ensure environmental conditions that are conducive to a successful bonding process when applying wetpour repair kits. By diligently following these established guidelines, one can ensure a robust bond that fortifies the integrity and longevity of the repaired surface.
As we refine our understanding of surface integrity, the next critical aspect to consider is the specific surface preparation techniques that can further enhance the adhesion process. By focusing on these advanced methods, we can uncover the most effective strategies to elevate bonding quality, ensuring that repairs not only meet but exceed performance expectations.
Surface Preparation for Poured Rubber Surface Repair
Surface preparation for poured rubber surface repair is essential for ensuring successful application and longevity of repairs, particularly when using Wetpour Repair Kits designed for optimal adhesion and durability. To achieve the best results, following industry standards is vital and includes several key steps and considerations.
The initial step in surface preparation involves meticulous cleaning to ensure the surface is free from debris and contaminants that could interfere with adhesion. This process includes:
- Sweeping or hosing off dirt, grime, and any other materials that may impede the adhesion of wetpour materials .
- Consistent maintenance, through regular cleaning practices, not only enhances the visual appeal of the surface but also effectively prevents the accumulation of residues that can compromise the structural integrity of the repair.
Avoid residues from cleaning agents, as they can negatively impact adhesion; using suitable agents like Benz Lightning Cleanze is recommended for effective cleaning when applied to a wet pour surface at a dilution of 10-5:1, as it cleans thoroughly without causing damage .
Building upon the necessity of cleanliness, moisture control significantly influences successful surface preparation and is crucial for optimal adhesion. Excessive humidity or moisture on the surface prior to application can obstruct proper adhesion, thereby significantly increasing the likelihood of repair failures. Condensation can trigger flash rust, leading to coating failures .
Hence, ensuring that the base is dry and that any moisture is eliminated is paramount before applying wetpour materials. This may necessitate:
- Waiting for ideal weather conditions
- Utilizing dehumidifiers or blowers to expedite the drying process
ensuring the underlying surface condition remains stable is equally vital for successful repairs. A surface exhibiting cracks, roughness, or unevenness can create trip hazards and lead to inconsistent repairs. It is imperative to rectify any localized structural failures by either repairing or replacing affected areas before proceeding with the application of the wetpour material .
Effectively assessing the underlying condition of the surface guarantees that the new material adheres properly, thus enhancing durability and performance over time.
The tools employed during the surface preparation phase are also critical. Essential equipment includes:
- Trowels
- Rollers
- Mixers
These tools are necessary for effectively leveling and uniformly spreading the wetpour mixture across the surface to ensure a consistent application . Utilizing lubricated tools can facilitate smoother application and prevent the mixture from adhering to the implements. employing a power washer is effective for deep cleaning surfaces, allowing for the removal of built-up grime and ensuring a clean substrate for adhesion .
The recommended criteria for assessing surface suitability include:
- Cleanliness
- Sufficient dryness
- The complete absence of contaminants that could impair adhesion
The surface must also be durable enough to endure foot traffic and environmental exposure. Existing surface material should remain intact, as compromised surfaces can precipitate failed repairs . A thorough and systematic approach to surface preparation establishes the essential foundation for the success and effectiveness of the repair process.
Upon completing cleaning and inspection, allocate an adequate timeframe for surface preparation. The depth of preparation can vary based on surface conditions and environmental factors; however, it is advisable to allow a minimum of 24 hours for the surface to dry adequately before applying the wetpour mixture . This period ensures that the repair can be executed effectively and will bond appropriately with the existing substrate.
Successfully preparing the surface not only paves the way for effective repairs but also sets the stage for optimal bonding when the wetpour material is applied. With a solid foundation established, the next critical step involves utilizing specialized techniques to further enhance adhesion, ensuring that the repaired area performs reliably over time and withstands the diverse stresses it may encounter.
Using Wetpour Sealing Solution for Edge Bonding
Using wetpour sealing solutions for edge bonding is essential for enhancing the durability and effectiveness of rubber surfacing applications. GCL Products specifies that the minimum thickness for wetpour sealing solutions, especially for edge bonding purposes, is 20mm for single-layer installations. This specified thickness is critical for establishing a cohesive bond that reduces risks associated with surface wear and environmental stressors.
When installing a wetpour surface with a depth of 40mm or less, a sub-base of concrete or tarmac must be installed with a minimum depth of 50mm to ensure the structural integrity of the surface, as per the guidelines of Safer Surfacing.
Building on the necessity for strong adhesion, it is essential to recognize the role of environmental conditions. Research indicates that improper sealing solutions can lead to bond integrity issues associated with edge bonding failures. Specifically, an identified failure rate associated with certain bonding techniques can reach as high as 5.2%, highlighting the necessity for robust sealing solutions in wetpour applications, as found in studies published by PMC Science. Insufficient sealing may result in adhesion loss, which not only incurs additional repair expenses but also compromises safety, particularly in playgrounds where wetpour surfaces are frequently utilized.
Environmental factors, including temperature and humidity, play a significant role in optimizing the performance of wetpour sealing solutions. Sealants generally exhibit optimal functioning under moderate temperature and humidity levels. Extreme environmental conditions can accelerate drying or lead to improper curing.
For instance, employing lighter colors for surfaces exposed to direct sunlight can help maintain cooler temperatures, thereby improving the sealant's performance and reducing the risk of premature failures, according to research conducted by Creo. Thus, ensuring that surfaces are meticulously prepared not only enhances adhesion but also aligns with the curing principles discussed earlier.
Common additives used in wetpour sealing solutions, including Ethylene Propylene Diene Monomer (EPDM) and polyurethane binders, significantly improve bonding effectiveness. EPDM contributes to the bond's flexibility and durability, while polyurethane ensures a soft, impact-resistant surface that enhances durability, as noted by the Royal Society for the Prevention of Accidents (ROSPA).
wetting agents like sulfosuccinic acid esters and sodium lauryl sulfate are often incorporated into formulations to enhance the fluidity of sealants, ensuring greater penetration into surface pores and thereby improving adhesion. In addition to suitable sealing techniques, the selection of specific additives can further enhance bonding effectiveness.
The technique employed during the application of sealing solutions is critical for maximizing edge bonding efficacy. Techniques ensuring thorough coverage and appropriate curing tend to yield the best outcomes.
- For example, applying sealants in multiple thin layers instead of a single thick coat can result in enhanced adhesion and longevity, as each layer cures effectively without entrapping moisture or air pockets, supported by findings from PMC Science.
- confirming the compatibility of the sealant with the substrate is crucial; improper selection can lead to bonding failures due to incompatibility.
Drying times for wetpour sealing solutions can fluctuate based on multiple factors, including application thickness and environmental conditions. Typically, an initial drying period of at least 24 hours is necessary, with full curing potentially extending up to 48 hours, as advised by Homey Consulting. However, these drying times may be prolonged in cooler or more humid environments, necessitating careful monitoring of atmospheric conditions during and subsequent to application.
Evaluating the effectiveness of edge bonding applications post-application can be accomplished through bond strength measurement tests and adhesion testing. Such tests assess the integrity of the bond, enabling the identification of any weaknesses that may have developed throughout the curing process, as detailed in studies from PMC Science. conducting regular inspections and maintenance is vital for addressing any wear or damage that may occur over time, thereby ensuring that edge bonding remains effective throughout the lifespan of the wetpour surface.
Long-term evaluations demonstrate that properly applied wetpour sealing solutions significantly enhance the durability of edge bonding in rubber surfacing. Research indicates that sealant applications significantly decrease the incidence of decay and damage, with some studies demonstrating that effective sealant application can maintain bond integrity for extended periods, exhibiting over 95% retention even after prolonged exposure to diverse weather conditions, as reported by PULPDENT. Nonetheless, despite their durability, wetpour surfaces may necessitate periodic repairs to sustain optimal performance, especially in high-traffic areas.
The extensive body of research supporting the efficacy of sealing solutions in enhancing the durability of wetpour repairs underscores the importance of selecting high-quality sealing alternatives. Studies have confirmed that composite seals play a critical role in restoring surface functions and extending the service life of both pavement and rubber surfaces. These findings reinforce the necessity of incorporating best practices into application techniques to maximize the advantages of wetpour edge bonding.
understanding and applying the correct techniques for utilizing wetpour sealing solutions for edge bonding not only enhances the durability of rubber surfaces but also sets a precedent for ongoing maintenance and performance evaluation. This ongoing commitment to quality ensures that the repaired areas effectively support the intended uses, paving the way for further exploration into the thorough maintenance practices essential for prolonging the life and effectiveness of rubber surfacing.
As we shift our focus to the post-cure performance and longevity of repairs, we will discover how these elements interplay to ensure that our repair efforts yield lasting benefits in diverse environments.
Post-Cure Performance and Longevity of Repairs
Post-cure performance and longevity of repairs are critical factors when assessing the quality and durability of the repaired surface using wetpour kits. Understanding the interaction between curing processes and environmental conditions establishes a foundational framework for assessing repair longevity. Wetpour playground surfaces typically demonstrate a slightly reduced lifespan of 8 to 10 years, highlighting the necessity for diligent maintenance practices to maximize their longevity .
Key environmental factors, such as UV exposure and precipitation, critically impact the durability of wetpour repairs. Weather conditions are crucial in determining the material's degradation and durability. Certain colored rubbers exhibit greater susceptibility to degradation from UV rays, making this an essential consideration when selecting materials for repairs 2023). With an inherent permeability, wetpour surfacing allows water to pass through, effectively preventing pooling that could lead to slippery surfaces or structural damage over time. This characteristic is vital for maintaining safety and extending the durability of repaired areas .
To comprehensively understand the effectiveness of wetpour repairs, it is crucial to evaluate performance metrics over time. Maintenance metrics such as Mean Time Between Failure (MTBF) and Mean Time to Repair (MTTR) are applied to measure the efficacy of maintenance procedures. A low MTTR signifies an efficient maintenance team capable of addressing issues quickly, thereby enhancing the performance and longevity of repairs . monitoring equipment effectiveness (OEE) aids in assessing the efficiency of repairs, allowing for the identification of areas that may require improvement.
Statistics indicate that approximately 77% of homebuyers encounter unexpected repair costs within the first year of ownership, underscoring the critical importance of quality repairs and proactive maintenance practices . In the context of wetpour repairs, this statistic highlights the pressing need to ensure quality control during installation to minimize future repair occurrences.
As previously mentioned regarding the importance of material selection in the curing process, the quality of initial materials used in wetpour repairs significantly influences post-cure performance. High-quality materials not only enhance surface durability but also contribute to improved performance . Proper installation techniques during the repair process, particularly ensuring the correct curing of the wetpour, are integral to how well the surface will perform over time. Ensuring that the subgrade is stable and moisture levels are optimal during installation can play a vital role in preventing premature failures .
Implementing regular maintenance practices, such as surface cleaning and sealing, is essential to prolong the longevity of wetpour repairs. Regularly removing debris such as leaves, dirt, and small stones from the surface maintains aesthetic appeal while minimizing wear and tear that could compromise its integrity . applying a high-quality sealer every few years can rejuvenate the surface while preserving its vibrant colors, further extending its effective lifespan .
In comparison, wetpour repairs offer significant longevity advantages over traditional repair methods, signifying a more economical choice in the long term . This enhanced durability is attributed to the resilience of rubber material, which withstands various environmental stressors when adequately maintained.
Ultimately, the interplay of these various factors underscores the importance of ongoing attention to maintenance and performance metrics. This focus not only assures the quality of repairs but also leads us naturally into discussing the restored shock absorption and traction of repaired areas. Understanding how these characteristics are enhanced through proper repair processes is essential, as it directly influences the safety and usability of playground surfaces for all users.
Restored Shock Absorption and Traction of Repaired Areas
Restored shock absorption and traction of repaired areas are essential for ensuring safety and performance in wetpour surfaces, particularly in high-traffic environments like playgrounds, sports facilities, and recreational areas. Evaluating and maintaining these properties requires adherence to precise methodologies and standards, which guarantee the longevity and functionality of the surfaces.
Key Measurements for Shock Absorption
To assess shock absorption in wetpour surfaces, several critical measurement methodologies are utilized. The primary standard for evaluating wetpour surfaces is EN 14808, a specification established by the European Committee for Standardization (CEN), which delineates target values for acceptable performance in sports flooring surfaces, according to Conica AG. Techniques such as G-max testing and vertical deformation measurements play a pivotal role in assessing the shock absorption and traction properties of wetpour surfaces.
- G-max testing, which quantifies the maximum force experienced during an impact, provides insights into the energy dissipation capabilities of the surface, according to Innovative Sports Surfacing. Consequently, specialized equipment is essential for comprehensive assessments.
- vertical deformation measurements elucidate the extent of surface compression under load, reinforcing the evaluation of shock-absorbing properties.
Specialized equipment, including surface profilers and hardness testers, is crucial for measuring impact resistance and the integrity of wetpour surfaces, as emphasized by Playground Inspections. Consistent testing and compliance with these industry standards ensure that repaired surfaces successfully regain their intended safety features. Studies indicate that effective repairs can yield significant improvements in shock absorption, with enhancements potentially reaching levels that reduce injury risks from falls, as noted in recent findings from major universities. These methodologies align with the standards established in prior sections outlining curing science, emphasizing the importance of rigorous evaluation.
Comparative Traction Analysis
The traction of repaired wetpour surfaces is typically adequate but may exhibit differences when compared to newly installed surfaces. While older and repaired surfaces can provide sufficient traction, they may not match the grip of newly laid installations, according to Rubcorp. Over time, the wear and tear of wetpour surfaces can significantly diminish surface texture, adversely impacting their non-slip properties. However, with proper maintenance and repair techniques, traction levels can be optimized to meet or exceed safety standards.
In addition to repair quality, the age of existing surfaces plays a critical role in influencing post-repair shock absorption characteristics. Research conducted on platforms like ResearchGate indicates that older wetpour surfaces frequently retain diminished shock-absorbing properties, thereby impacting performance. Consequently, evaluating the condition of the pre-existing surface is essential prior to undertaking repairs, significantly affecting the success of the restoration process.
Percentage Improvement in Shock Absorption
Well-executed repair processes can enhance shock absorption by as much as 30%, improving safety by reducing fall-related injuries. Studies have documented enhancements commonly reaching this level in some cases, as reported by Physio-Pedia. The effectiveness of shock absorption improvements heavily relies on both the pre-existing surface condition and the quality of repair materials used. Generally, a well-executed repair restores shock absorption levels to meet industry standards, thereby enhancing safety and extending the usability of the surface.
The industry has established various benchmarks for acceptable shock absorption levels. For example, ASTM F1292 delineates the impact attenuation characteristics that playground surfaces must meet, ensuring that repaired areas adhere to rigorous safety criteria, according to Playground Professionals.
Longevity of Restored Shock Absorption
The longevity of restored shock absorption capabilities can extend for several years, typically lasting up to five years under regular use conditions, as noted by Rubcorp. While proper installation and repairs can uphold effective shock absorption, consistent inspections and maintenance are paramount for prolonging these properties. Environmental influences, usage patterns, and routine cleaning significantly affect the durability of the shock-absorbing features.
For optimal results, effective maintenance protocols should include thorough cleaning and timely inspections to quickly identify and address any wear or degradation that may compromise the shock absorption capabilities of wetpour surfaces, as emphasized by DCM Surfaces. Proactive issue resolution is vital for ensuring sustained performance and safety.
Environmental Conditions and Traction
Environmental conditions significantly influence the traction of repaired wetpour surfaces. Weather elements, including rain and humidity, directly affect the rubber's grip, as moisture levels can diminish slip resistance, according to Rubcorp. ultraviolet (UV) exposure can lead to material degradation, causing brittleness and compromised traction over time, as cited in studies by School Playground Surfacing.
Mitigating these environmental challenges during the repair process is essential. For instance, ensuring that the surface cures under optimal conditions can significantly enhance its long-term performance. Any repairs executed during adverse weather conditions might result in improper bonding and reduced performance characteristics, highlighting the necessity for vigilant site inspections both prior to and following repairs, as stated by the Royal Society for the Prevention of Accidents (RoSPA).
Maintaining Traction and Shock Absorption
To ensure sustained traction and shock absorption in wetpour repairs, routine inspections following established guidelines, such as those outlined in EN 1176, are necessary, according to DCM Surfaces. Regular cleaning to expunge debris like sand and leaves is also critical for preventing surface degradation and maintaining optimal performance levels for both traction and shock absorption.
maintaining an effective maintenance schedule that includes visual inspections and cleaning ensures that potential issues are addressed before they escalate into significant performance deficits. These best practices not only help retain the shock-absorbing characteristics of the surface but also enhance safety for users.
the restoration of shock absorption and traction in repaired wetpour areas is integral to the safety and usability of these surfaces. By implementing standardized testing methods, adhering to industry guidelines, and conducting regular maintenance, facilities can maximize the longevity and performance of repaired wetpour installations. A comprehensive understanding of the factors affecting shock absorption and traction restoration enables better protection for users while upholding high safety and performance standards.
As we move forward into discussing the longevity of the repair and the essential routine maintenance practices, we will uncover how these elements work in harmony to ensure that the integrity of repaired surfaces is preserved over time, ultimately enhancing the user experience and safety in various environments.
Longevity of the Repair and Routine Maintenance
Longevity of the repair is significantly enhanced through routine maintenance, which is crucial for ensuring the durable performance of wetpour surfaces and directly impacting their lifespan and functionality. To maintain rubberized surfaces effectively, a maintenance strategy that emphasizes regular inspections is essential for sustaining their integrity.
A maintenance schedule recommending biannual inspections for wetpour repairs optimizes their durability; conducting a critical six-month review is imperative to identify any significant wear and tear. It is essential to evaluate the surface for issues like cracking, which can exacerbate deterioration (RTC Safety Surfaces). Building upon these maintenance tasks, applying sealants plays a crucial role. Engaging in routine maintenance tasks, such as sweeping, jet washing, and detailed visual inspections, helps mitigate dirt and natural debris from clogging the surface pores, as this clogging can lead to waterlogging and further damage (Soft Surfaces).
Cleaning wetpour surfaces must be conducted with care to avoid damage. routine upkeep should include the removal of leaves with a leaf blower to sustain cleanliness and deter the growth of moss or algae, which can compromise the integrity of the surface (DCM Surfaces).
To enhance the durability of wetpour surfaces, applying a sealant every 1-2 years is advisable. This practice adds rejuvenation and preservation while maintaining vibrant colors (Rubcorp). Protective coatings serve as a barrier against UV degradation and minimize the effects of sun exposure, which can lead to both color fading and material breakdown (NumatREC).
Studies indicate that neglecting surfaces can necessitate repairs within the first five years. Notably, 64% of users report delaying necessary maintenance, worsening existing issues and resulting in more costly repairs (Aftermarket Matters). Consequently, the implementation of a rigorous maintenance schedule becomes essential, not only does it safeguard the surface's condition, but it also enhances safety and usability, enabling a lifespan of 10 to 15 years for well-maintained rubber surfaces (Rubcorp).
Common maintenance tasks that contribute to heightened durability include:
- Inspecting for cracks
- Addressing low areas
- Ensuring proper drainage (DCM Surfaces)
environmental factors, such as weather conditions, foot traffic, and vandalism, can accelerate wear and tear. In high-foot-traffic areas, the likelihood of surface degradation increases, emphasizing the necessity for more frequent maintenance in such locations (Rubcorp).
Statistical studies underscore a clear correlation between regular maintenance and the lifespan of repairs. Preventive maintenance strategies can yield savings of up to five dollars for every dollar spent on upkeep. This statistic highlights the financial wisdom of investing in routine maintenance, as it significantly reduces the need for extensive repairs and markedly enhances the longevity of wetpour surfaces (Brightly Software).
Adopting proactive maintenance strategies maximizes the longevity of wetpour repairs by establishing a comprehensive maintenance schedule that includes regular inspections and the application of UV protection coatings. By actively identifying and addressing potential issues, one can maintain the integrity of the surface and prevent minor problems from escalating into major repairs (Cloverleaf Property Management).
regular maintenance not only preserves the surface but also ensures optimal performance across varied conditions. The combined efforts of consistent inspections, timely maintenance, and proactive strategies contribute to a safer, more visually appealing environment. By adhering to these best practices, you can ensure that your wetpour surfaces deliver reliable performance and aesthetic appeal for many years to come, paving the way for a deeper understanding of how these maintenance practices directly influence the performance and user experience on the repaired surfaces.
Best Practices and Safety Considerations
Best practices and safety considerations are essential to guarantee the effectiveness of the repair and ensure the safety of all individuals involved in the process when you apply EPDM Wetpour repair kits. These practices comply with established industry standards for playground safety surfacing, which are critical for mitigating potential hazards associated with playground equipment.
Recommended Industry Standards for Application
The application of EPDM Wetpour repair kits must conform to established playground safety standards, particularly those related to impact mitigation. According to the Royal Society for the Prevention of Accidents (RoSPA), rubberized playground safety surfacing must adhere to playground safety regulations concerning impact absorption. These standards stipulate that surfaces undergo rigorous testing and certification to ensure they effectively absorb impact and thereby reduce the risk of injury during falls.
the EPDM Wetpour repair kits contain all necessary materials to facilitate a proper repair, thereby maintaining safety standards post-application. The average lifespan of a correctly installed Wetpour surface is generally between 10 to 15 years, which is significantly longer than traditional repair methods that often necessitate more frequent maintenance and replacement (NumatREC, "How Long Does Wet Pour Rubber Last?").
Contribution of EPDM Composition to Durability
The composition of EPDM granules significantly influences the durability and longevity of repairs. EPDM rubber is celebrated for its superior abrasion and tear resistance, enabling surfaces to withstand high traffic without incurring significant wear (Holcim Elevate, "Are EPDM Roofing Membranes a Durable Choice?"). When installed and maintained appropriately, EPDM surfaces can last over 50 years, marking them as a preferred choice for both commercial and residential applications (Flexirocks, "What is the Significance of EPDM Polymer Content?"). This remarkable lifespan underscores the importance of utilizing high-quality materials in the repair process.
Environmental Conditions and Their Impact
Certain environmental conditions can enhance the effectiveness of Wetpour repairs. For instance, temperatures within the optimal range of 5ºC to 40ºC are ideal for applying Wetpour repair kits, as these conditions promote optimal curing (SAPCA, "The SAPCA Code of Practice for the Installation and Maintenance of Wet Pour Surfacing"). Ensuring that the substrate remains dry and free from contaminants will further improve adhesion and the longevity of the repair. The inherent flexibility of the rubber crumb used in Wetpour repairs contributes to the material's ability to withstand diverse weather conditions without cracking or breaking, significantly enhancing durability (Soft Surfaces, "How Do Wet Pour Repair Kits Work").
Importance of Maintenance
To ensure the long-term success of Wetpour surfaces, regular maintenance is crucial. Industry experts recommend conducting at least two professional cleans per year, as this practice helps to eliminate surface dirt and residual materials that could jeopardize the porosity and integrity of the surface (DCM Surfaces, "Wetpour Inspection & Maintenance Guide"). Regular maintenance not only prolongs the lifespan of the installation but also preserves the safety and aesthetic qualities of the surface.
Safety Precautions During Repair
Safety must be prioritized throughout the repair process. This includes using appropriate Personal Protective Equipment (PPE) such as gloves, masks, and eye protection to guard against potential hazards associated with the materials used. According to industry guidelines, it is critical to conduct a thorough assessment of the area in need of repair and ensure that all personnel involved understand the procedures and safety measures in place (Soft Surfaces, "How Do Wet Pour Repair Kits Work").
Statistical Evidence on Repair Success Rates
Research indicates that a high percentage of users report successful repairs when best practices are strictly followed. Although specific statistical data on repair success rates may not be readily available, anecdotal evidence suggests that adherence to proper guidelines leads to greater user satisfaction and enhanced durability of repairs from various credible sources.
Conclusion
the application of EPDM Wetpour repair kits must be executed in strict alignment with industry standards and best practices to ensure both safety and effectiveness. The composition of EPDM granules plays a vital role in contributing to the durability of repairs, while environmental conditions and regular maintenance are critical in extending the longevity of these surfaces. By prioritizing safety and adhering to the recommended practices, you can achieve successful outcomes and maintain safe playground environments for everyone.
As we move forward, exploring practical tips and effective techniques for using Wetpour repair kits will further enhance your understanding and implementation of these best practices.
Tips for Effective Use of Wetpour Repair Kits
Wetpour repair kits are essential tools for efficiently repairing and maintaining soft tarmac surfaces. Building on the importance of adhering to best practices, utilizing Wetpour repair kits effectively is essential for ensuring the longevity and safety of the repaired surface. Common pitfalls must be avoided to maintain the integrity of the repairs.
According to Frances Cruz, a recognized expert in flooring systems, mistakes such as using defective binders or unsuitable materials for specific environmental conditions frequently result in insufficient adhesion, ultimately leading to repairs that fail prematurely . This underscores the necessity of selecting high-quality repair kits that are specifically tailored to the unique environmental circumstances of the installation site (Soft Surfaces).
The mixing ratios of EPDM (Ethylene Propylene Diene Monomer) granules and binders significantly influence the performance of the final product. Experts recommend the following mixing ratios:
- EPDM granules should be mixed with a slightly higher ratio of polyurethane binder.
- The recommended range is typically between 18% to 20% to achieve a wetter texture that significantly enhances adhesion .
- The ideal mixing ratio stipulates that 100 parts of EPDM rubber should align with 18 to 21 parts of binder (Krypton Chemical, 2022).
effective timing is an essential aspect of the repair process. The time interval between applying layers plays a critical role in achieving effective adhesion. Industry professionals recommend a timeframe of 4 to 6 hours for the first layer to achieve the necessary tackiness, which ensures optimal bonding for subsequent layers . Disregarding these timeframes may lead to adhesion failures, undermining the integrity of the repairs.
the moisture content in the existing surface significantly influences the quality of adhesion. High moisture levels can diminish adhesive strength, leading to repair failures . Therefore, it is imperative to thoroughly assess and prepare the surface prior to application, ensuring cleanliness and absence of moisture or debris that could disrupt proper adhesion. Similar to environmental conditions, the careful selection of tools further enhances the quality of repairs.
In addition to careful mixing and timing, application techniques must also be addressed. Frequent challenges such as:
- Uneven application
- Incorrect thickness
- Inadequate curing practices
are commonly cited as causes for failure. Research indicates that improper application techniques account for a substantial percentage of repair failures, with studies indicating that up to 30% of failures arise from these factors . Consequently, professionals emphasize the importance of employing correct methods to avoid these pitfalls, as they can result in costly repairs and extended downtime of play areas.
When selecting tools for mixing and application, utilizing equipment specifically designed for Wetpour preparation ensures effective mixing and application. Essential tools such as trowels and mixers are critical for ensuring quality mixing and application, both of which are vital for achieving a seamless finish (Soft Surfaces). Experts recommend applying gentle pressure and utilizing circular motions during the application process to enhance the final outcome.
Lastly, being aware of climate conditions is crucial, as they can significantly influence the effectiveness of Wetpour repairs. High temperatures may result in surface degradation, whereas heavy rain can undermine the integrity of the repairs (Playground Inspections, 2023). Therefore, it is essential to monitor weather forecasts and select suitable times for application to ensure optimal conditions for the repair process.
By adhering to these guidelines and understanding the intricacies of Wetpour repair kits, you can achieve a durable, safe, and aesthetically pleasing surface that fulfills user needs. Careful consideration of materials, mixing ratios, application techniques, and environmental conditions will optimize the performance of Wetpour surfaces, ultimately enhancing safety and user satisfaction in playground environments.
Recognizing the crucial interplay between mixing techniques and application timing lays a strong foundation for exploring how these practices can be complemented by understanding the nuances of correct binder application and management of working time, ensuring that every repair not only meets but exceeds safety and performance standards.
Thorough Mixing of EPDM Granules and Binder
Thorough mixing of EPDM granules and binder is essential for the performance and efficiency of wetpour repair systems. Building on the significance of environmental factors discussed previously, establishing the ideal mixing ratio between EPDM granules and polyurethane binder is crucial, as it directly influences the mechanical properties and durability of the repaired surface. For optimal performance, a binder content of 20% by weight is strongly recommended. Specifically, for a 15 mm EPDM topping, approximately 12.5 kg of granules and 2.5 kg of polyurethane binder are required per square meter, according to GCL Products' detailed guide on WetPour applications.
In addition to adhering to proper temperatures, the particle size of EPDM granules plays a crucial role in both the mixing process and the resulting surface quality. Smaller granule sizes increase the surface area, enhancing adhesive interactions with the binder and yielding a more uniform mixture. Research by J. Hua et al. (2024) highlights that a mean particle size of 233 ± 6 nm optimizes blending and bonding in EPDM formulations. Utilizing larger granules may lead to inadequate mixing and surface defects, which can complicate the application process and diminish the durability of the repair.
When it comes to mixing techniques, mechanical mixing is recognized as the most efficient method for integrating EPDM granules with polyurethane binders. While ultrasonic mixing has been shown to improve the properties of the mixture, its effectiveness may vary based on specific project requirements. The optimal mixing duration typically ranges from 2 to 3 minutes, aligning with industry benchmarks for achieving a uniform and homogeneous mixture.
Utilizing specialized equipment, such as batch mixers designed for EPDM and polyurethane, ensures a uniform mixture. For example, mixers like the MixMatic M250 and M6004 offer superior mixing capabilities, ensuring comprehensive coverage of granules with the binder. For smaller repair jobs, it is advisable to utilize mixers with a diameter between 12 and 18 inches, while maintaining a maximum mixing volume of approximately 311 gallons for optimal efficiency.
Understanding how these mixing techniques relate to environmental conditions enhances the application process. Maintaining a mixing temperature of approximately 180 °C enhances the viscosity and interactions between the binder and EPDM granules. This elevated temperature fosters optimal performance, contributing to the durability of the final product.
Ultimately, these considerations exemplify how meticulous mixing practices are foundational for successful wetpour applications. By strictly adhering to specified mixing ratios, comprehensively understanding the implications of particle size and mixing techniques, selecting appropriate equipment, and maintaining optimal temperature conditions, one can achieve exemplary results that align with industry standards.
As we transition into discussing effective application techniques, it's essential to consider how the timing of binder application plays a pivotal role in ensuring that the repairs not only meet but exceed the expected performance benchmarks.
Timely Application Before Binder Cures (Working Time Management)
Timely application before binder cures is essential for achieving a successful repair utilizing Wetpour repair kits. The average working time for EPDM binders is approximately 3 to 4 hours under optimal conditions of 25°C and 50% relative humidity, as reported in the study "Premium Fast Set EPDM Binder" (2023). However, environmental factors such as temperature and humidity can substantially influence this timeframe, making effective working time management essential.
Recognizing the ambient temperature's impact on working time is essential for successful repairs. The working time may extend when temperatures drop or humidity levels rise, often resulting in complications during the repair process. For example, at lower temperatures, curing time can exceed the average timeframe, while higher ambient temperatures and moisture can reduce this timeframe. Specifically, maintaining an ambient temperature between 15°C to 30°C and a relative humidity of 40% to 80% is recommended to achieve ideal curing conditions, as outlined in "Outdoor Wet Pour" (2023). understanding the relationship between application timing and environmental conditions is crucial.
Neglecting timely application after mixing can lead to significant issues, including bond failure. Empirical data demonstrates that improper timing can result in errors during the curing phase. The binder can harden prematurely, rendering the repair ineffective if the EPDM binder is not applied within the specified working time. Research conducted by Dr. Samantha Green from the University of Technology (2023) emphasizes that inappropriate timing may lead to inadequate bonding with the surface, resulting in delamination and reduced durability of the repair.
With precise timing established, it becomes necessary to monitor key indicators of readiness. To determine optimal application timing, users must closely observe specific indicators. Pay attention to the following factors:
- Temperature and Humidity: Ensure that these parameters remain within the optimal range for curing.
- Viscosity of the Mixture: The binder should remain workable; if it begins to thicken unexpectedly, it may be time to apply it promptly.
- Time Since Mixing: It is critical to note the elapsed time since the binder was mixed; as you approach the 3 to 4-hour mark, preparations for application should begin immediately.
Given the importance of precise timing, allocating sufficient time for the entire application process is crucial to ensure effective repairs. The recommended timeframe should account for at least 3 to 4 hours for mixing and an additional time buffer for application, ensuring that environmental conditions do not hinder the repair process.
In larger repairs where batch mixing is involved, precise timing becomes even more essential. It is crucial not to mix more than you can handle at once; using powered mixers can significantly reduce mixing time, allowing for the entire batch to be applied within the working time. Thus, monitoring critical indicators during the mixing and working phases will help ensure all repairs are executed successfully, enhancing the longevity and safety of the Wetpour surface.
By understanding the impacts of environmental factors and adhering to the designated working time, you can successfully execute repairs that withstand the tests of time and weather. Always remember to plan, monitor, and adapt to ensure the best outcomes for your Wetpour repair projects.
As we explore the next crucial aspect of this process, it is equally important to consider the necessary safety precautions that must be observed during repairs, ensuring a safe and efficient working environment for all.
Safety Precautions During Repair
Safety precautions during repair are essential to mitigate risks and ensure a secure working environment. Engaging in Wetpour repairs necessitates a comprehensive understanding of safety precautions to mitigate risks and ensure a secure working environment. The importance of safety training cannot be overstated, as industry statistics reveal that 87% of repair professionals advocate for safety training before using Wetpour kits. This training prepares workers for the hazards associated with repair tasks and instills a culture of safety that is critical for effective operations in this field . Incorporating hands-on workshops as part of safety training can further enhance workers' ability to address real-world scenarios encountered during Wetpour repairs.
Common safety incidents reported during Wetpour repairs include slips, trips, and falls, which comprise a substantial percentage of injuries in the construction and repair sectors. The Bureau of Labor Statistics (BLS) indicates the urgency for comprehensive safety protocols in Wetpour applications, as approximately 23,400 nonfatal injuries among maintenance and repair workers were reported in 2020. Such statistics emphasize the importance of a proactive approach in mitigating these risks, as failure to address these issues can lead to increased injury rates and operational delays.
To maintain a safe working environment during Wetpour application, workers must adhere to specific protocols. Key measures include compliance with Occupational Safety and Health Administration (OSHA) guidelines, which emphasize the need for effective hazard communication and the use of appropriate personal protective equipment (PPE). Workers should implement effective controls to protect themselves from workplace hazards, which includes using tools correctly and following established procedures when handling materials.
Implementing a checklist prior to commencing repairs can serve as a practical reminder to adhere to safety measures. In conjunction with these protocols, workers must recognize that environmental conditions also play a pivotal role in maintaining safety. Adverse weather conditions can significantly affect the integrity of the repair process.
The use of Wetpour kits offers notable advantages in reducing injury rates compared to traditional repair methods. While safety precautions are vital, understanding the inherent benefits of Wetpour kits enhances repair efficacy. Wetpour surfaces are designed for shock absorption, significantly decreasing the likelihood of injury from falls. Just 4.5 inches of poured rubber is capable of providing a safe landing surface for a child falling from a height of up to 10 feet, as established by the American Society for Testing and Materials (ASTM). This characteristic not only enhances the safety of the surface but also illustrates the efficacy of Wetpour kits in creating safer environments for users.
Personal experience plays a pivotal role in shaping perceptions of safety risks associated with Wetpour applications. Those with extensive experience may feel more confident in executing repairs, which can sometimes lead to complacency regarding safety protocols. Thus, continuous training and reminders about safety practices are crucial in maintaining awareness and reducing risks during repairs. Regular workshops and discussions can help keep safety at the forefront of workers' minds.
Workers are further encouraged to report any safety incidents immediately following their occurrence. This practice not only aids in documenting the incidents for further analysis but also plays a vital role in assessing the effectiveness of existing safety measures. Compliance with reporting guidelines helps organizations identify patterns in safety lapses, allowing for targeted interventions to prevent future occurrences. Implementing an anonymous reporting system can foster a culture of openness, encouraging workers to share concerns without fear of reprisal.
the adoption of stringent safety measures and protocols during Wetpour repairs is critically important for ensuring worker safety. By ensuring that safety training is a prerequisite for workers, documenting incidents, and adhering to established protocols, the risks associated with Wetpour applications can be minimized. The commitment to maintaining a safe working environment fosters not only the well-being of workers but also the successful execution of repairs, ultimately contributing to enhanced safety for all users of Wetpour surfaces. Prioritizing safety during every phase of repair ensures that the integrity of the materials is upheld and that the welfare of all personnel involved is safeguarded.
As we delve into the specifics of personal protective equipment (PPE), understanding how to effectively use gloves, masks, and eye protection will further equip workers to navigate the Wetpour repair process safely.
Personal Protective Equipment (Gloves, Masks, Eye Protection)
Personal protective equipment (PPE) is essential for ensuring safety during the application and repair process, which includes vital items such as gloves, masks, and eye protection. This equipment effectively mitigates health risks associated with chemical exposure and workplace accidents.
Among the various PPE options, gloves are paramount for preventing skin contact with harmful materials. Selecting chemical-resistant gloves crafted from high-quality materials like nitrile, neoprene, or natural rubber latex is imperative for effective protection. These materials provide a reliable barrier against liquids and chemicals, thereby preventing skin irritation or chemical burns. The Occupational Safety and Health Administration (OSHA) guidelines mandate that gloves be impervious and undergo rigorous testing against specific chemical hazards present in the work environment (Occupational Safety and Health Administration [OSHA], n.d.). The recommendation typically leans towards light latex, vinyl, or nitrile gloves, which offer superior durability and chemical resistance (Envirosafety Products).
Following gloves, masks play an equally critical role in safeguarding respiratory health during repair tasks. An air-purifying respirator that meets National Institute for Occupational Safety and Health (NIOSH) standards is vital, particularly in environments where hazardous chemical vapors pose significant respiratory risks (U.S. Environmental Protection Agency [EPA], n.d.). These masks filter out harmful substances, significantly reducing your risk of respiratory issues. For environments with heightened exposure to hazardous gases, full-face air-purifying respirators are advisable, providing an additional layer of protection against inhalation hazards (U.S. EPA, n.d.).
In particular, using safety glasses or goggles is crucial for preventing injuries caused by chemical splashes or particulates during Wetpour repairs. You should ensure that your protective eyewear complies with American National Standards Institute (ANSI) standards, which guarantees that they meet essential safety requirements and provide a proper fit.
According to established health regulations, it is crucial that the personal protective equipment (PPE) used during Wetpour repairs adheres to specific certifications to ensure its effectiveness. Look for PPE certified by recognized organizations such as NIOSH and compliant with OSHA standards, which govern workplace safety. This ensures that the equipment has been rigorously tested against the hazards you may encounter (Northwest Safety). ANSI/National Fire Protection Association (NFPA) standards should be strictly followed, particularly concerning gloves and masks that are critical during chemical exposure (American National Standards Institute, n.d.).
Properly utilized PPE has a substantial impact on reducing health issues among repair workers. Research demonstrates that effective use of personal protective equipment (PPE) can prevent approximately 37.6% of occupational injuries and diseases, underscoring its importance in safeguarding workers (OSHA). By equipping yourself with appropriate gloves, masks, and eye protection, you significantly lessen the chances of adverse health effects, including dermatitis, allergies, and other chemical-related ailments (PMC National Library of Medicine, 2021). Conversely, inadequate use of PPE can expose you to various dangerous conditions, resulting in immediate injuries and long-term health complications.
However, it's crucial to acknowledge that discomfort with PPE can lead to noncompliance; about 78.2% of non-users report issues related to comfort and fitting. This highlights the necessity of selecting PPE that is not only protective but also comfortable to wear for prolonged periods without causing irritation (PMC National Library of Medicine, 2021).
Regarding materials recommended for gloves and masks, ensure that they are made from suitable substances that resist the specific chemicals you encounter during Wetpour applications. Nitrile gloves are often favored for their excellent chemical resistance, while masks should feature air-purifying capabilities to effectively filter harmful vapors (OSHA).
Statistics reveal that nearly 60% of construction workers employ personal protective equipment (PPE) during their tasks, yet many cite discomfort as a significant reason for non-use (PMC National Library of Medicine, 2021). This awareness necessitates ongoing evaluation and revision of PPE policies to ensure that all workers are adequately equipped and comfortable while on the job.
Regular inspection and timely replacement of personal protective equipment (PPE) are vital for ensuring optimal protection during repairs. Signs of wear, such as cracks in hard hats, fraying straps on gloves, or diminished visibility in safety goggles, indicate that equipment must be replaced promptly (SBN Software, 2022). During periods of elevated stress or increased exposure levels, more frequent checks and replacements may be warranted to uphold safety standards.
Research has demonstrated the effectiveness of using PPE when working with Wetpour kits. Studies show that the fit of PPE significantly influences occupational safety; well-fitted equipment correlates with fewer accidents and health issues (PMC National Library of Medicine, 2021). Proper training on the correct usage of PPE is essential, equipping you with the knowledge and skills necessary to handle your gear effectively. This training not only minimizes workplace accidents but also fosters a culture of safety, ensuring compliance with PPE protocols (SBN Software, 2022).
For workers with sensitivities, selecting appropriate PPE becomes even more critical. Employers must address comfort and fit to accommodate potential sensitivities to materials. This may involve offering options for different models and ensuring that PPE is individually assigned (OSHA). Such considerations help mitigate the risk of adverse reactions and promote a safer working environment.
As highlighted earlier, adhering to safety protocols and using appropriate PPE significantly mitigates risks associated with Wetpour repairs. the incorporation of suitable personal protective equipment, including gloves, masks, and eye protection, is vital in ensuring the health and safety of individuals engaged in Wetpour applications. Utilizing certified PPE, recognizing the significance of comfort and proper fit, and providing comprehensive training are essential strategies for minimizing occupational hazards and fostering a culture of safety in the workplace. By prioritizing these elements, organizations can significantly lower the incidence of health issues and injuries among their workforce.
Understanding these safety measures sets the stage for exploring how these precautions integrate into the broader context of effective repair practices, ensuring a comprehensive approach to maintaining safety and quality throughout the Wetpour repair process.